How to Achieve Consistent Print Results with a UV Flatbed Printer
How to Achieve Consistent Print Results with a UV Flatbed Printer
Achieving consistent print results with a UV flatbed printer is a goal that many print professionals strive for. Whether you’re printing graphics for signage, packaging, or artistic purposes, consistency ensures that your outputs meet the high standards expected by clients and end-users. However, achieving this level of uniformity is not always straightforward. It requires a blend of technical know-how, meticulous preparation, and ongoing maintenance. In this article, we will delve into the key aspects that contribute to consistent print results with a UV flatbed printer, exploring everything from printer setup and material preparation to color management and post-processing techniques.
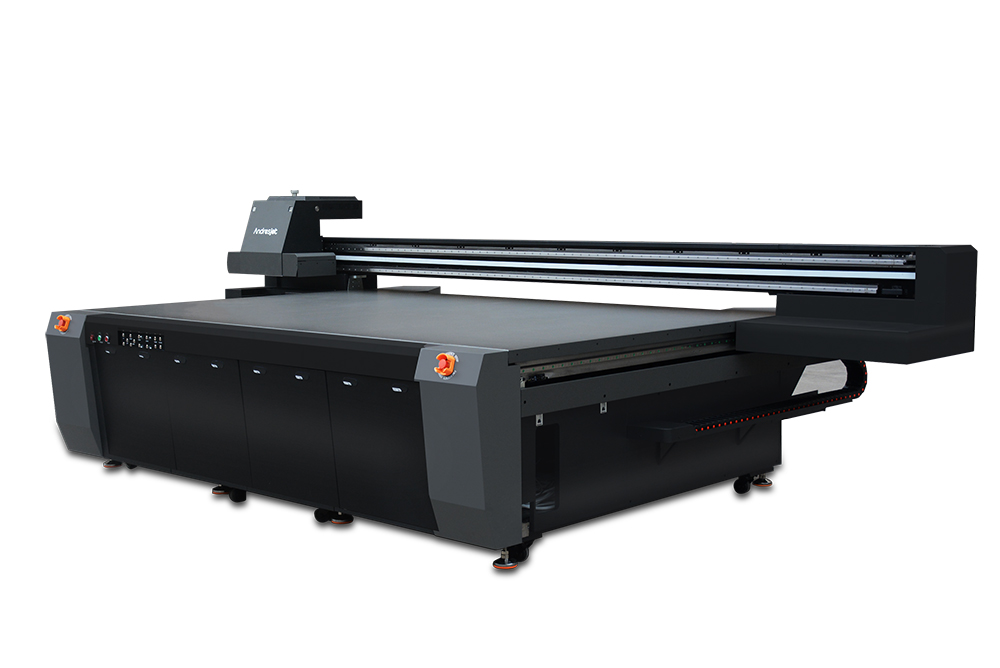
1. Understanding Your UV Flatbed Printer
Before diving into the specifics, it’s crucial to have a solid understanding of your UV flatbed printer’s capabilities and limitations. UV flatbed printers utilize ultraviolet light to cure inks instantly upon contact with the printing surface. This technology allows for printing on a wide range of materials, including rigid substrates like acrylic, glass, metal, and various types of plastics.
Key Components:
Print Heads: These are responsible for depositing ink onto the substrate. Understanding their configuration (such as the number of heads and nozzles) and how they impact print resolution and speed is essential.
Ink System: UV inks come in various formulations, each suited to specific applications. Knowledge of your ink’s properties, such as viscosity, cure time, and adhesion to different materials, is vital.
UV Lamps: The quality and intensity of the UV light directly affect ink curing. Ensuring the lamps are regularly maintained and replaced as needed is crucial for consistent results.
Software: The printer’s software, including RIP (Raster Image Processor) and color management tools, plays a significant role in translating digital files into print-ready data.
2. Printer Setup and Calibration
Proper setup and calibration are foundational to achieving consistent print results.
Environmental Controls:
Temperature and Humidity: Maintaining a stable environment with consistent temperature and humidity levels is critical. Fluctuations can affect ink viscosity, causing variations in print quality.
Ventilation: Adequate ventilation ensures that fumes from the UV inks are properly managed, which is not only important for print quality but also for the health and safety of operators.
Calibration Procedures:
Print Head Alignment: Regularly align the print heads to ensure that they are positioned correctly, avoiding issues like banding and misregistration.
Color Calibration: Use calibration tools and software to ensure that the colors produced by the printer match the intended colors in your digital files. This involves profiling the printer and creating ICC (International Color Consortium) profiles for different substrates and ink configurations.
Media Settings: Each substrate requires specific settings for optimal print quality. Adjust parameters such as ink drop size, print speed, and cure time according to the manufacturer’s recommendations and your own testing.
3. Material Preparation
The choice and preparation of the printing substrate can significantly impact print consistency.
Material Selection:
Compatibility: Ensure that the materials you choose are compatible with UV inks and your printer’s specifications. Some materials may require special treatments or coatings to ensure proper ink adhesion and curing.
Flatness and Rigidity: For flatbed printers, the substrate must be flat and rigid to avoid issues like head crashes and ink bleeding.
Pre-Treatment:
Cleaning: Thoroughly clean the substrate to remove any dust, oils, or contaminants that could interfere with ink adhesion.
Priming: In some cases, applying a primer can improve ink adhesion and color saturation, particularly on non-absorbent materials like glass or metal.
4. Color Management
Consistent color reproduction is a hallmark of high-quality printing.
Profiling:
Create Custom Profiles: Develop ICC profiles for your specific printer, inks, and substrates. These profiles help the printer accurately interpret color data from your digital files.
Regular Updates: Periodically recheck and update your profiles, especially if you’ve made changes to your printer setup or are using new materials.
Color Accuracy Tools:
Spectrophotometers: Use these devices to measure the color output of your prints and compare it to the desired color standards.
Soft Proofing: Utilize soft proofing tools to preview how your prints will look before sending them to the printer, allowing for adjustments to be made before committing to a print run.
5. Print Settings and Techniques
Optimizing your print settings can greatly enhance consistency.
Resolution and Passes:
Print Resolution: Higher resolutions generally yield sharper images but may come at the cost of slower print speeds. Find the balance that suits your specific needs.
Multiple Passes: Printing in multiple passes can help distribute ink more evenly, reducing the risk of banding and improving overall print quality.
Ink Laydown:
Ink Density: Adjust the ink density settings to ensure that the right amount of ink is deposited on the substrate, avoiding issues like over-saturation or ink starvation.
Curing Stages: If possible, utilize intermediate curing stages for multi-layer prints to ensure that each layer is fully cured before the next is applied.
6. Post-Processing
The final step in achieving consistent print results is careful post-processing.
Curing:
Final Cure: Ensure that prints are fully cured after printing to maximize durability and color fastness. This may involve additional time under UV lights or the use of specialized curing equipment.
Consistency Checks: Regularly check the cure quality of your prints using tools like a cure meter to ensure that the inks are fully polymerized.
Finishing:
Cutting and Trimming: Use precision tools to cut and trim your prints, maintaining clean edges and ensuring that the final dimensions match your specifications.
Lamination and Protection: If required, apply a protective laminate or coating to enhance the durability and scratch resistance of your prints.
7. Maintenance and Upkeep
Consistent print results also hinge on regular maintenance and upkeep of your printer.
Daily Maintenance:
Clean Print Heads: Regularly clean the print heads to prevent clogging and ensure optimal ink flow.
Inspect UV Lamps: Check the UV lamps for any signs of wear or reduction in intensity, and replace them as needed.
Wipe Down: Keep the printer’s interior and exterior clean to avoid dust and debris interfering with the printing process.
Long-Term Maintenance:
Scheduled Servicing: Follow the manufacturer’s recommended maintenance schedule for preventive servicing and part replacements.
Software Updates: Keep your printer’s software and firmware up to date to benefit from the latest improvements and bug fixes.
Conclusion
Achieving consistent print results with a UV flatbed printer is a multifaceted endeavor that requires attention to detail at every stage of the printing process. From understanding your printer’s capabilities and properly setting it up, to carefully selecting and preparing materials, managing color accurately, optimizing print settings, and meticulously post-processing your prints, each step is crucial. Regular maintenance and upkeep ensure that your printer continues to perform at its best, delivering high-quality prints consistently over time.
By following these guidelines and continuously refining your processes based on feedback and testing, you can elevate the quality and consistency of your UV flatbed printing, meeting and even exceeding the expectations of your clients and customers.