Can UV Flatbed Printers Print White Ink? Unveiling the Truth Behind the Technology
In the ever-evolving landscape of digital printing, UV flatbed printers have emerged as a game-changer, offering unparalleled versatility across industries. From creating vibrant signage to crafting personalized merchandise, these machines have redefined what’s possible in the world of print. However, one question often arises: Can UV flatbed printers print white ink? This query is particularly relevant for professionals seeking to achieve opaque, bright white prints on dark or transparent substrates—a challenge traditional printers often struggle with. In this blog, we’ll delve into the mechanics, applications, and limitations of white ink printing with UV flatbed technology, demystifying the process for curious minds and industry enthusiasts alike.
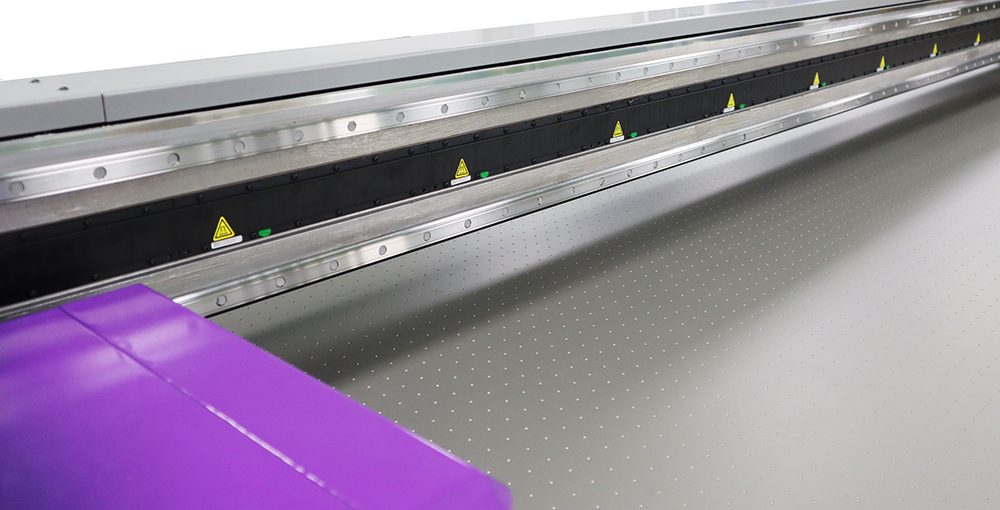
The Science Behind UV Flatbed Printing
Before addressing white ink specifically, it’s essential to understand how UV flatbed printers function. Unlike conventional printers, which rely on solvent-based or water-based inks, UV printers use ultraviolet light to cure (or solidify) ink instantly upon contact with the substrate. This process ensures rapid drying times, minimal ink absorption into the material, and enhanced durability—attributes ideal for printing on a vast array of surfaces, including glass, metal, wood, and plastics.
The technology’s versatility lies in its ability to print directly onto three-dimensional objects, eliminating the need for pre-coating or priming in many cases. But what about white ink? Can this critical component fit seamlessly into the UV printing workflow? Let’s explore further.
The Role of White Ink in UV Printing
White ink serves as a foundational element in UV printing, especially when working with non-white substrates. Its primary function is to provide opacity, allowing vibrant colors to “pop” against dark or clear backgrounds. Without white ink, colors would appear translucent or muted, compromising the visual impact of the print.
In UV flatbed printing, white ink is typically formulated with titanium dioxide (TiO₂) pigments, which reflect light and create a dense, opaque layer. However, achieving consistent white ink performance is no small feat. The ink must be viscous enough to settle evenly without clogging printheads yet fluid enough to flow smoothly through the printer’s nozzle system. This delicate balance is what sets apart high-quality UV printers from their counterparts.
How UV Flatbed Printers Handle White Ink
Modern UV flatbed printers are engineered to accommodate white ink through specialized mechanisms. One common approach is the use of dedicated white ink channels within the printhead. These channels operate independently of color ink channels, ensuring precise layering of white ink beneath or above CMYK (cyan, magenta, yellow, key/black) colors.
Another innovation is the “white underbase” technique, where the printer first lays down a layer of white ink to act as a canvas for subsequent color layers. This method is particularly effective for printing on dark materials like black acrylic or colored glass. Conversely, “white overprint” can be used to highlight specific design elements or create a glossy, raised effect.
Some advanced UV printers also feature automatic ink circulation systems to prevent pigment settling in the white ink reservoir, a common issue with denser inks. These systems keep the ink in constant motion, ensuring consistent viscosity and print quality over extended periods.
Applications of White Ink in UV Printing
The ability to print white ink opens up a world of creative possibilities across industries. In advertising and signage, white ink enables the production of eye-catching backlit displays, where colors appear vivid even under ambient lighting. In the automotive sector, it’s used to create custom graphics on dark-colored vehicle wraps, while in the fashion industry, designers leverage white ink for intricate patterns on transparent accessories like phone cases and sunglasses.
The medical and pharmaceutical fields also benefit from white ink printing, particularly for labeling opaque or dark-colored bottles and containers. The ink’s opacity ensures compliance with regulatory requirements for clear, legible text, even on challenging substrates.
Moreover, white ink is a cornerstone of the growing 3D printing and prototyping market. When combined with UV flatbed technology, it allows designers to simulate raised textures, embossed logos, or tactile finishes on promotional items and packaging prototypes.
Challenges and Limitations
Despite its advantages, white ink printing with UV flatbed technology isn’t without its hurdles. One of the primary challenges is ink cost. White ink formulations often contain expensive pigments like titanium dioxide, driving up material expenses. Additionally, the ink’s viscosity requires more frequent printhead maintenance to prevent clogs, adding to operational overhead.
Another limitation is substrate compatibility. While UV printers excel on a wide range of materials, certain surfaces—such as highly textured woods or uneven metals—may require pre-treatment to ensure proper ink adhesion. Moreover, extreme temperatures or humidity levels can affect ink drying times and overall print quality.
Finally, achieving consistent white ink coverage on large-format prints can be tricky. Operator expertise plays a crucial role in calibrating the printer settings to avoid banding, streaking, or uneven opacity.
The Future of White Ink in UV Printing
As technology advances, the future of white ink in UV printing looks promising. Innovations like LED-UV curing systems offer faster, more energy-efficient drying, reducing production time and costs. Meanwhile, researchers are exploring eco-friendly alternatives to titanium dioxide pigments, aiming to create sustainable white ink formulations without compromising opacity.
Another exciting development is the integration of artificial intelligence (AI) into UV printers. AI algorithms can analyze substrate types, ink properties, and ambient conditions in real time, automatically adjusting print parameters for optimal white ink performance. This level of automation not only streamlines the printing process but also reduces waste and enhances productivity.
Conclusion
In conclusion, UV flatbed printers are indeed capable of printing white ink, and they do so with remarkable precision and versatility. From advertising to manufacturing, the applications of white ink in UV printing are as diverse as they are impactful. While challenges like ink cost and substrate compatibility persist, ongoing technological advancements continue to address these limitations, paving the way for even more innovative uses of white ink in the years to come.
Whether you’re a seasoned print professional or a curious hobbyist, understanding the capabilities and nuances of white ink printing with UV technology can unlock new creative possibilities and business opportunities. So, the next time you’re faced with a project requiring vibrant, opaque prints on dark or transparent materials, remember: UV flatbed printers have got you covered—in white and beyond.