How to Optimize Your UV Flatbed Printer for High-Volume Production
In the realm of digital printing, UV flatbed printers have revolutionized the way we approach large-scale and high-detail printing projects. These versatile machines offer unparalleled flexibility in terms of substrate compatibility, print quality, and durability. However, optimizing a UV flatbed printer for high-volume production is a multifaceted endeavor that requires attention to various aspects, from printer settings and ink management to workflow efficiency and maintenance practices. This comprehensive guide delves into the essential strategies to maximize the performance and productivity of your UV flatbed printer in a high-volume environment.
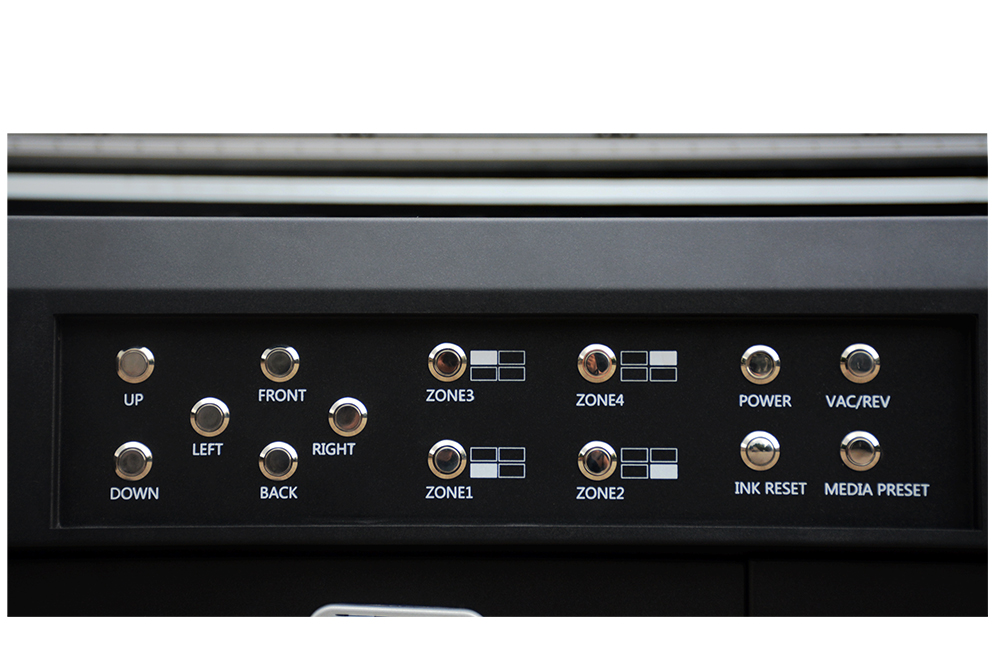
1. Understanding Your Printer’s Capabilities
Before diving into optimization techniques, it’s crucial to have a thorough understanding of your UV flatbed printer’s specifications and capabilities. Familiarize yourself with its maximum print speed, resolution, supported substrate types, and ink system. Knowing these fundamentals will help you set realistic expectations and make informed decisions throughout the optimization process.
2. Calibrating for Consistency
Consistency is key in high-volume production. Regularly calibrate your printer to ensure accurate color reproduction and print quality. This involves:
Color Calibration: Use calibration tools and software to adjust the printer’s color output, ensuring it matches your desired standards or industry-specific color profiles.
Print Head Alignment: Misaligned print heads can lead to blurry or uneven prints. Perform regular alignments to maintain precision.
Media Settings: Different substrates require different print settings. Create and save profiles for each type of material you frequently use, including adjustments for ink adhesion, drying times, and temperature settings.
3. Optimizing Print Settings
Tweaking the printer’s settings can significantly impact production efficiency and quality:
Resolution: While higher resolutions offer better detail, they also slow down the printing process. Find the optimal balance between resolution and speed for your specific job requirements.
Pass Count: The number of times the print head passes over the substrate affects both quality and productivity. Reducing pass count can increase speed but might require adjustments to ink flow and layering to maintain quality.
Ink Density: Adjusting ink density settings can help achieve the desired color saturation and opacity without wasting ink or compromising on speed.
4. Efficient Ink Management
Ink is a significant cost factor in high-volume printing. Effective ink management strategies include:
Ink Type Selection: Choose inks that are suited for your production needs, considering factors like durability, cure time, and substrate compatibility.
Ink Usage Monitoring: Implement systems to track ink consumption and detect leaks or inefficiencies early.
Cleaning and Maintenance: Regularly clean the print heads and ink system to prevent clogs and ensure smooth ink flow, reducing the risk of downtime and waste.
5. Streamlining Workflow
Optimizing your workflow can drastically improve production efficiency:
Pre-Press Preparation: Invest time in preparing files correctly. Ensure high-resolution images, proper color profiles, and efficient file formats to avoid printing delays.
Automation Tools: Utilize automation software to manage job queues, automate file processing, and minimize manual intervention.
Batch Processing: Group similar jobs together to reduce setup times between different print runs.
6. Enhancing Productivity with Software
Modern UV flatbed printers often come with sophisticated software that can be leveraged for optimization:
RIP Software: A good Raster Image Processor (RIP) can significantly enhance print quality and speed by optimizing image data before sending it to the printer.
Print Management Systems: These systems offer features like job tracking, cost estimation, and remote printer management, which are invaluable in a high-volume environment.
Customization Tools: Utilize variable data printing (VDP) capabilities to personalize prints without sacrificing efficiency.
7. Maintaining Optimal Performance
Regular maintenance is essential to keep your UV flatbed printer running at peak performance:
Daily Checks: Perform daily inspections of the print heads, ink levels, and overall machine cleanliness.
Preventive Maintenance: Establish a schedule for preventive maintenance tasks, such as replacing worn parts, cleaning the printer’s interior, and updating software.
Training: Ensure that operators are well-trained in both the operation and maintenance of the printer to prevent human error and extend the machine’s lifespan.
8. Managing Waste and Sustainability
In high-volume production, managing waste is not only environmentally responsible but also economically beneficial:
Ink Recovery: Implement systems to recycle or reuse excess ink.
Substrate Scrap Management: Minimize substrate waste through efficient cutting and nesting techniques.
Energy Efficiency: Optimize printer settings to reduce energy consumption, such as adjusting cure times and using power-saving modes when possible.
9. Quality Control Measures
Maintaining high standards of quality control is crucial:
Inline Inspection: Use inline inspection tools to catch defects early in the production process.
Sample Testing: Regularly print test samples to ensure consistency and make adjustments as needed.
Customer Feedback: Collect feedback from customers to identify areas for improvement and adapt your processes accordingly.
10. Scaling Up with Scalability in Mind
As your production volume grows, so should your printer’s capacity:
Modular Upgrades: Look for printers that allow for modular upgrades, such as additional print heads or larger ink tanks, to increase output without having to invest in a whole new machine.
Scalable Software: Ensure your print management software can handle increased job volumes and complexity.
Outsourcing Options: Consider partnerships with outsourcing providers for overflow work, ensuring you can meet peak demands without overburdening your in-house capabilities.
Optimizing a UV flatbed printer for high-volume production is a continuous process that involves fine-tuning technical settings, implementing efficient workflows, and maintaining rigorous quality control measures. By understanding your printer’s capabilities, managing resources effectively, and investing in ongoing training and maintenance, you can significantly enhance productivity, reduce costs, and ensure consistent print quality. Remember, the key to success lies in balancing advanced technology with strategic planning and a commitment to excellence. As you navigate this optimization journey, stay adaptable and open to innovations that can further push the boundaries of your UV flatbed printing capabilities.