How to Adjust Printer Settings for Optimal Color Saturation on a UV Flatbed Printer?
How to Adjust Printer Settings for Optimal Color Saturation on a UV Flatbed Printer?
UV flatbed printers have revolutionized the printing industry, offering unparalleled versatility and precision in reproducing vibrant colors on various materials. These printers use UV-curable inks that instantly dry when exposed to ultraviolet light, allowing for quick turnaround times and minimal smearing or bleeding. However, achieving optimal color saturation on a UV flatbed printer requires careful adjustment of printer settings, understanding of ink properties, and material compatibility. This article outlines the steps to adjust printer settings for optimal color saturation on a UV flatbed printer.
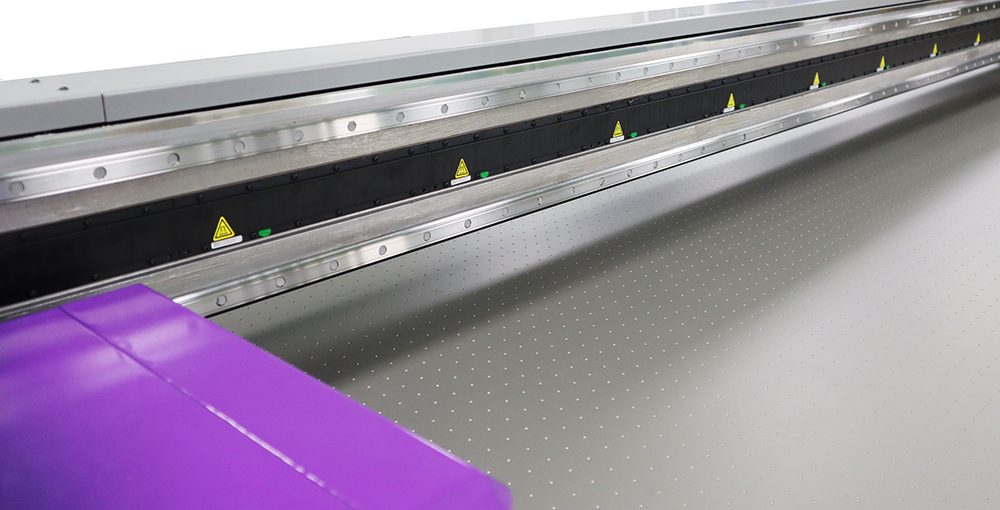
1. Understand the Basics of UV Flatbed Printing
Before diving into the specifics of adjusting printer settings, it is crucial to understand the basics of UV flatbed printing. UV flatbed printers use UV-curable inks that are cured (dried) instantly by UV light. This technology allows for printing on a wide range of materials, including plastics, glass, metal, wood, and more. The inks are formulated to adhere to these surfaces without the need for primers or additional coatings, making the process efficient and cost-effective.
Color saturation refers to the intensity or purity of a color. In printing, it is achieved by adjusting the amount of ink deposited on the substrate. UV flatbed printers offer precise control over ink deposition, allowing for fine adjustments to achieve the desired color saturation.
2. Choose the Right Ink
The choice of ink plays a significant role in achieving optimal color saturation. UV-curable inks are available in various formulations, each with its unique characteristics. Some inks are designed for specific materials, while others offer enhanced color gamut or durability.
When selecting an ink, consider the following:
Color Gamut: Look for inks that offer a wide color gamut to ensure you can achieve the desired colors and saturation levels.
Opacity: Opaque inks are ideal for achieving high color saturation on transparent or dark materials.
Durability: Consider the intended use of the printed material. If it will be exposed to harsh conditions, choose an ink with high durability.
Compatibility: Ensure the ink is compatible with your printer and the materials you intend to print on.
3. Calibrate Your Printer
Printer calibration is essential for achieving consistent and accurate color reproduction. It involves adjusting the printer settings to match the specific characteristics of the inks and materials being used.
Follow these steps to calibrate your UV flatbed printer:
Print a Test Chart: Print a color test chart provided by the ink manufacturer or create a custom chart with a range of colors and shades.
Measure Color Values: Use a spectrophotometer or colorimeter to measure the color values of the printed test chart.
Adjust Printer Settings: Compare the measured color values to the target values and adjust the printer settings accordingly. This may involve adjusting the ink density, color balance, or other parameters.
Repeat the Process: Reprint the test chart and measure the color values again. Repeat the adjustment process until you achieve the desired color accuracy and saturation.
4. Adjust Printer Settings for Color Saturation
Once your printer is calibrated, you can fine-tune the settings to achieve optimal color saturation. Here are some key settings to adjust:
Ink Density: Increase the ink density setting to deposit more ink on the substrate, resulting in higher color saturation. Be cautious not to exceed the maximum recommended ink density, as it may lead to ink bleeding or smearing.
Color Balance: Adjust the color balance settings to achieve the desired hue and saturation. This may involve increasing or decreasing the intensity of specific colors.
Print Mode: Some UV flatbed printers offer different print modes, such as high-speed or high-quality mode. Choose the print mode that prioritizes color saturation while meeting your production requirements.
Curing Settings: Adjust the UV light intensity and curing time to ensure the inks are fully cured without compromising color saturation. Insufficient curing may result in ink bleeding or fading, while excessive curing may cause the inks to become brittle or crack.
5. Consider Material Compatibility
The choice of substrate material can significantly impact color saturation. Different materials have varying ink absorption rates and surface textures, which can affect how inks adhere and appear.
When selecting a material, consider the following:
Ink Absorption: Materials with high ink absorption rates may require additional ink deposition to achieve optimal color saturation.
Surface Texture: Rough or porous surfaces may require additional ink to achieve a smooth and even color appearance.
Pretreatment: Some materials may require pretreatment, such as sanding or priming, to ensure proper ink adhesion and color saturation.
6. Perform Regular Maintenance
Regular maintenance of your UV flatbed printer is crucial for maintaining optimal color saturation and overall print quality. This includes cleaning the print head, replacing worn parts, and ensuring the printer is properly calibrated.
Follow these maintenance tips:
Clean the Print Head: Regularly clean the print head to remove any ink residue or debris that may affect ink deposition and color saturation.
Replace Worn Parts: Replace worn or damaged parts, such as the UV lamp or print head, to maintain consistent curing and ink deposition.
Calibrate Regularly: Perform regular printer calibration to ensure consistent color reproduction and saturation over time.
Conclusion
Achieving optimal color saturation on a UV flatbed printer requires careful adjustment of printer settings, understanding of ink properties, and material compatibility. By following the steps outlined in this article, you can fine-tune your printer settings to achieve vibrant and consistent colors on various materials. Remember to choose the right ink, calibrate your printer, adjust printer settings for color saturation, consider material compatibility, and perform regular maintenance to ensure optimal print quality. With these tips, you can unlock the full potential of your UV flatbed printer and produce eye-catching prints with exceptional color saturation.