How to Adjust Printer Settings for Maximum Color Vibrancy on a UV Flatbed Printer?
How to Adjust Printer Settings for Maximum Color Vibrancy on a UV Flatbed Printer?
UV flatbed printers have revolutionized the printing industry, especially when it comes to achieving vibrant and durable prints on various materials. These printers use UV-curable inks that are instantly dried by UV light, resulting in sharp, fade-resistant images. However, to harness the full potential of your UV flatbed printer and ensure maximum color vibrancy, you need to master the art of adjusting printer settings. In this comprehensive guide, we will walk you through the key steps and considerations for optimizing your printer settings to achieve outstanding color results.
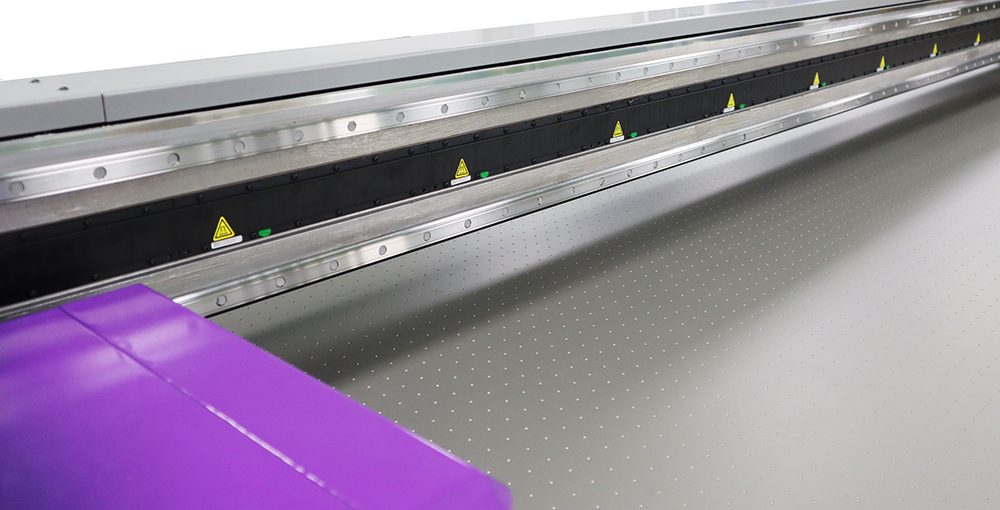
1. Understand Your Printer’s Capabilities
Before diving into the specifics of adjusting settings, it’s crucial to understand the capabilities of your UV flatbed printer. Different models and brands may have unique features and limitations. Consult your printer’s manual or manufacturer’s website to gain insights into its color gamut, resolution capabilities, and recommended ink types. This knowledge will serve as a foundation for making informed adjustments.
2. Calibrate Your Printer
Proper calibration is the cornerstone of achieving accurate and vibrant colors. Most UV flatbed printers offer built-in calibration tools or software. Use these tools to align the print heads, adjust ink densities, and ensure consistent color output. If your printer doesn’t have automated calibration, you may need to perform manual calibrations using test prints and visual inspections.
3. Choose the Right Color Mode
UV flatbed printers often provide various color modes, such as CMYK, RGB, or specific modes designed for printing on different materials. For maximum color vibrancy, select the color mode that best suits your print job and material. For instance, using an RGB mode might be ideal for graphics-heavy prints, while CMYK is more suited for prints requiring a broader color range.
4. Optimize Ink Density and Saturation
Ink density and saturation play pivotal roles in achieving vibrant colors. Start by adjusting the ink density settings. Increasing ink density can enhance color saturation, but it should be done cautiously to avoid ink bleeding or smudging. Experiment with different density levels to find the optimal balance between color vibrancy and print quality.
Saturation adjustments allow you to fine-tune the intensity of individual colors. Boosting saturation can make colors pop, but overdoing it can lead to unrealistic or oversaturated hues. Find the saturation level that maintains a natural look while maximizing vibrancy.
5. Utilize Color Management Tools
Most UV flatbed printers come equipped with color management tools that let you adjust color profiles and manage color accuracy. These tools allow you to select or create custom ICC profiles tailored to your specific ink set and material. Using the right color profile ensures that your prints match your design intent and exhibit maximum color vibrancy.
6. Adjust Print Resolution
Print resolution directly impacts the sharpness and detail of your prints. While higher resolution generally results in better print quality, it also increases print time and ink consumption. Find the right balance by adjusting the print resolution based on your specific needs. For instance, 300 DPI (dots per inch) is suitable for most print jobs, but you might opt for a higher resolution for intricate designs or when printing on materials that require finer detail.
7. Experiment with Print Speed
Print speed can indirectly affect color vibrancy. Faster print speeds may reduce ink curing time, leading to less vibrant colors. Slowing down the print speed can allow for better ink curing and more vibrant hues. However, finding the optimal print speed is a balancing act, as slower speeds increase production time. Conduct test prints at different speeds to determine the best setting for your specific requirements.
8. Control Ink Curing Temperature
UV flatbed printers cure ink using UV light, and the temperature during this process can impact color vibrancy. Lower curing temperatures may result in dull colors, while excessively high temperatures can cause ink to crack or yellow. Consult your printer’s specifications to find the recommended curing temperature range and adjust accordingly.
9. Choose the Right Printing Material
The choice of printing material significantly influences color vibrancy. Different materials absorb ink differently, affecting the final appearance of colors. Experiment with various materials to determine which ones best showcase your desired color vibrancy. Additionally, consider using materials with a smooth surface for more consistent ink application and enhanced color vibrancy.
10. Perform Regular Maintenance
Lastly, regular maintenance is crucial for maintaining optimal print quality and color vibrancy. Clean your printer’s print heads and UV lamps regularly to prevent ink buildup and ensure consistent curing. Replace worn-out parts promptly and keep your printer’s software updated to access the latest color management features and bug fixes.
Conclusion
Achieving maximum color vibrancy on a UV flatbed printer is a multifaceted process that requires a keen understanding of your printer’s capabilities, meticulous calibration, and strategic adjustments to various settings. By following the steps outlined in this guide, you can unlock the full potential of your UV flatbed printer and produce prints that are not only visually stunning but also durable and long-lasting. Remember, achieving optimal color vibrancy is often a result of experimentation and fine-tuning, so don’t be afraid to make adjustments and conduct test prints along the way. With patience and practice, you’ll master the art of maximizing color vibrancy on your UV flatbed printer.