How Does a UV Flatbed Printer Work? An Inside Look
How Does a UV Flatbed Printer Work? An Inside Look
In the realm of digital printing, UV flatbed printers have emerged as versatile and powerful tools, capable of producing high-quality prints on a wide variety of substrates. From rigid materials like glass, metal, and plastic to flexible media such as vinyl and fabric, these printers have revolutionized the way businesses approach product customization, signage, and promotional materials. To fully grasp the capabilities and advantages of UV flatbed printers, it is essential to understand their inner workings, the technology that drives them, and the processes involved in producing stunning prints. This article provides an inside look at how a UV flatbed printer operates, covering its key components, printing process, ink systems, and the role of UV curing.
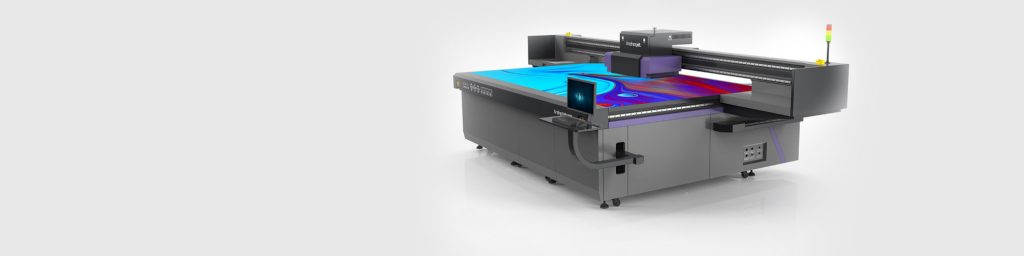
Key Components of a UV Flatbed Printer
A UV flatbed printer is a complex machine consisting of several crucial components that work together seamlessly to produce high-quality prints. These components include:
Print Head and Ink System: The print head is responsible for depositing ink onto the substrate. It typically contains multiple nozzles that can dispense different colors and types of ink. The ink system supplies the print head with ink and ensures that it is delivered in a controlled and precise manner.
Substrate Handling System: This system is responsible for positioning the substrate accurately beneath the print head. It may include mechanisms for loading, unloading, and moving the substrate during the printing process. Some advanced systems can handle substrates of various sizes and shapes, including irregular or three-dimensional objects.
UV Curing System: One of the defining features of a UV flatbed printer is its UV curing system. This system uses ultraviolet light to instantly cure the ink after it has been deposited onto the substrate. The UV light triggers a chemical reaction in the ink, causing it to harden and adhere to the surface.
Control System: The control system manages the overall operation of the printer, including the movement of the print head, the flow of ink, and the activation of the UV curing system. It typically includes software that allows users to design and prepare their prints, as well as adjust settings such as ink density, print speed, and curing time.
Frame and Enclosure: The frame and enclosure provide structural support for the printer and protect its components from dust, debris, and other contaminants. They also help maintain a stable environment for consistent printing results.
The Printing Process
The printing process on a UV flatbed printer can be broken down into several key steps:
Preparation: Before printing can begin, the substrate must be properly prepared. This may involve cleaning the surface to remove any contaminants that could affect ink adhesion, applying a primer if necessary, and ensuring that the substrate is properly positioned on the printer’s bed.
Design and File Setup: The design for the print is created using graphic design software and saved in a compatible file format. This file is then uploaded to the printer’s control system, where it can be adjusted and previewed to ensure that it will print correctly.
Ink Deposition: Once the design is ready, the printing process begins. The print head moves across the substrate, depositing ink in a precise pattern according to the design. The printer’s control system ensures that the ink is applied accurately and evenly, taking into account factors such as ink density, drop size, and print speed.
UV Curing: Immediately after the ink is deposited, the UV curing system is activated. UV lights, typically positioned either above or beside the print head, emit ultraviolet light that cures the ink instantly. This process hardens the ink and ensures that it adheres firmly to the substrate. The curing time and intensity can be adjusted to achieve the desired print quality and durability.
Post-Processing: Depending on the substrate and the desired finish, additional post-processing steps may be required. These can include cutting the printed material to size, applying a protective coating, or laminating the print for added durability.
Ink Systems and UV Curable Inks
The ink system is a critical component of a UV flatbed printer, as it directly affects the quality and durability of the prints. UV curable inks are specifically designed to be cured by ultraviolet light, and they offer several advantages over traditional solvent-based inks:
Fast Curing: UV curable inks cure instantly when exposed to UV light, allowing for faster printing speeds and reduced production time.
Durability: Cured UV inks are highly resistant to fading, scratching, and chemicals, making them ideal for outdoor applications and environments where the print may be exposed to harsh conditions.
Versatility: UV curable inks can be formulated to adhere to a wide range of substrates, including those that are difficult to print on with traditional inks.
Environmental Benefits: UV curable inks typically have lower volatile organic compound (VOC) emissions compared to solvent-based inks, making them a more environmentally friendly option.
The Role of UV Curing
UV curing is a crucial aspect of the printing process on a UV flatbed printer. It not only hardens the ink but also ensures that it adheres properly to the substrate. The UV light triggers a chemical reaction in the ink, causing it to polymerize and form a strong, durable bond with the surface.
There are several factors that can affect the effectiveness of UV curing, including:
Intensity and Duration: The intensity and duration of the UV light must be carefully controlled to ensure proper curing. Too much light can cause the ink to over-cure, leading to cracking or discoloration, while too little light can result in under-curing, which may cause the ink to remain tacky or fail to adhere properly.
Ink Chemistry: The chemistry of the UV curable ink plays a significant role in the curing process. Different inks may require different levels of UV exposure to achieve optimal curing.
Substrate Material: The type of substrate can also affect the curing process. Some materials may absorb more UV light than others, which can impact the amount of light that reaches the ink. In these cases, adjustments to the curing process may be necessary to ensure proper adhesion and durability.
Advantages of UV Flatbed Printers
UV flatbed printers offer several advantages over traditional printing methods, including:
Versatility: UV flatbed printers can print on a wide range of substrates, including rigid and flexible materials, as well as irregular or three-dimensional objects.
High Quality: UV curable inks produce sharp, vibrant prints with excellent color accuracy and detail.
Durability: Cured UV inks are highly resistant to fading, scratching, and chemicals, making them suitable for a variety of applications.
Fast Production: The instant curing process allows for faster printing speeds and reduced production time.
Customization: UV flatbed printers enable businesses to create customized products and promotional materials with ease, helping them stand out in a competitive market.
Conclusion
UV flatbed printers have become an invaluable tool for businesses seeking high-quality, durable prints on a wide range of substrates. By understanding the inner workings of these printers, including their key components, printing process, ink systems, and UV curing mechanisms, businesses can make informed decisions about their printing needs and leverage the full potential of UV flatbed technology. As the digital printing industry continues to evolve, UV flatbed printers will remain at the forefront, offering versatility, quality, and durability that meet the demands of modern businesses and consumers.