How to Adjust Printer Settings for Optimal UV Printing?
How to Adjust Printer Settings for Optimal UV Printing?
UV printing, also known as ultraviolet printing, is a popular technique that uses UV-curable inks and specialized printers to produce high-quality prints with vibrant colors and excellent durability. This printing method is particularly suited for materials that are difficult to print on using traditional inkjet or offset printing techniques, such as plastics, metals, glass, and certain types of paper. To achieve optimal results in UV printing, it is crucial to adjust the printer settings correctly. This article will guide you through the process of adjusting printer settings for optimal UV printing.
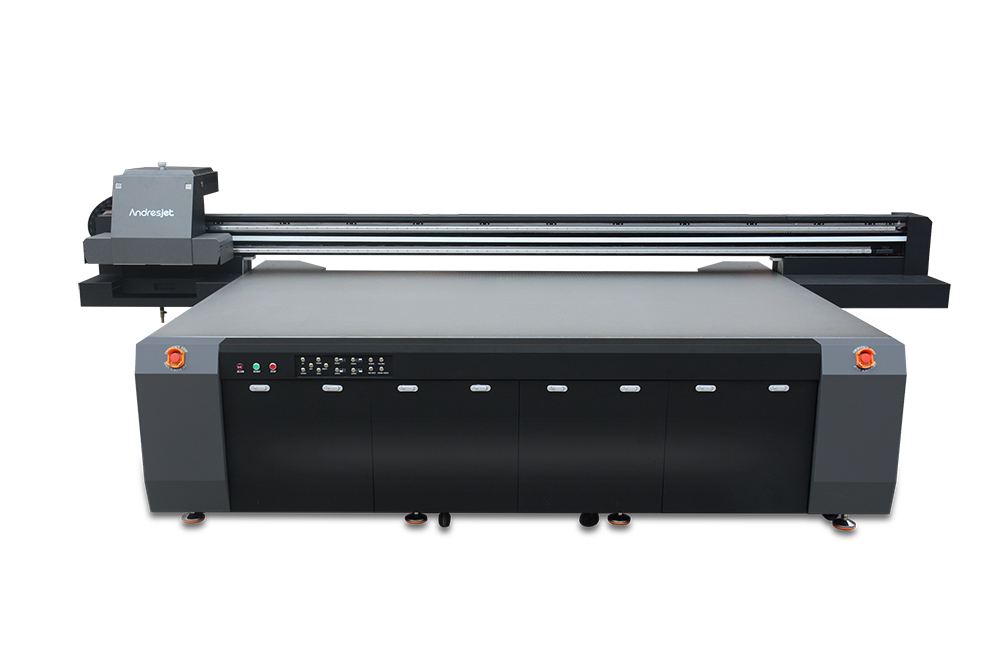
Understanding UV Printers and UV-Curable Inks
UV printers are designed to work with UV-curable inks, which are formulated to cure (or dry) instantly when exposed to ultraviolet light. These inks are typically more viscous than conventional inks, allowing them to adhere to a wider range of substrates without smearing or bleeding. UV printers are equipped with UV lamps or LED arrays that emit the necessary ultraviolet light to cure the ink as it is deposited onto the material.
1. Printer Calibration
Before making any adjustments to the printer settings, it is essential to ensure that the printer is properly calibrated. Calibration involves aligning the print heads, checking the ink flow, and adjusting the printer’s internal settings to ensure consistent and accurate printing.
Print Head Alignment: Use the printer’s built-in alignment tool to ensure that the print heads are correctly positioned. This step is crucial for achieving sharp, well-defined prints.
Ink Flow Check: Inspect the ink lines and make sure there are no blockages or leaks. Also, check the ink levels and replace any empty or low ink cartridges.
Internal Settings Calibration: Most UV printers have internal calibration settings that can be accessed through the printer’s control panel or software. Follow the manufacturer’s instructions to perform the calibration process.
2. Adjusting Ink Density and Curing Levels
Ink density and curing levels play a significant role in the quality of UV prints. These settings need to be adjusted based on the specific material being printed and the desired print outcome.
Ink Density: Ink density refers to the amount of ink deposited on the material. Higher ink density results in more saturated colors, while lower ink density produces lighter shades. Experiment with different ink density settings to find the optimal balance between color saturation and ink curing.
Curing Levels: Curing levels determine how much ultraviolet light is applied to the ink to cure it. Higher curing levels result in faster ink curing but may cause the ink to become too brittle, leading to cracking or peeling. Lower curing levels may result in slower curing times and increased risk of ink smearing. It is essential to find the right curing level for each material and ink combination.
3. Choosing the Right Printing Mode
UV printers often offer different printing modes, such as high-speed mode, high-quality mode, and custom mode. Each mode has its own set of advantages and disadvantages, and selecting the right mode can significantly impact the print quality.
High-Speed Mode: This mode is suitable for large-volume printing jobs where speed is a priority. However, it may result in slightly lower print quality.
High-Quality Mode: This mode is ideal for printing jobs that require exceptional detail and color accuracy. It may result in slower printing speeds but produces superior print quality.
Custom Mode: Custom mode allows you to adjust individual printer settings, such as ink density, curing levels, and print speed, to achieve the desired print outcome. This mode is recommended for experienced users who understand the intricacies of UV printing.
4. Adjusting Print Resolution
Print resolution refers to the number of dots per inch (DPI) that the printer can produce. Higher DPI results in sharper, more detailed prints, while lower DPI produces less detailed prints with larger dots.
Standard Resolution: Most UV printers offer a standard resolution of 300 DPI, which is suitable for most printing jobs.
High Resolution: For printing jobs that require exceptional detail, such as fine art prints or high-end product packaging, consider using a higher resolution, such as 600 DPI or even 1200 DPI.
Low Resolution: Low-resolution printing (150 DPI or lower) may be suitable for large-format prints or printing jobs where speed is a priority and detail is not crucial.
5. Considering Material Properties
Different materials have unique properties that can affect the print quality. It is essential to adjust the printer settings based on the specific material being printed.
Porous Materials: Materials like paper and certain types of fabric are porous and absorb ink easily. For these materials, you may need to adjust the ink density and curing levels to ensure proper ink adhesion and curing.
Non-Porous Materials: Non-porous materials, such as plastics, metals, and glass, do not absorb ink and require higher curing levels to ensure proper ink adhesion and curing.
Flexible Materials: Flexible materials, like vinyl or certain types of plastic, may require lower ink density and curing levels to prevent the ink from cracking or peeling when the material is bent or stretched.
6. Testing and Fine-Tuning
Once you have made the initial adjustments to the printer settings, it is crucial to perform test prints to evaluate the print quality and make any necessary fine-tuning adjustments.
Print Test Patterns: Print test patterns, such as color gradients or fine lines, to evaluate the print quality, ink curing, and color accuracy.
Inspect the Prints: Inspect the test prints closely for any signs of ink smearing, bleeding, cracking, or peeling. Also, check the color accuracy and overall print quality.
Make Adjustments: Based on the results of the test prints, make any necessary adjustments to the printer settings, such as ink density, curing levels, or print resolution. Repeat the testing process until you achieve the desired print quality.
Conclusion
Adjusting printer settings for optimal UV printing requires a thorough understanding of the printer’s capabilities, the properties of the materials being printed, and the desired print outcome. By following the steps outlined in this article, you can ensure that your UV prints are of the highest quality, with vibrant colors, excellent detail, and superior durability. Remember to always perform test prints and make any necessary adjustments to achieve the best possible results. With practice and experience, you will become proficient in adjusting printer settings for optimal UV printing.