How Does UV Ink Differ from Traditional Printing Inks?
How Does UV Ink Differ from Traditional Printing Inks?
In the realm of printing technology, the ink used plays a pivotal role in determining the quality, durability, and versatility of the printed output. Traditional printing inks, which have been the cornerstone of the industry for centuries, have continually evolved to meet the demands of various applications. However, in recent decades, a new contender has emerged: UV ink. This innovative type of ink, cured by ultraviolet light, offers a host of advantages that set it apart from its traditional counterparts. In this article, we will delve into the key differences between UV ink and traditional printing inks, exploring their composition, curing processes, environmental impact, application versatility, and overall performance.
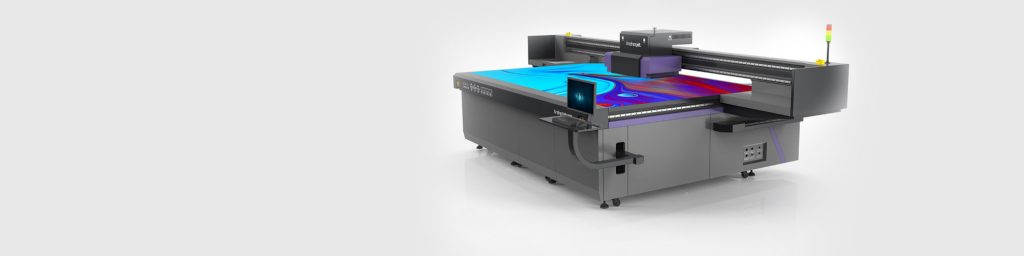
Composition and Chemistry
Traditional Printing Inks
Traditional printing inks, also known as conventional inks, encompass a broad category that includes oil-based, water-based, and solvent-based inks. Oil-based inks, commonly used in offset printing, consist of pigments or dyes suspended in a carrier oil, often mixed with resins and additives to enhance print quality and durability. Water-based inks, on the other hand, utilize water as the primary solvent, making them more environmentally friendly. Solvent-based inks, typically used in large-format printing, contain solvents that evaporate during the printing process, leaving the pigment or dye on the substrate.
These inks are formulated to provide good color saturation, adhesion, and resistance to fading and smudging. However, their composition often includes volatile organic compounds (VOCs) that can pose health and environmental risks if not properly managed.
UV Ink
UV ink, or ultraviolet-curable ink, is a type of ink that solidifies or “cures” when exposed to ultraviolet light. It typically contains a mixture of acrylate monomers, oligomers, photoinitiators, and pigments or dyes. The photoinitiators are crucial components as they absorb UV light and trigger a chemical reaction that causes the ink to polymerize, forming a durable, cross-linked film on the substrate.
One of the significant advantages of UV ink is its low VOC content. Since it does not rely on evaporation of solvents for drying, it releases fewer harmful emissions during the printing process, making it a more environmentally friendly option.
Curing Processes
Traditional Printing Inks
The curing process for traditional inks varies depending on the type of ink and the printing method. Oil-based inks, for example, often require a combination of heat and time to fully cure. This can involve passing the printed material through a drying oven or allowing it to air-dry for an extended period. Water-based and solvent-based inks generally dry faster, with solvent-based inks evaporating their solvents more rapidly due to their volatile nature.
These curing methods can be time-consuming and energy-intensive, particularly for large-scale printing operations. Additionally, the need for heat can sometimes limit the types of substrates that can be used, as some materials may warp or degrade under high temperatures.
UV Ink
UV ink, by contrast, cures instantly upon exposure to UV light. This process, known as photopolymerization, allows for rapid curing and eliminates the need for heat or extended drying times. UV curing systems typically consist of UV lamps or LEDs that emit light at specific wavelengths to trigger the curing reaction.
The speed of UV curing offers several advantages. It enables faster print speeds, reducing overall production time. It also allows for immediate handling and further processing of the printed material, as there is no need to wait for the ink to dry. Furthermore, UV curing can be more energy-efficient than traditional drying methods, particularly when considering the reduced need for heating systems.
Environmental Impact
Traditional Printing Inks
Traditional inks, particularly oil-based and solvent-based varieties, can have a significant environmental impact. They often contain high levels of VOCs, which can contribute to air pollution and pose health risks to printers and end-users. Disposal of ink waste and used solvents also requires careful handling to prevent contamination of soil and water sources.
Water-based inks, while generally more environmentally friendly, still require proper waste management to mitigate the impact of any residual chemicals or dyes.
UV Ink
UV ink is considered more environmentally friendly than traditional inks due to its low VOC content and the absence of solvents that need to evaporate. The UV curing process produces minimal emissions and does not generate harmful byproducts. Additionally, UV ink can be formulated to be more easily recyclable or biodegradable, further reducing its environmental footprint.
Moreover, the efficiency of UV curing systems can lead to energy savings compared to traditional drying methods. This not only reduces greenhouse gas emissions but also lowers operating costs for printing businesses.
Application Versatility
Traditional Printing Inks
Traditional inks have long been the standard for a wide range of printing applications, from book publishing and packaging to advertising and signage. Their versatility lies in their ability to adhere to various substrates, including paper, cardboard, plastic, and metal, depending on the ink type and formulation.
However, traditional inks may have limitations when it comes to certain specialized applications. For example, they may not be suitable for printing on heat-sensitive materials or for achieving the high-definition, vibrant colors desired in digital printing.
UV Ink
UV ink excels in applications that require fast curing, high durability, and precise color reproduction. Its ability to cure instantly on a wide range of substrates, including heat-sensitive materials like plastics and vinyl, makes it ideal for digital printing, large-format printing, and product labeling.
UV ink is particularly well-suited for outdoor applications due to its resistance to fading, weathering, and abrasion. It can be used to print on materials that will be exposed to direct sunlight, moisture, and extreme temperatures, such as vehicle wraps, banners, and signage.
Furthermore, UV ink’s versatility extends to specialized printing techniques, such as 3D printing and screen printing, where the precise control and rapid curing of UV ink can enhance the quality and efficiency of the process.
Performance and Durability
Traditional Printing Inks
Traditional inks have proven their durability and performance over time, particularly in applications where longevity and resistance to wear and tear are essential. Oil-based inks, for example, are known for their strong adhesion and resistance to fading, making them suitable for long-term applications like book printing.
However, traditional inks may not offer the same level of scratch resistance or chemical resistance as UV inks. They may also be more susceptible to smudging or fading when exposed to harsh environmental conditions.
UV Ink
UV ink is renowned for its exceptional durability and performance. The cross-linked polymer film formed during the curing process creates a strong, resilient layer that is highly resistant to scratching, fading, and chemical attack. This makes UV ink ideal for applications where the printed material will be subjected to heavy use or harsh environments.
Additionally, UV ink’s ability to cure on a variety of substrates ensures that the printed image remains vibrant and intact, even on materials that may expand or contract with changes in temperature or humidity.
Conclusion
In summary, UV ink and traditional printing inks differ significantly in their composition, curing processes, environmental impact, application versatility, and overall performance. Traditional inks, with their long history and proven durability, remain a staple of the printing industry. However, UV ink’s rapid curing, low VOC content, and exceptional durability make it a compelling alternative for many applications.
As technology continues to evolve, the demand for faster, more efficient, and more environmentally friendly printing solutions will grow. UV ink, with its combination of speed, versatility, and durability, is poised to play a increasingly important role in meeting these demands. Whether for digital printing, large-format printing, or specialized applications, UV ink offers a compelling set of advantages that set it apart from traditional printing inks. As the industry continues to innovate, it is likely that UV ink will become an even more integral part of the printing landscape, pushing the boundaries of what is possible in terms of quality, efficiency, and sustainability.