How to Adjust the Settings on a UV Flatbed Printer for Best Results?
How to Adjust the Settings on a UV Flatbed Printer for Best Results?
UV flatbed printers have revolutionized the printing industry, offering high-quality prints on various materials with exceptional durability. These printers use UV-curable inks that dry instantly when exposed to ultraviolet light, resulting in vibrant, long-lasting prints. However, achieving the best results with a UV flatbed printer requires careful adjustment of its settings. This article will guide you through the process of optimizing your printer’s settings for superior print quality, efficiency, and material compatibility.
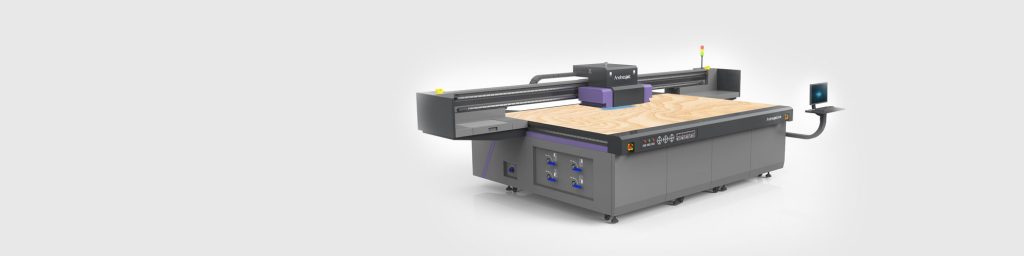
1. Understanding the Basics of UV Flatbed Printer Settings
Before diving into the specifics, it’s essential to understand the fundamental settings that can be adjusted on a UV flatbed printer. These settings typically include:
Print Resolution: Determines the sharpness and detail of the printed image. Higher resolutions produce clearer images but may require more time to print.
Ink Density: Controls the amount of ink deposited on the material. Higher ink density results in richer colors but can increase the risk of ink bleeding or smudging.
UV Intensity: Adjusts the power of the UV light source, affecting the curing speed of the ink. Incorrect UV intensity can lead to ink not fully curing or overheating the material.
Print Speed: Balances production time and print quality. Faster speeds may reduce detail and increase the risk of ink misalignment.
Print Mode: Offers预设的打印配置,如“高质量”、“标准”或“快速”,以适应不同的打印需求。
2. Calibrating Print Resolution for Optimal Output
Print resolution is a critical factor in determining the overall quality of your prints. Most UV flatbed printers offer resolutions ranging from 720×720 DPI (dots per inch) to 4000×4000 DPI or higher. The ideal resolution depends on the specific application and material:
For detailed graphics and fine art prints, aim for resolutions of 1440×1440 DPI or higher.
For large-format prints viewed from a distance, such as outdoor advertising, a resolution of 720×720 DPI may suffice.
Conduct test prints at different resolutions to determine the optimal setting for your specific needs.
3. Adjusting Ink Density for Rich Colors and Material Compatibility
Ink density directly impacts the vibrancy of colors and the printer’s ability to adhere to various materials. Start with the manufacturer’s recommended ink density settings as a baseline and adjust as needed:
For porous materials like wood or canvas, you may need to increase ink density to ensure proper coverage and color saturation.
On non-porous surfaces such as glass or metal, reduce ink density to prevent ink pooling and ensure even curing.
Perform test prints on your target material to fine-tune ink density settings for the best results.
4. Optimizing UV Intensity for Efficient Curing
UV intensity controls how quickly the ink cures under the UV light. Incorrect settings can lead to ink that is either too tacky or overheated, causing material damage:
Follow the printer manufacturer’s guidelines for initial UV intensity settings.
Increase UV intensity for thicker or more opaque materials to ensure complete curing.
Decrease UV intensity for sensitive materials or when printing thinner layers of ink to prevent overheating.
Regularly check the UV lamps for wear and replace them according to the manufacturer’s recommendations to maintain consistent curing performance.
5. Balancing Print Speed and Quality
Print speed is a crucial factor in determining production efficiency, but it must be balanced with print quality:
For high-volume production, consider using the “fast” print mode, but be prepared to sacrifice some detail.
When printing detailed graphics or prototypes, opt for the “high-quality” mode to ensure the best possible output.
Experiment with different print speeds and modes to find the optimal balance between quality and efficiency for your specific applications.
6. Material-Specific Adjustments
Different materials require unique adjustments to achieve the best print results. Consider the following material-specific tips:
Rigid Materials: Ensure the material is properly secured to the print bed to prevent movement during printing. Adjust the print head gap to maintain consistent ink deposition.
Flexible Materials: Use a vacuum table or adhesive to hold flexible materials in place. Adjust the print head pressure to prevent ink bleeding or distortion.
Heat-Sensitive Materials: Lower the UV intensity and print speed to minimize heat exposure and prevent material warping or discoloration.
7. Regular Maintenance and Calibration
Consistent print quality requires regular maintenance and calibration of your UV flatbed printer:
Clean the print head and ink system regularly to prevent ink buildup and clogged nozzles.
Calibrate the printer’s color profile to ensure accurate color reproduction.
Check and replace worn components, such as UV lamps and print bed adhesives, as needed.
Conclusion
Achieving the best results with a UV flatbed printer requires a thorough understanding of its settings and how they interact with different materials and print requirements. By carefully adjusting print resolution, ink density, UV intensity, print speed, and considering material-specific factors, you can optimize your printer’s performance for superior print quality, efficiency, and material compatibility. Regular maintenance and calibration will further ensure consistent results over time. With these guidelines, you’ll be well-equipped to harness the full potential of your UV flatbed printer and produce outstanding prints for a wide range of applications.