How to Achieve Consistent Print Quality on a UV Flatbed Printer?
How to Achieve Consistent Print Quality on a UV Flatbed Printer?
UV flatbed printers have revolutionized the printing industry, offering unmatched versatility, efficiency, and print quality. However, achieving consistent print quality on a UV flatbed printer can be challenging, especially when dealing with various materials, inks, and print settings. This article explores the key factors that contribute to achieving consistent print quality on a UV flatbed printer, from material selection and pre-press preparations to printer calibration and maintenance.
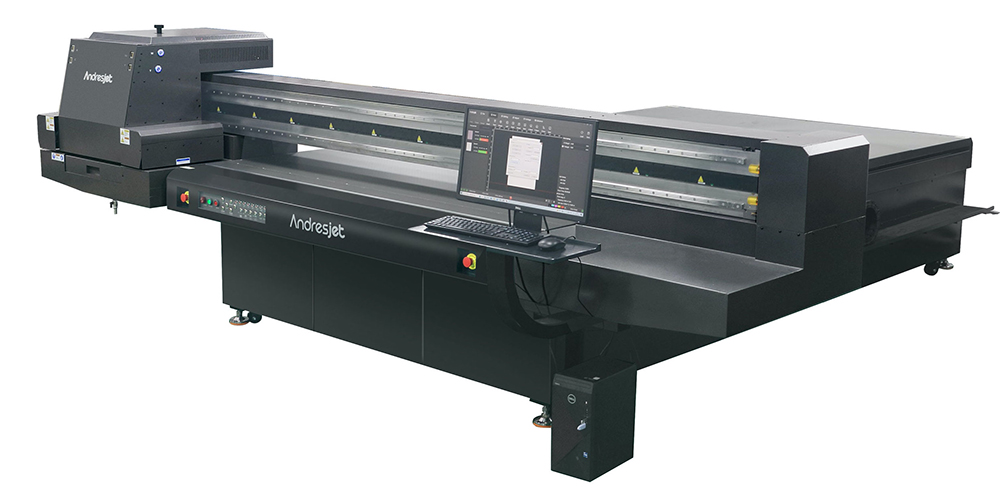
1. Material Selection
The choice of printing material significantly impacts the final print quality. UV flatbed printers can accommodate a wide range of materials, including glass, metal, plastic, wood, and even textile. However, not all materials are compatible with all types of UV inks. Therefore, it’s crucial to select materials that are compatible with the inks used in your UV flatbed printer.
Additionally, the surface texture and porosity of the material can affect print quality. Rough or porous surfaces may require special treatments or primers to ensure smooth and even ink laydown. It’s also important to consider the material’s ability to withstand UV exposure, as some materials may degrade or discolor over time when exposed to UV light.
2. Pre-press Preparations
Before starting the printing process, several pre-press preparations are essential to ensure consistent print quality. Firstly, the design files must be optimized for printing. This involves converting them to the appropriate file format (such as PDF or TIFF), adjusting the resolution to match the printer’s capabilities, and ensuring color accuracy by using the correct color profiles.
Moreover, color management is crucial for maintaining consistency across different print jobs. Implementing a color management system (CMS) helps standardize colors, reducing variations caused by differences in monitor calibration, ink, and material.
3. Printer Calibration
Regular printer calibration is vital to maintain consistent print quality. Calibration involves adjusting the printer’s settings to ensure accurate color reproduction and ink laydown. This typically includes adjusting the printer’s heads, ink flow, and other parameters to achieve the desired output.
Calibration should be performed periodically, especially when changing inks, materials, or printheads. Many UV flatbed printers come with built-in calibration tools or software that simplify this process.
4. Ink Management
The quality and type of UV ink used in the printer significantly affect the final output. UV inks are specially formulated to dry instantly under UV light, providing durable and long-lasting prints. However, different inks may have varying drying times, adhesion properties, and color saturation.
Therefore, it’s essential to use high-quality inks from reputable suppliers and to regularly clean and maintain the ink system to prevent clogged nozzles or ink buildup. Additionally, storing inks properly is crucial to maintain their quality and extend their shelf life.
5. Printer Maintenance
Regular printer maintenance is essential to ensure optimal performance and consistent print quality. This includes cleaning the printheads, replacing worn parts, and checking the printer’s alignment and calibration.
Clogged nozzles can lead to banding, missing lines, or other artifacts in the final print. Therefore, it’s important to perform regular nozzle checks and cleanings to ensure ink flow is unobstructed.
Furthermore, maintaining the printer’s environment is also crucial. UV flatbed printers should be kept in a dust-free, temperature-controlled environment to minimize external factors that could affect print quality.
6. Operator Training
The operator’s skill level and knowledge of the printer also contribute to achieving consistent print quality. Proper training on the printer’s software, ink management, material handling, and troubleshooting techniques are essential.
Operators should be familiar with the printer’s settings and adjustments, inkjet technology, and color management principles. Regular training sessions and workshops can help operators stay up to date with the latest printing techniques and best practices.
7. Quality Control Measures
Implementing quality control measures is key to maintaining consistent print quality. This involves regularly checking print samples for color accuracy, resolution, and other quality parameters.
Automated inspection systems can help identify defects, such as banding, missing nozzles, or color shifts, allowing operators to address these issues promptly. Additionally, maintaining detailed records of each print job, including ink usage, material type, and print settings, can help identify patterns and improve future print jobs.
Conclusion
Achieving consistent print quality on a UV flatbed printer requires attention to detail, regular maintenance, and a systematic approach to quality control. By selecting compatible materials, preparing design files, calibrating the printer, managing inks, maintaining the printer, training operators, and implementing quality control measures, printers can ensure that their UV flatbed printers produce high-quality, consistent prints.
Remember, consistency is key in the printing industry, and by following these guidelines, UV flatbed printer users can achieve reliable and repeatable results, satisfying even the most demanding clients.