How to Choose the Right UV-Curable Ink for Your Application
In the realm of printing and coating technologies, UV-curable inks have emerged as a game-changer, offering numerous advantages over traditional solvent-based or water-based inks. Their quick curing process, excellent durability, and versatility make them ideal for a wide range of applications, from digital printing on packaging materials to creating intricate designs on various substrates. However, with the myriad of options available in the market, selecting the right UV-curable ink for your specific application can be a daunting task. This comprehensive guide aims to simplify the decision-making process by outlining key factors to consider when choosing UV-curable inks.
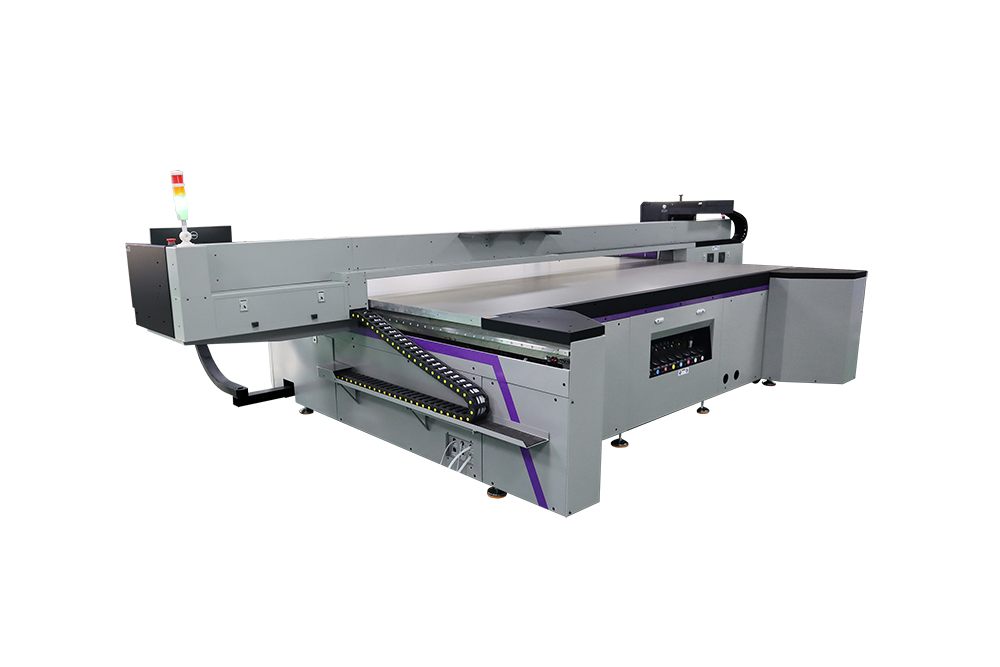
Understanding UV-Curable Inks
UV-curable inks, also known as UV-curing or UV-hardening inks, are formulations that cure almost instantly when exposed to ultraviolet light. This rapid curing process eliminates the need for drying time, significantly speeding up production processes. These inks are composed of oligomers, monomers, photoinitiators, and pigments or dyes, each playing a crucial role in the ink’s performance characteristics.
Oligomers and monomers are the building blocks that form the polymer network upon curing, providing the ink with its durability and adhesion properties. Photoinitiators are responsible for initiating the polymerization reaction when exposed to UV light. Pigments or dyes determine the ink’s color and opacity, while additional additives can enhance specific properties such as flexibility, scratch resistance, or chemical resistance.
Factors to Consider When Choosing UV-Curable Inks
Substrate Compatibility
One of the primary considerations when selecting UV-curable ink is the type of substrate you will be printing on. Different substrates, such as plastics, metals, glass, paper, and textiles, have varying surface energies and absorption rates, which can affect ink adhesion and cure performance. It’s essential to choose an ink that is specifically formulated to adhere well to your particular substrate and provides the desired finish.
For instance, if you’re printing on a flexible plastic material, you’ll need an ink with good flexibility to prevent cracking or peeling when the substrate is bent. Similarly, printing on a non-absorbent surface like glass or metal requires an ink with excellent adhesion properties to ensure a durable and long-lasting print.
Curing Requirements
UV-curable inks require exposure to UV light to cure properly. The curing process can be influenced by factors such as the intensity and wavelength of the UV light, the cure speed, and the ink layer thickness. It’s crucial to match the ink’s curing requirements with your existing UV curing equipment or plan for the necessary adjustments.
Some inks may require high-intensity UV lamps for rapid curing, while others may be more suited to lower-intensity settings. Additionally, the cure speed can impact production efficiency, with faster-curing inks allowing for higher throughput rates. Consider the ink’s cure response and how it aligns with your production goals and equipment capabilities.
Performance Characteristics
The performance characteristics of UV-curable inks can vary significantly depending on the application. Key properties to consider include durability, scratch resistance, chemical resistance, weatherability, and flexibility.
For outdoor applications, such as signage or automotive graphics, you’ll need an ink with excellent weatherability to withstand exposure to UV rays, moisture, and temperature fluctuations. In industrial settings, where the printed surface may be subjected to harsh chemicals or abrasive conditions, chemical resistance and scratch resistance become critical factors.
Flexibility is another important consideration, especially for applications where the substrate will be bent or folded, such as packaging or textile printing. Ensure that the ink you choose can maintain its integrity and appearance under the expected conditions of use.
Color and Opacity
The color and opacity of UV-curable inks can significantly impact the visual appeal and effectiveness of your prints. When selecting an ink, consider the desired color range, vibrancy, and opacity for your application.
Some inks may offer a wider color gamut and more vibrant colors than others, which can be crucial for applications where color accuracy and visual impact are essential. Additionally, the opacity of the ink can affect its coverage on the substrate, with more opaque inks providing better hiding power and reducing the need for multiple layers.
Environmental and Safety Considerations
As with any material used in manufacturing processes, it’s important to consider the environmental impact and safety aspects of UV-curable inks. Look for inks that are formulated with low volatile organic compound (VOC) content, as these contribute less to air pollution and are generally more environmentally friendly.
Furthermore, ensure that the ink you choose complies with relevant safety regulations and standards. Check for any hazardous materials or potential health risks associated with the ink’s use, and follow proper handling and disposal procedures to protect your workforce and the environment.
Cost and Availability
Last but not least, cost and availability are practical considerations that can influence your choice of UV-curable ink. While it’s tempting to opt for the cheapest option available, it’s important to balance cost with performance and quality. A more expensive ink may offer better durability, color accuracy, or other benefits that outweigh the initial cost savings of a cheaper alternative.
Additionally, consider the availability of the ink and the reliability of the supplier. A consistent supply of high-quality ink is essential for maintaining production schedules and meeting customer demands. Research the supplier’s reputation, customer service, and support capabilities to ensure a smooth and reliable supply chain.
Choosing the right UV-curable ink for your application requires careful consideration of several factors, including substrate compatibility, curing requirements, performance characteristics, color and opacity, environmental and safety considerations, and cost and availability. By taking the time to evaluate these aspects and understanding your specific needs, you can select an ink that delivers optimal performance, durability, and visual appeal for your prints.
Remember, the key to successful UV-curable ink selection is to strike a balance between the ink’s properties and your application requirements. With the right ink, you can enhance the quality and efficiency of your printing processes, opening up new possibilities for innovation and growth in your industry.