How Does UV Flatbed Printing Compare to Traditional Printing Methods?
In the ever-evolving world of printing technology, businesses are constantly seeking innovative solutions to meet their diverse and dynamic printing needs. Among the myriad of options available, UV flatbed printing has emerged as a formidable contender, challenging traditional printing methods in terms of versatility, efficiency, and quality. This article delves into the intricacies of UV flatbed printing and compares it with conventional printing techniques, highlighting the unique advantages and potential drawbacks of each.
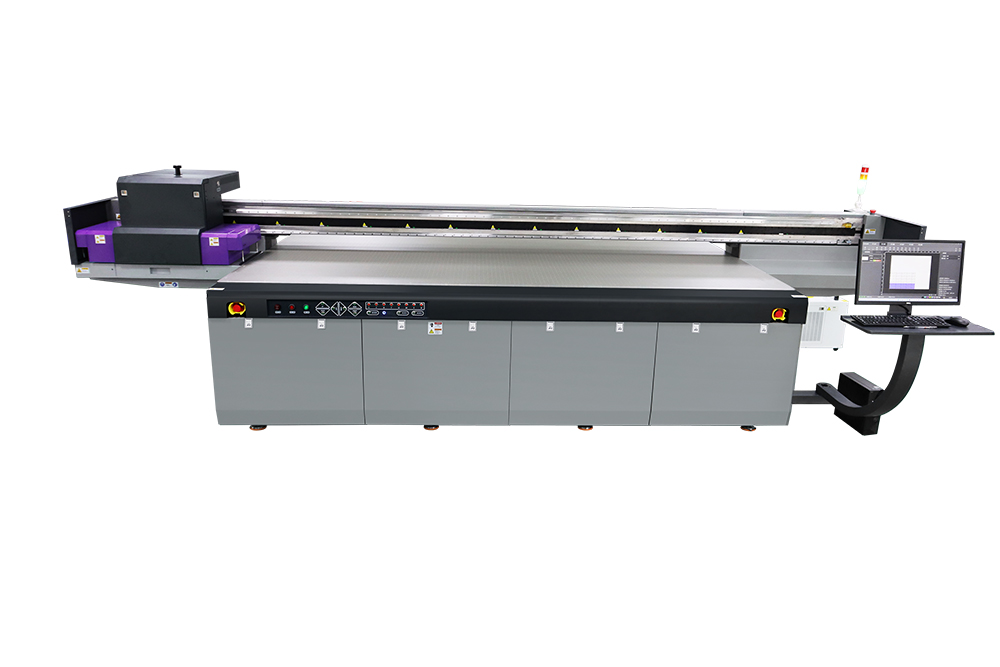
Understanding UV Flatbed Printing
UV flatbed printing is a digital printing process that utilizes ultraviolet light to cure or dry the inks immediately after they are applied to the substrate. This technology allows for printing on a wide range of materials, including rigid surfaces such as wood, metal, glass, plastics, and even textiles, making it highly versatile. The process involves a flatbed printer that uses a series of UV-curable inks, which are jetted onto the surface through precision nozzles. Once the ink is deposited, a UV light source instantly cures it, resulting in a durable, vibrant, and smudge-proof print.
Key Features of UV Flatbed Printing
Versatility in Substrates: Unlike traditional methods that are often limited to specific materials, UV flatbed printing can accommodate an extensive array of substrates, from solid objects to flexible media.
High Resolution: With advancements in print head technology, UV flatbed printers can achieve extremely high resolutions, often exceeding 1200 dpi, resulting in sharp and detailed prints.
Immediate Curing: The UV curing process ensures that the inks dry instantly, reducing the risk of smudging and allowing for immediate handling and further processing of the printed items.
Durability: UV-cured inks are highly resistant to fading, scratching, and environmental factors such as moisture and chemicals, ensuring long-lasting prints.
Customization: This method enables high levels of customization, with the ability to print variable data, intricate designs, and even textures directly onto the substrate.
Traditional Printing Methods: An Overview
Traditional printing methods encompass a variety of techniques that have been in use for centuries, each with its own set of strengths and limitations. The most common traditional printing methods include offset lithography, screen printing, and flexography.
Offset Lithography
Offset printing involves transferring an image from a metal plate to a rubber blanket, which then prints the image onto the substrate. It is renowned for its high image quality and is widely used for large-scale commercial printing, such as newspapers, magazines, and packaging.
Pros:
Excellent print quality and consistency.
Cost-effective for large-volume prints.
Wide range of paper and substrate options.
Cons:
Longer setup times and higher initial costs for small runs.
Limited to flat or cylindrical surfaces.
Not ideal for quick turnarounds due to plate preparation.
Screen Printing
Screen printing, also known as silkscreening, involves pushing ink through a fine mesh screen onto the substrate. It is particularly suited for printing on fabrics, plastics, and other materials that may not be compatible with other printing methods.
Pros:
Ability to print on a variety of textures and thicknesses.
Vibrant colors and good opacity.
Suitable for both small and large-scale production.
Cons:
Limited to one color at a time, requiring multiple passes for multi-color prints.
Higher setup costs for each color.
Not as precise as digital methods for intricate designs.
Flexography
Flexography, commonly used in packaging and label printing, employs flexible relief plates to transfer ink to the substrate. It is known for its ability to print on a wide range of materials, including plastics, paper, and foil.
Pros:
High-speed printing capability.
Good for printing on uneven surfaces.
Cost-effective for large volumes.
Cons:
Lower resolution compared to offset and digital methods.
Limited to flexible substrates.
Initial setup and plate costs can be high.
Comparing UV Flatbed Printing to Traditional Methods
Versatility and Substrate Compatibility
UV flatbed printing stands out for its unparalleled versatility in substrate compatibility. Traditional methods, while adept at printing on specific materials, often require significant adjustments or entirely different processes to accommodate different substrates. UV flatbed printers, on the other hand, can seamlessly transition between materials, from rigid surfaces like metal and glass to flexible media like textiles and vinyl, without compromising on print quality.
Print Quality and Detail
In terms of print quality and detail, UV flatbed printing and offset lithography are neck and neck, with both capable of producing high-resolution prints. However, UV flatbed printing’s ability to print directly onto textured surfaces and achieve intricate details, such as fine gradients and small text, gives it an edge in certain applications. Screen printing and flexography, while effective, generally do not match the precision and detail offered by UV flatbed or offset printing.
Speed and Efficiency
The speed and efficiency of printing methods largely depend on the specific application and volume. Offset lithography is highly efficient for large-scale runs, with quick turnaround times once the plates are set up. However, for short runs and personalized prints, UV flatbed printing offers a significant advantage due to its minimal setup time and ability to print variable data on demand. Flexography and screen printing, while fast in their respective niches, cannot match the versatility and quick setup of UV flatbed printing for diverse jobs.
Cost Considerations
Cost is a crucial factor in any printing decision. Traditional methods often have higher initial setup costs but can become more cost-effective as the print volume increases. UV flatbed printing, while initially more expensive due to the technology involved, can be more economical for small to medium-sized runs due to reduced setup times and waste. Additionally, the durability and longevity of UV-cured prints can offset the higher initial costs over time, particularly in applications where long-term durability is essential.
Environmental Impact
Environmental concerns are increasingly important in today’s market. UV flatbed printing uses solvent-free inks that cure instantly, reducing the need for harmful chemicals and minimizing waste. Offset lithography, while it has made strides in reducing its environmental footprint, still relies on inks that require longer drying times and can involve more waste due to plate changes. Screen printing and flexography also generate waste and may use chemicals that require special disposal methods.
The choice between UV flatbed printing and traditional printing methods ultimately depends on the specific needs of the project, including the type of substrate, desired print quality, volume, budget, and environmental considerations. UV flatbed printing offers unparalleled versatility, high resolution, and quick turnarounds, making it an excellent choice for a wide range of applications, particularly those requiring short runs, customization, or printing on unconventional substrates.
Traditional methods, such as offset lithography, screen printing, and flexography, continue to have their place, particularly in high-volume production and specialized applications. Each method has its unique strengths and limitations, and the key is to select the one that best aligns with the project requirements.
In summary, UV flatbed printing represents a significant advancement in printing technology, offering a blend of versatility, efficiency, and quality that challenges traditional methods. As technology continues to evolve, it is likely that UV flatbed printing will become even more integrated into the printing industry, pushing the boundaries of what is possible and driving innovation in print.