How Does a UV Flatbed Printer Handle Different Types of Materials
In the realm of digital printing, UV flatbed printers have emerged as a versatile and powerful tool, capable of producing high-quality prints on a wide array of materials. Unlike traditional printing methods that are often limited to specific substrates, UV flatbed printers utilize ultraviolet curing technology to print on virtually any flat or slightly curved surface. This adaptability has revolutionized the printing industry, enabling businesses to expand their product offerings and cater to diverse customer needs. In this article, we will explore how a UV flatbed printer handles different types of materials, delving into the technical aspects, printing processes, and the unique considerations for each material type.
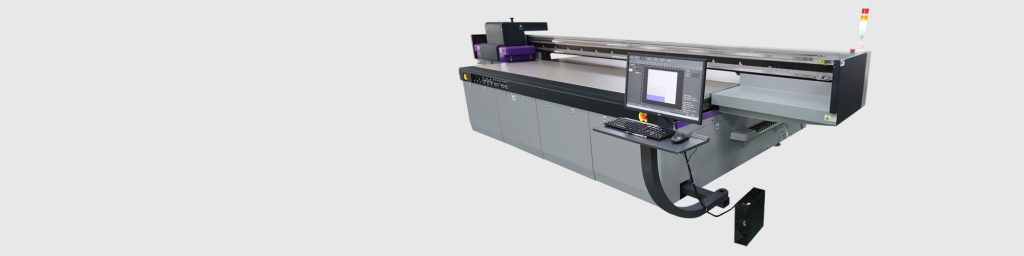
Understanding UV Flatbed Printing Technology
Before diving into the specifics of material handling, it is essential to grasp the fundamentals of UV flatbed printing. This technology employs a series of LED or mercury vapor lamps that emit ultraviolet light to instantly cure the ink as it is deposited onto the material. The ink used in UV flatbed printers is specially formulated to react with UV light, solidifying immediately upon exposure. This rapid curing process eliminates the need for drying time, allowing for faster production speeds and the ability to print on a variety of substrates without the risk of ink bleeding or smudging.
Key Components and Their Roles
Print Heads: High-resolution print heads, often utilizing piezoelectric technology, deposit droplets of UV ink onto the material with precision. These heads can adjust the droplet size, enabling detailed and vibrant prints.
UV Lamps: Strategically placed UV lamps cure the ink as it is printed. Depending on the printer model, these lamps can be positioned before, after, or both relative to the print heads, ensuring complete curing.
Material Handling Systems: Adjustable platforms, vacuum systems, and clamps secure the material in place during printing, preventing movement and ensuring accurate print registration.
Ink Delivery System: A sophisticated ink delivery system manages the flow of UV ink to the print heads, maintaining consistent color and quality throughout the print run.
Software and Control Systems: Advanced software controls the entire printing process, from file preparation to print execution, ensuring precise color matching and efficient job management.
Handling Different Types of Materials
The versatility of UV flatbed printers lies in their ability to print on a multitude of materials. Each material presents unique challenges and requires specific adjustments to the printing process. Below are some common material types and how UV flatbed printers handle them:
1. Rigid Materials
Examples: Acrylic, glass, metal, wood, plastic, and ceramic tiles.
Handling: Rigid materials are typically placed directly onto the printer’s flatbed. Vacuum systems or mechanical clamps hold the material securely in place to prevent any movement during printing. For materials like glass ** orConsider metalations,**: which The can printer be’ reflectives, bed special must coatings be or level primers and may free be of applied to ensure proper ink adhesion and to prevent ink from running or smearing.
any debris that could interfere with the printing process. Additionally, the UV lamps’ intensity and position may need to be adjusted to ensure even curing, especially for thicker or more dense materials.
2. Flexible Materials
Examples: Vinyl, fabric, leather, and soft plastics.
Handling: Flexible materials often require a different approach. They may be mounted onto a rigid substrate or stretched and secured using a system of clamps or adhesive. For materials like vinyl, which can shrink or expand with temperature changes, it is crucial to maintain a consistent printing environment.
Considerations: The tension and flatness of the material must be carefully controlled to avoid wrinkles or misalignments. Special inks and curing profiles may also be necessary to ensure proper adhesion and durability of the print.
3. Porous Materials
Examples: Paper, cardboard, and uncoated woods.
Handling: Porous materials absorb ink differently than non-porous ones. To prevent excessive ink absorption and ensure vibrant colors, a pre-treatment or primer may be applied to the surface. This step helps to seal the pores and provides a better surface for the ink to adhere to.
Considerations: The ink’s viscosity and the printer’s ink delivery system must be fine-tuned to avoid over-saturation. Porous materials may also require additional curing passes to ensure complete ink solidification.
4. Heat-Sensitive Materials
Examples: Certain plastics, fabrics, and other materials that can warp or melt under high temperatures.
Handling: UV flatbed printers equipped with LED lamps, which generate less heat than mercury vapor lamps, are ideal for heat-sensitive materials. Additionally, the printing speed and UV lamp intensity can be adjusted to minimize heat exposure.
Considerations: It is crucial to monitor the material’s temperature throughout the printing process and make adjustments as necessary to prevent damage.
5. Textured or Uneven Materials
Examples: Stone, textured plastics, and fabrics with a raised pattern.
Handling: Printing on textured or uneven surfaces requires precise control of the print heads’ height and angle. Some UV flatbed printers are equipped with sensors that automatically adjust the head position to maintain a consistent distance from the material surface.
Considerations: The ink’s flow rate and droplet size may need to be adjusted to ensure even coverage and penetration into the textured areas. Multiple print passes or layers may also be necessary to achieve the desired color saturation and clarity.
Special Techniques and Considerations
White Ink: For materials that are transparent or require a base layer for vibrant color reproduction, such as glass or clear plastics, white ink is often used as a primer. This step ensures that the colors appear true and vibrant.
Varnish and Spot UV: To add a finishing touch, some UV flatbed printers can apply a clear varnish or spot UV effect. This technique enhances the print’s visual appeal by adding a glossy finish to specific areas, creating a contrast between matte and glossy surfaces.
Multi-Layer Printing: For complex designs or materials that require a high level of detail, multi-layer printing techniques can be employed. This involves printing different elements of the design in separate passes, allowing for more precise control over color, ink coverage, and curing.
The versatility of UV flatbed printers in handling a wide range of materials is a testament to their advanced technology and design. By understanding the unique characteristics of each material and making the necessary adjustments to the printing process, businesses can produce high-quality prints that meet the demands of even the most discerning customers. Whether working with rigid substrates like metal and glass, flexible materials like vinyl and fabric, or porous and heat-sensitive surfaces, UV flatbed printers offer a level of flexibility and precision that is unmatched by traditional printing methods. As the technology continues to evolve, we can expect even more innovative applications and material compatibilities, further expanding the boundaries of digital printing.