How to Achieve Superior Durability with UV-Cured Prints
In the realm of printing technology, the pursuit of superior durability is a constant endeavor. Among various methods, UV-cured printing stands out as a highly effective technique that not only enhances the aesthetic appeal of prints but also significantly boosts their longevity. This article delves into the intricacies of UV-cured printing, exploring the mechanisms behind its durability and offering practical insights on how to achieve optimal results. By understanding the process, selecting the right materials, and implementing best practices, one can ensure that UV-cured prints withstand the test of time.
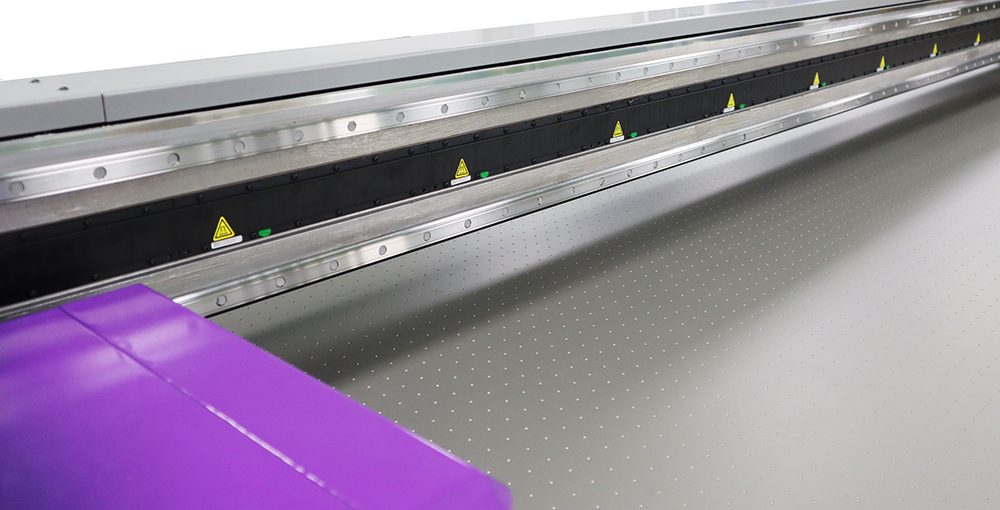
Understanding UV-Cured Printing
UV-cured printing, also known as UV printing, involves the use of ultraviolet light to instantly dry and cure inks. This technology leverages the power of UV radiation to initiate a chemical reaction within the ink, causing it to harden and adhere firmly to the substrate. Unlike traditional printing methods that rely on evaporation or heat to dry inks, UV-cured printing offers a faster, more efficient, and environmentally friendly alternative.
The UV-curing process typically involves three essential components: UV-curable inks, a UV light source, and a substrate. The inks, formulated with special resins and additives, are applied to the substrate using various printing techniques such as inkjet, screen printing, or offset lithography. Once the ink is deposited, it is exposed to UV light, usually in the range of 200-400 nanometers, which triggers the curing process. This rapid curing not only accelerates production but also ensures a high-quality finish with excellent adhesion and durability.
Mechanisms of Durability in UV-Cured Prints
The durability of UV-cured prints stems from several key mechanisms:
Chemical Cross-Linking: UV light causes the resin molecules in the ink to form cross-links, creating a dense, three-dimensional network. This cross-linked structure significantly enhances the ink’s resistance to abrasion, chemicals, and environmental factors such as moisture and temperature fluctuations.
Instant Curing: The immediate curing of the ink prevents it from smearing or running, ensuring a sharp and precise image. This quick solidification also reduces the risk of contamination or damage during handling and post-processing.
Enhanced Adhesion: UV-cured inks often contain adhesion promoters that ensure a strong bond between the ink and the substrate. This strong interface minimizes the likelihood of peeling or cracking over time.
Weather Resistance: The cross-linked polymer structure provides excellent resistance to UV degradation, preventing fading and discoloration even when exposed to prolonged sunlight.
Selecting the Right Materials
Achieving superior durability with UV-cured prints begins with the selection of appropriate materials. Here are some critical considerations:
Substrates: Choose substrates that are compatible with UV-curable inks and capable of withstanding the curing process. Common substrates include plastics, metals, glass, and certain types of paper and fabrics. Ensure that the substrate is clean, dry, and free of any contaminants that could interfere with ink adhesion.
Inks: Opt for high-quality UV-curable inks specifically designed for your application. Consider factors such as cure speed, viscosity, colorfastness, and chemical resistance. Some inks may be formulated for specific substrates or to meet particular performance requirements, such as flexibility or outdoor durability.
UV Light Sources: The type and intensity of the UV light source can significantly impact the curing efficiency and print quality. LED-based UV systems are increasingly popular due to their energy efficiency, long lifespan, and ability to provide consistent curing across a wide range of applications.
Best Practices for UV-Cured Printing
To maximize the durability of UV-cured prints, follow these best practices:
Proper Ink Application: Ensure that the ink is evenly applied to the substrate, avoiding over-saturation or thinning. Use the recommended printing parameters, such as inkjet printer settings or screen printing mesh counts, to achieve the desired ink thickness and coverage.
Curing Optimization: Calibrate the UV light source to the appropriate wavelength, intensity, and exposure time for the specific ink and substrate being used. Over-exposure can lead to over-curing, which may cause the ink to become brittle, while under-exposure can result in incomplete curing and reduced durability.
Environmental Control: Maintain a clean and controlled environment during the printing and curing processes. Dust, humidity, and temperature variations can all affect the quality and durability of the prints. Use dust extraction systems and climate control measures to minimize these factors.
Post-Processing: After curing, handle the prints with care to avoid scratching or damaging the surface. If additional processing, such as cutting or laminating, is required, ensure that it is done using tools and materials that are compatible with UV-cured inks.
Quality Assurance: Regularly inspect the prints for any defects, such as bubbling, cracking, or adhesion issues. Implement a quality control process to monitor the printing and curing conditions, ensuring consistency and reliability.
Innovations in UV-Cured Printing
The field of UV-cured printing is continuously evolving, with innovations aimed at further enhancing durability and expanding application possibilities. Some notable advancements include:
Nano-Enhanced Inks: Incorporating nanoparticles into UV-curable inks can improve their mechanical properties, such as hardness and flexibility, leading to even more durable prints.
3D UV Printing: This technology enables the creation of three-dimensional objects with UV-cured inks, offering new possibilities for durable and intricate designs.
Dual-Cure Systems: Combining UV curing with other curing methods, such as heat or electron beam curing, can result in hybrid inks with superior performance characteristics.
Sustainable Inks: The development of eco-friendly UV-curable inks, made from renewable resources and with lower volatile organic compound (VOC) emissions, aligns with the growing trend towards sustainability in manufacturing.
Achieving superior durability with UV-cured prints requires a comprehensive understanding of the process, careful selection of materials, and adherence to best practices. By harnessing the power of UV curing, businesses and individuals can produce prints that not only look stunning but also stand the test of time. Whether for outdoor signage, product packaging, or artistic creations, UV-cured printing offers a versatile and resilient solution that meets the demands of modern applications. As the technology continues to advance, the potential for even greater durability and innovation in UV-cured printing is limitless.