How Does UV Curing Work in a UV Flatbed Printer?
How Does UV Curing Work in a UV Flatbed Printer?
In the realm of digital printing, technological advancements have revolutionized the way we produce high-quality, customized graphics and designs across various substrates. Among these innovations, UV flatbed printers stand out for their versatility, precision, and most notably, their ability to instantly cure ink through UV curing technology. This technology not only accelerates the printing process but also enhances the durability, color vibrancy, and overall quality of the printed pieces. Let’s delve into the intricacies of how UV curing works within a UV flatbed printer, exploring its mechanisms, benefits, and the science behind this remarkable process.
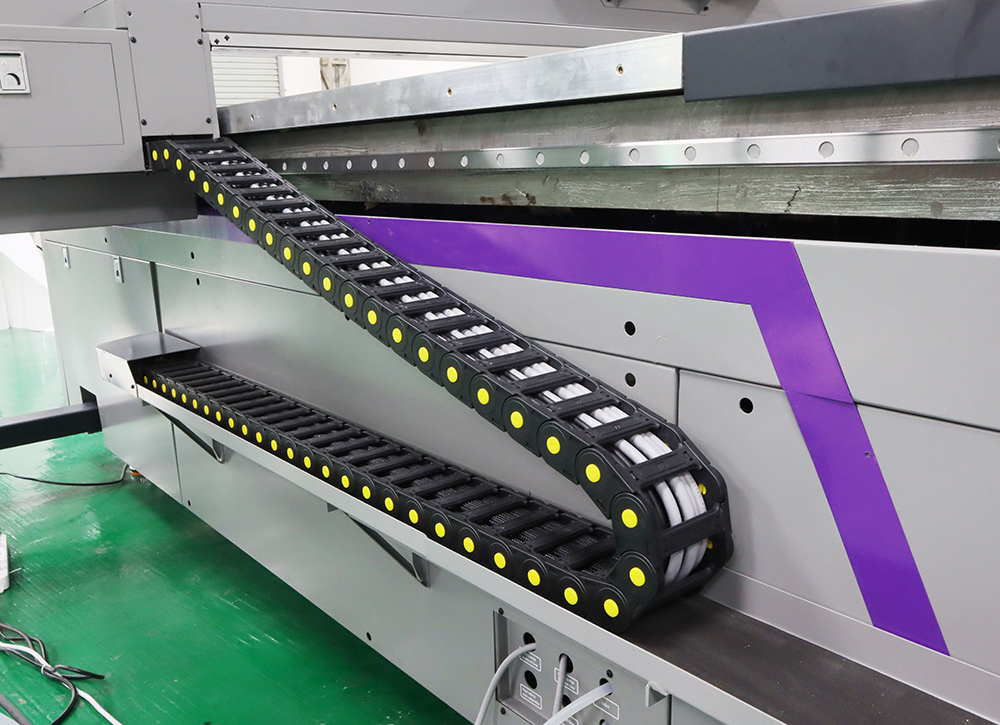
Introduction to UV Flatbed Printers
UV flatbed printers are a type of digital printing equipment designed to print directly onto a wide range of materials, including rigid substrates like wood, metal, glass, acrylics, and even flexible materials up to a certain thickness when equipped with a vacuum table. They employ advanced inkjet technology, dispensing droplets of ink in precise patterns to create stunning images and graphics. However, what sets UV flatbed printers apart is their integration of UV curing technology, which allows for immediate ink drying and curing, significantly reducing production time and enhancing the final product’s properties.
Understanding UV Curing
UV curing, also known as ultraviolet curing, is a photochemical process that utilizes ultraviolet (UV) light to initiate a rapid chemical reaction within the ink, causing it to harden or cure almost instantly. This process differs significantly from traditional drying methods, such as air drying or heat curing, which can be time-consuming and may not provide the same level of durability or color saturation.
The Science Behind UV Curing
UV inks contain photoinitiators, which are special chemical compounds that absorb UV light energy and convert it into chemical energy. When exposed to UV light, these photoinitiators undergo a reaction, generating free radicals that initiate a chain reaction throughout the ink film. This reaction leads to the formation of cross-linkages between the ink molecules, effectively solidifying the ink layer and bonding it to the substrate.
The key factors influencing the efficiency of UV curing include:
Intensity of UV Light: The intensity of the UV light source directly affects the rate of curing. Higher intensities lead to faster curing times.
Wavelength: Different wavelengths of UV light are absorbed by different photoinitiators, so the choice of UV lamp (e.g., mercury vapor, LED) and its spectral output is crucial.
Ink Chemistry: The composition of the ink, including the type and concentration of photoinitiators, influences the curing speed and final properties of the printed surface.
Substrate Type: The nature of the substrate (its surface energy, reflectivity, and thermal conductivity) can also affect the curing process.
UV Curing System in UV Flatbed Printers
UV flatbed printers incorporate a dedicated UV curing system, typically consisting of one or more UV lamps positioned directly after the print head. These lamps emit high-intensity UV light, often in the range of 365nm to 420nm, which is most effective for activating the photoinitiators in the ink.
Types of UV Lamps
Mercury Vapor Lamps: Traditionally used in UV curing applications, mercury vapor lamps produce a broad spectrum of UV light, including UV-A and UV-C wavelengths. However, they require warm-up time, generate heat, and contain mercury, posing environmental concerns.
LED UV Lamps: Increasingly popular due to their energy efficiency, instant-on capability, longer lifespan, and reduced heat output. LED UV lamps can be tailored to emit specific wavelengths, optimizing the curing process for specific ink formulations.
Curing Process
Ink Deposition: As the print head moves across the substrate, it deposits droplets of UV-curable ink in precise patterns, forming the desired image or design.
UV Exposure: Immediately after ink deposition, the UV lamp(s) illuminate the freshly printed area, exposing the ink to intense UV light.
Curing Reaction: The UV light activates the photoinitiators in the ink, triggering the rapid chemical reaction that solidifies the ink and bonds it to the substrate.
Cooling (Optional): Depending on the lamp type and substrate, a cooling system may be employed to manage heat generated during the curing process, ensuring optimal curing conditions and protecting the substrate from thermal stress.
Post-Processing (if necessary): After curing, the printed piece may undergo additional processing steps, such as cutting, trimming, or lamination, depending on the end application.
Benefits of UV Curing in UV Flatbed Printers
Instant Drying and Curing: UV curing eliminates the need for lengthy drying times, allowing for immediate handling and further processing of the printed material.
Enhanced Durability: The cross-linking process during UV curing creates a more durable ink layer, resistant to scratching, fading, and chemical degradation.
Vibrant Colors and Sharp Details: UV inks cure to a glossy finish, enhancing color vibrancy and providing sharp, crisp details.
Versatility in Substrate Choice: UV curing enables printing on a wide range of materials, including those that are difficult to print on using traditional methods.
Environmental Friendliness (LED UV): While mercury vapor lamps have environmental drawbacks, the adoption of LED UV technology reduces energy consumption, eliminates mercury usage, and generates less heat.
Reduced Waste: The ability to print directly onto a variety of substrates eliminates the need for intermediate materials like transfer papers or adhesives, reducing waste and production costs.
Challenges and Considerations
Despite its numerous advantages, UV curing in UV flatbed printers also presents some challenges and considerations:
Cost: UV flatbed printers and their UV curing systems can be more expensive than traditional printers, due to the specialized technology involved.
Heat Management: Excessive heat generated during UV curing can cause substrate warping or damage, particularly with heat-sensitive materials. Proper ventilation and cooling systems are essential.
Ink Selection: Not all inks are UV-curable, and the choice of ink can significantly impact the final print quality and curing efficiency.
Health and Safety: UV light and certain photoinitiators can pose health risks if not handled properly. Adequate protective gear and ventilation are crucial.
Conclusion
UV curing in UV flatbed printers represents a significant leap forward in digital printing technology, offering unparalleled speed, durability, and versatility. By harnessing the power of UV light to instantly cure ink, these printers enable the production of high-quality, customized graphics and designs across a broad spectrum of substrates. As the industry continues to evolve, with advancements in LED UV technology and the development of new ink formulations, the potential of UV curing in UV flatbed printers becomes even more exciting. Understanding the mechanisms and benefits of this remarkable process is crucial for anyone seeking to harness its power for their printing needs.