How Does Temperature and Humidity Affect UV Flatbed Printing
UV flatbed printing has revolutionized the printing industry, offering high-quality, durable prints on a wide range of substrates. This technology utilizes ultraviolet (UV) light to cure inks instantly, providing numerous advantages such as faster production times, reduced waste, and the ability to print on diverse materials. However, like any sophisticated printing process, UV flatbed printing is susceptible to environmental factors, particularly temperature and humidity. Understanding how these elements impact the printing process is crucial for achieving optimal print quality and efficiency.
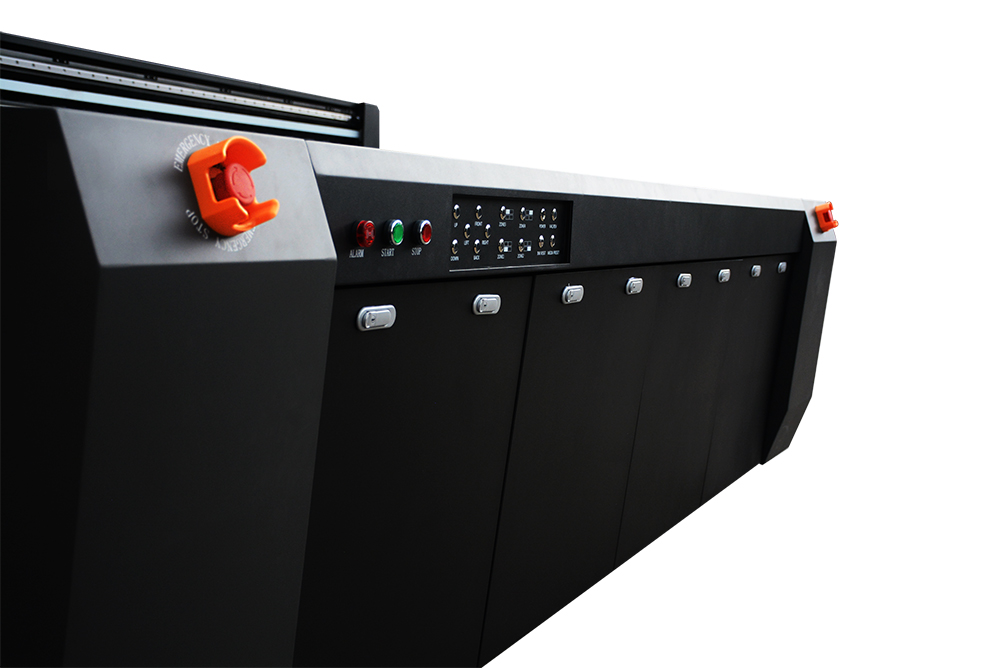
The Science Behind UV Ink Curing
To comprehend the effects of temperature and humidity on UV flatbed printing, it’s essential to delve into the basics of UV ink curing. UV inks contain photoinitiators that react when exposed to UV light. This reaction triggers a chemical process, causing the ink to polymerize and harden almost instantly. The curing process is highly efficient, as it transforms liquid ink into a solid state within seconds, allowing for rapid printing and handling of the printed materials.
Temperature’s Role in UV Printing
Temperature plays a pivotal role in the performance and outcome of UV flatbed printing. Here’s how variations in temperature can affect the process:
Ink Viscosity: The viscosity of UV inks is temperature-dependent. At higher temperatures, inks tend to become more fluid, which can improve ink flow and coverage. However, excessively high temperatures may cause the ink to spread uncontrollably, leading to bleeding or poor image resolution. Conversely, low temperatures can thicken the ink, potentially causing clogging in the print heads and uneven ink deposition.
Curing Efficiency: The curing process relies on a specific range of temperatures to be effective. If the ambient temperature is too low, the UV light may not activate the photoinitiators efficiently, resulting in incomplete curing. This can lead to tackiness in the printed area, making it susceptible to smudging or adhesion issues. On the other hand, excessively high temperatures can accelerate the curing process but may also cause premature curing in the print heads, leading to clogs and reduced print quality.
Substrate Expansion and Contraction: Different materials react differently to temperature changes. Substrates like metals and plastics can expand or contract with fluctuations in temperature. If the substrate’s dimensions change significantly during or after printing, it can cause the print to crack, peel, or distort.
Equipment Performance: The mechanical and electronic components of UV flatbed printers are also affected by temperature. Extreme heat can cause overheating of motors, electronics, and other sensitive parts, leading to potential breakdowns or reduced lifespan of the equipment. Conversely, cold environments can cause components to stiffen, affecting precision and reliability.
Humidity’s Influence on UV Printing
Humidity is another critical factor that can significantly impact UV flatbed printing. Here’s how:
Ink Absorption: High humidity can affect how ink is absorbed by the substrate. Moisture in the air can cause the substrate’s surface to become slightly damp, altering its porosity. This can result in ink bleeding, poor adhesion, or uneven color distribution. In contrast, low humidity can cause the substrate to be too dry, potentially leading to static build-up, which can attract dust and debris, affecting print quality.
Curing Issues: Humidity can interfere with the UV curing process. High humidity levels can create a thin layer of moisture on the printed surface, which can absorb some of the UV light intended for the ink. This can lead to incomplete curing, resulting in a tacky or sticky surface that is prone to smudging and scratching.
Substrate Stability: Changes in humidity can cause substrates to warp or swell. For example, wooden or paper-based substrates can absorb moisture and expand, while materials like metal may develop condensation, leading to surface imperfections. These changes can compromise the dimensional stability of the prints and affect their overall appearance and durability.
Printer Maintenance: High humidity environments can promote the growth of mold and mildew within the printer, particularly in areas where ink residue or debris may accumulate. This can lead to health hazards and require more frequent cleaning and maintenance. Low humidity, on the other hand, can cause static electricity issues, attracting dust and potentially causing print head clogs.
Mitigating the Effects of Temperature and Humidity
To ensure high-quality UV flatbed printing, it’s essential to control and mitigate the effects of temperature and humidity. Here are some strategies:
Climate-Controlled Environment: Maintaining a consistent temperature and humidity level within the printing facility is crucial. Investing in a climate control system, such as HVAC (heating, ventilation, and air conditioning), can help regulate these environmental factors, creating an optimal printing environment.
Humidity and Temperature Sensors: Installing sensors throughout the printing area can provide real-time data on humidity and temperature levels. This allows for prompt adjustments to maintain ideal conditions, preventing potential issues before they arise.
Substrate Preparation: Ensuring that substrates are stored in a controlled environment before and after printing can help maintain their stability. Acclimating substrates to the printing room’s conditions can reduce the risk of warping or swelling during the printing process.
Ink Management: Regularly checking and adjusting ink viscosity can help maintain consistent print quality. Using ink conditioning systems that heat or cool the ink to the optimal temperature can further improve ink flow and curing efficiency.
Equipment Maintenance: Regular maintenance of the UV flatbed printer, including cleaning and inspecting print heads, UV lamps, and other components, can help prevent issues related to temperature and humidity. Ensuring that the printer is in good working condition can enhance its performance and longevity.
UV flatbed printing offers numerous advantages in terms of versatility, speed, and quality. However, achieving optimal results requires a deep understanding of how environmental factors, particularly temperature and humidity, can impact the printing process. By controlling these variables through climate-controlled environments, real-time monitoring, proper substrate preparation, ink management, and regular equipment maintenance, printers can mitigate the effects of temperature and humidity, ensuring consistent and high-quality prints. As the printing industry continues to evolve, addressing these environmental factors will remain crucial in maximizing the potential of UV flatbed printing technology.