How to Achieve Consistent Color Output on a UV Flatbed Printer
How to Achieve Consistent Color Output on a UV Flatbed Printer
In the world of printing, achieving consistent color output is crucial for maintaining brand identity and professional appearance. UV flatbed printers, known for their versatility and ability to print on various materials, are widely used in the advertising, packaging, and signage industries. However, ensuring consistent color reproduction on these printers can be challenging. This article explores practical steps to achieve consistent color output on a UV flatbed printer.
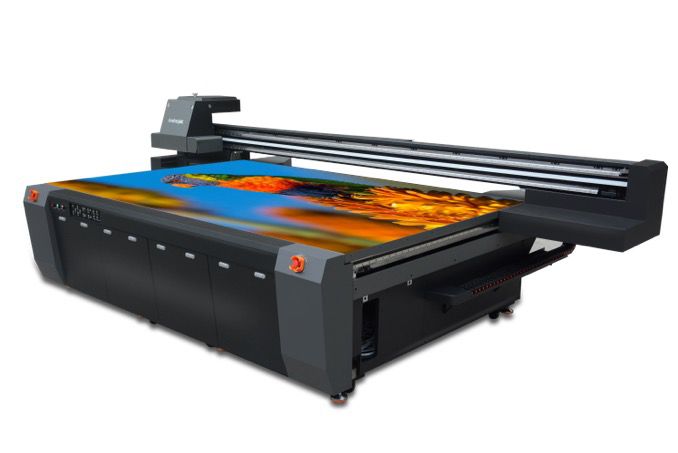
1. Calibrate Your Printer Regularly
Color calibration is the first and foremost step towards achieving color consistency. Printer calibration involves adjusting the printer’s settings to ensure that the colors it produces match a known standard. Many UV flatbed printers come with built-in calibration tools or software. Regularly using these tools can significantly improve color consistency.
During calibration, it’s essential to use a color target or test print with known color values. By comparing the printed output to the original, you can adjust the printer’s color profiles accordingly. This process helps to compensate for any drift in ink density, nozzle wear, or other factors that can affect color reproduction.
2. Use High-Quality Inks and Materials
The quality of inks and printing materials plays a vital role in color consistency. UV-curable inks specifically designed for flatbed printers tend to produce more vibrant and consistent colors. Similarly, using substrates that are compatible with UV inks and have a consistent, smooth surface can enhance color reproduction.
Low-quality inks or substrates might cause colors to appear duller or shift over time, affecting the overall consistency. Therefore, investing in high-quality supplies is crucial for maintaining color fidelity.
3. Control the Printing Environment
Environmental factors such as temperature, humidity, and dust can all affect the printing process and, consequently, color reproduction. UV flatbed printers should be placed in a controlled environment with minimal fluctuations in temperature and humidity. Regular cleaning and maintenance of the printer also help to reduce dust buildup, which can interfere with the printing process.
4. Profile Your Printer and Materials
Creating an ICC profile for your printer and the specific materials you’re using is another essential step. ICC profiles contain information about how colors should be reproduced on a particular device or material. By profiling your printer and materials, you’re telling the printer how to accurately reproduce colors based on the characteristics of the inks and substrates being used.
Profiling typically involves printing a color target containing hundreds or thousands of color patches. A spectrophotometer then measures these patches, and software creates a profile based on these measurements. Once the profile is created, it can be selected in your printing software to ensure consistent color output.
5. Monitor and Adjust Ink Density
Ink density, or the amount of ink laid down on the substrate, directly affects color saturation and consistency. If the ink density is too low, colors may appear washed out. If it’s too high, colors may appear too dark or intense.
Regularly checking and adjusting ink density settings on your UV flatbed printer can help maintain color consistency. Many printers allow you to adjust ink density settings for each individual color, providing fine-grained control over the final output.
6. Standardize Your Workflow
Consistency in your printing workflow is key to achieving consistent color output. This means using the same settings, profiles, and materials for each print job. By standardizing your workflow, you can minimize variations in color reproduction caused by human error or inconsistencies in the printing process.
7. Regular Maintenance and Cleaning
Proper maintenance and cleaning of your UV flatbed printer are essential for maintaining color consistency. Clogged nozzles, dirty print heads, or contaminated inks can all lead to color shifts or other printing issues. Regularly cleaning the print heads and nozzles, as well as replacing inks and filters as needed, can help to prevent these problems.
8. Train Your Operators
Finally, proper training of your printer operators is crucial. They need to understand the importance of color consistency, how to calibrate the printer, select the correct ICC profiles, and maintain a standardized workflow. By investing in their training, you can ensure that human factors don’t contribute to color inconsistencies.
Achieving consistent color output on a UV flatbed printer requires attention to detail and a systematic approach. By regularly calibrating your printer, using high-quality inks and materials, controlling the printing environment, profiling your printer and materials, monitoring ink density, standardizing your workflow, maintaining your printer, and training your operators, you can significantly improve color consistency and produce professional-looking prints that meet your customers’ expectations.