How to Choose the Right UV-Curable Ink for Your Printing Needs
In the realm of modern printing technology, UV-curable inks have revolutionized the way we approach various printing applications, from graphic arts to industrial marking. Their ability to cure instantly upon exposure to ultraviolet light offers numerous advantages, including faster production times, enhanced durability, and improved print quality. However, with a plethora of options available in the market, selecting the right UV-curable ink for your specific printing needs can be a daunting task. This comprehensive guide aims to simplify the process by outlining key considerations and steps to ensure you make an informed decision.
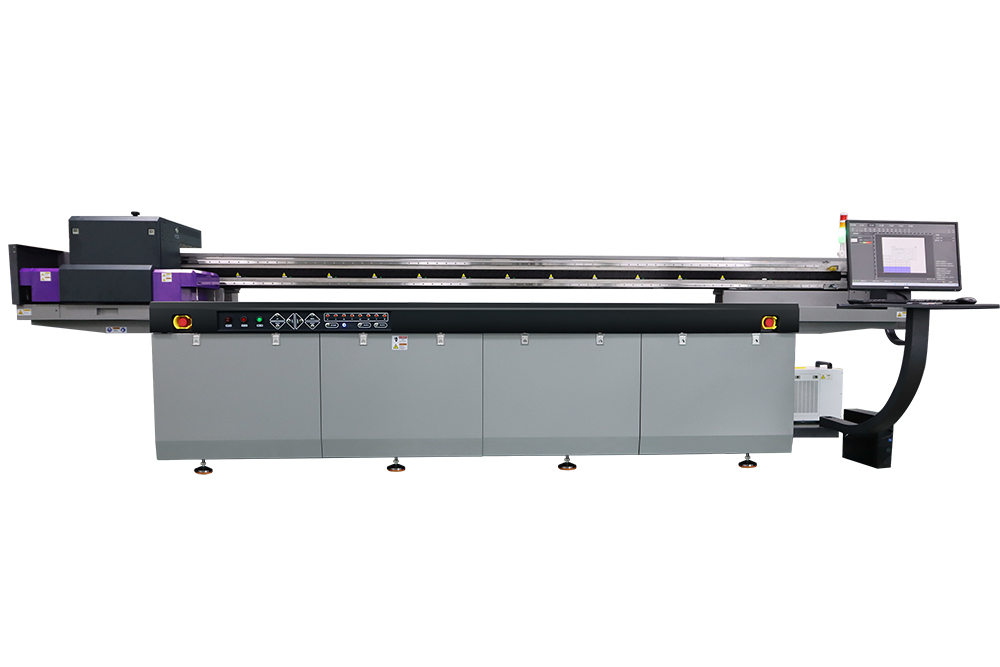
Understanding the Basics of UV-Curable Inks
UV-curable inks are formulated with special resins, pigments, and additives that react when exposed to UV light. This chemical reaction, known as curing, transforms the liquid ink into a solid, creating a durable and vibrant print. The primary benefits of UV-curable inks include:
Rapid Curing: Unlike traditional inks that require time to dry, UV-curable inks cure instantly, significantly reducing production time.
Enhanced Durability: Cured inks are resistant to fading, abrasion, and chemicals, making them ideal for outdoor and industrial applications.
Versatility: UV-curable inks can be used on a wide range of substrates, including plastics, metals, glass, and more.
Environmental Benefits: They often contain fewer volatile organic compounds (VOCs) compared to solvent-based inks, contributing to a more environmentally friendly printing process.
Key Considerations in Choosing UV-Curable Inks
To choose the most suitable UV-curable ink for your printing needs, you must evaluate several factors related to your specific application, the printing equipment, and the desired outcome. Here are the critical aspects to consider:
1. Substrate Compatibility
The type of material you plan to print on is paramount. UV-curable inks adhere differently to various substrates. For instance:
Rigid Substrates: Materials like glass, metal, and rigid plastics require inks that can form a strong bond and withstand potential stress.
Flexible Substrates: Soft materials such as vinyl, fabrics, and flexible packaging films need inks that maintain flexibility after curing.
Ensure the ink manufacturer specifies compatibility with your chosen substrate, and consider testing samples to verify adhesion and performance.
2. Print Application
The intended use of the printed material will greatly influence your ink choice. Ask yourself:
Is the print for outdoor or indoor use? Outdoor applications demand inks with high resistance to UV rays, weathering, and environmental pollutants.
Will the print be subjected to mechanical stress? If so, you need inks that offer excellent abrasion resistance.
Do you require special effects? Metallic, fluorescent, or textured finishes may necessitate specialized inks.
Understanding the application will help you select an ink that meets the necessary performance criteria.
3. Curing Equipment
The type and configuration of your UV curing equipment play a crucial role. Consider:
Wavelength: Different UV inks require specific wavelengths of light to cure effectively. Ensure your curing system matches the ink’s requirements.
Curing Speed: The speed of the curing process can affect the ink’s final properties. Faster curing might be desirable for high-volume production but could impact ink penetration and adhesion.
Energy Output: Insufficient UV energy can result in incomplete curing, leading to poor durability and print quality.
Consult with both your ink supplier and curing equipment manufacturer to ensure compatibility and optimal settings.
4. Color and Pigmentation
Achieving the desired color accuracy and consistency is vital. Factors to consider include:
Color Range: Ensure the ink set offers the necessary colors and can achieve the desired color gamut for your application.
Pigment Quality: High-quality pigments ensure better lightfastness and color stability over time.
Opacity and Transparency: Depending on your design, you may need inks that offer high opacity or those that can be used for transparent effects.
Request color swatches or samples to assess the ink’s performance in terms of color reproduction and stability.
5. Environmental and Safety Considerations
While UV-curable inks are generally more environmentally friendly than solvent-based alternatives, it’s essential to:
Check for VOC Content: Ensure the inks comply with local environmental regulations regarding VOC emissions.
Assess Handling Requirements: Some inks may require special handling or storage conditions to ensure safety.
Dispose of Waste Properly: Understand the proper disposal methods for unused inks and cleaning materials to minimize environmental impact.
Always consult safety data sheets (SDS) provided by the ink manufacturer for detailed guidance.
6. Cost and Budget Considerations
While cost shouldn’t be the sole determining factor, it’s crucial to:
Evaluate Total Cost: Consider not just the price per liter but also factors like ink consumption, curing efficiency, and potential waste.
Assess Long-Term Value: Sometimes, investing in higher-quality inks with better durability and performance can lead to cost savings in the long run by reducing the need for frequent replacements or repairs.
Explore Bulk Purchasing Options: Many manufacturers offer discounts for bulk purchases, which can be beneficial for large-scale projects.
7. Technical Support and Service
Finally, don’t overlook the importance of technical support and customer service. A reliable ink supplier should offer:
Technical Assistance: Access to experts who can provide guidance on ink selection, troubleshooting, and optimization.
Training: Especially if you’re new to UV-curable inks, training for your team on proper handling, printing, and curing techniques can be invaluable.
After-Sales Support: Prompt resolution of any issues that may arise after purchase is crucial to minimizing downtime and maintaining productivity.
Steps to Choose the Right UV-Curable Ink
Define Your Requirements: Clearly outline the specifics of your printing project, including substrate, application, desired finish, and budget.
Research: Compile a list of potential ink manufacturers and suppliers that specialize in UV-curable inks.
Request Samples: Obtain samples of inks that seem to meet your criteria and test them on your substrates and equipment.
Evaluate Performance: Assess the print quality, curing efficiency, color accuracy, and durability of the samples.
Consult with Experts: Engage with technical representatives from the ink suppliers to address any questions or concerns.
Compare Costs: Analyze the total cost implications, considering ink consumption, curing costs, and potential waste.
Make a Decision: Based on your evaluations, select the ink that best balances performance, cost, and support.
Choosing the right UV-curable ink is a multifaceted process that requires careful consideration of your specific printing needs, substrate compatibility, application requirements, curing equipment, color specifications, environmental impact, cost, and the level of support provided by the supplier. By systematically evaluating these factors and conducting thorough testing, you can ensure that you select an ink that not only meets but exceeds your expectations, delivering outstanding print quality and durability for your projects. Remember, the key to success lies in understanding your unique requirements and partnering with a knowledgeable supplier who can provide the right solutions and support.