How to Adjust Print Speed and Quality on a UV Flatbed Printer
How to Adjust Print Speed and Quality on a UV Flatbed Printer
UV flatbed printers have revolutionized the printing industry by offering versatile, high-quality, and durable prints on a wide range of substrates. These printers utilize ultraviolet (UV) light to cure the ink instantly, resulting in vibrant, smudge-proof, and water-resistant prints. Whether you’re printing on rigid materials like glass, metal, or wood, or on flexible media like vinyl or fabric, adjusting the print speed and quality is crucial to achieving optimal results. This article delves into the intricacies of fine-tuning these settings to ensure you get the best output from your UV flatbed printer.
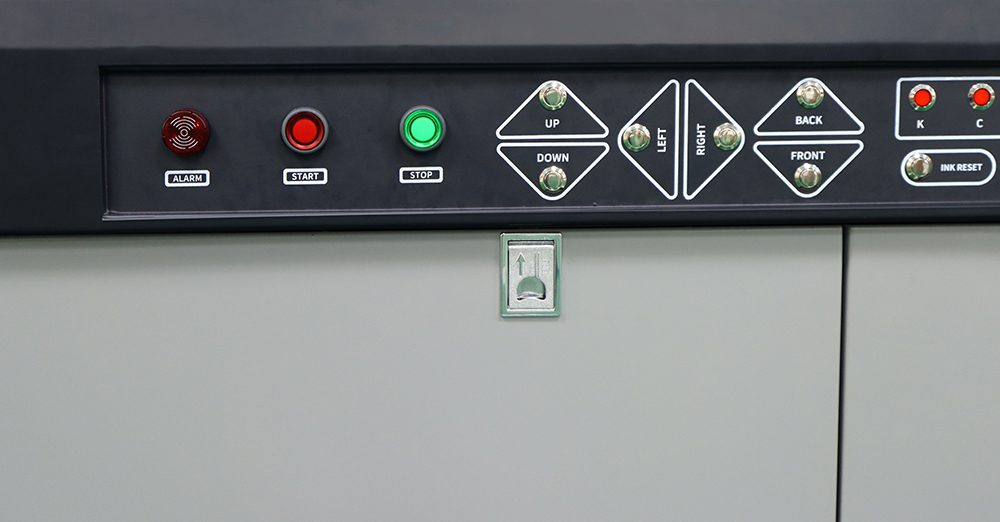
Understanding the Basics
Before diving into the specifics, it’s essential to grasp the fundamental concepts of print speed and quality.
Print Speed: This refers to the rate at which the printer produces output, usually measured in square meters per hour (m²/h) or prints per minute (ppm). Faster print speeds are desirable for high-volume production, but they can sometimes compromise print quality.
Print Quality: This encompasses several factors, including resolution (dpi – dots per inch), color accuracy, ink coverage, and detail reproduction. Higher print quality is crucial for applications where visual fidelity is paramount, such as fine art prints or promotional materials.
Factors Affecting Print Speed and Quality
Several variables impact the print speed and quality of a UV flatbed printer. Understanding these factors will help you make informed adjustments:
Ink Type and Viscosity: Different inks have varying curing times and flow characteristics. High-viscosity inks may require slower print speeds to ensure proper curing and avoid clogging.
Substrate Material: The type and condition of the substrate can affect ink adhesion and curing. For example, porous materials like uncoated paper absorb ink differently than non-porous surfaces like glass.
Print Resolution: Higher resolutions require more data processing and finer ink droplet placement, which can slow down the print speed.
Curing Lamp Intensity: The power and wavelength of the UV lamps determine the curing speed. Insufficient curing can lead to ink smudging, while over-curing may cause substrate damage or color fading.
Printer Mechanics: The physical capabilities of the printer, such as the speed of the print head movement and the accuracy of the positioning system, also play a role.
Adjusting Print Speed
Adjusting the print speed involves a balance between productivity and quality. Here’s how to fine-tune this setting:
Test Prints: Start by performing test prints at different speeds. Use a standard test image that includes a variety of colors, text sizes, and intricate details. This will help you identify any quality issues that arise at various speeds.
Gradual Adjustments: Increase or decrease the print speed incrementally. A drastic change can lead to unexpected problems, such as ink bleeding or incomplete curing.
Observe Curing: Pay close attention to the curing process. If the ink isn’t curing properly, you may need to slow down the print speed or increase the UV lamp intensity.
Substrate Compatibility: Consider the substrate’s characteristics. For example, if you’re printing on a heat-sensitive material, faster speeds might be preferable to minimize heat exposure.
Maintenance: Regularly maintain your printer to ensure it operates at peak efficiency. A well-maintained printer can often handle higher speeds without compromising quality.
Adjusting Print Quality
Achieving the desired print quality requires careful calibration and adjustment of several parameters:
Resolution Settings:
DPI Selection: For most applications, a resolution of 300 dpi is considered high quality. However, for fine art or detailed graphics, you might opt for 600 dpi or higher.
Halftoning: This technique simulates continuous tones using dots of varying sizes and spacing. Adjusting the halftoning settings can improve color gradients and overall image smoothness.
Color Management:
Profiling: Use ICC (International Color Consortium) profiles to ensure color accuracy. These profiles map the printer’s color output to the desired color space.
Calibration: Regularly calibrate your printer and monitor to maintain consistent color reproduction.
Ink Coverage:
Dot Gain: Adjust the dot gain settings to control the amount of ink deposited on the substrate. Excessive dot gain can lead to oversaturated colors and blurring.
Ink Layers: In some cases, applying multiple thin layers of ink (known as layering) can improve color saturation and detail without compromising print speed.
Print Head Alignment:
Automated Tools: Use the printer’s built-in alignment tools to ensure the print heads are correctly positioned. Misalignment can result in banding, streaking, or blurred prints.
Manual Adjustment: For more precise control, some printers allow manual adjustment of the print heads.
Curing Settings:
Lamp Power: Adjust the power of the UV lamps to ensure proper curing. Too little power can result in undercured ink, while too much can cause overcuring.
Curing Time: Depending on the ink type and substrate, you may need to adjust the time the ink spends under the UV lamps.
Best Practices for Optimization
To further enhance your print speed and quality, consider the following best practices:
Keep a Log: Maintain a detailed log of your print settings, including speed, resolution, ink type, and substrate. This will help you replicate successful prints and troubleshoot issues.
Stay Updated: Regularly update your printer’s firmware and software to take advantage of new features and improvements.
Train Your Staff: Ensure that operators are well-versed in the printer’s functionality and troubleshooting procedures. Proper training can prevent many common issues.
Environment Control: Maintain a consistent temperature and humidity in your print environment. Fluctuations in these conditions can affect ink viscosity, curing times, and overall print quality.
Experiment: Don’t be afraid to experiment with different settings and materials. Sometimes, the best results come from unexpected combinations.
Adjusting the print speed and quality on a UV flatbed printer is a delicate process that requires a thorough understanding of the printer’s capabilities and the materials being used. By carefully balancing these settings and regularly performing maintenance and calibration, you can achieve outstanding prints that meet your specific needs. Whether you’re producing high-volume commercial graphics or intricate fine art pieces, the ability to fine-tune your printer’s performance is key to achieving professional-grade results. With practice and attention to detail, you can maximize both the efficiency and the quality of your UV flatbed printing operations.