How to Ensure Color Accuracy and Consistency with a UV Flatbed Printer
In the realm of digital printing, achieving impeccable color accuracy and consistency is paramount. This is especially true when utilizing a UV flatbed printer, a versatile device capable of producing high-quality prints on a wide range of substrates. Whether you’re printing marketing materials, signage, or artistic reproductions, the ability to replicate colors faithfully is crucial. However, ensuring color accuracy and consistency with a UV flatbed printer is a multifaceted endeavor that involves careful calibration, understanding color management principles, and employing best practices in print production. In this article, we will delve into the essential steps and considerations to help you achieve outstanding color results with your UV flatbed printer.
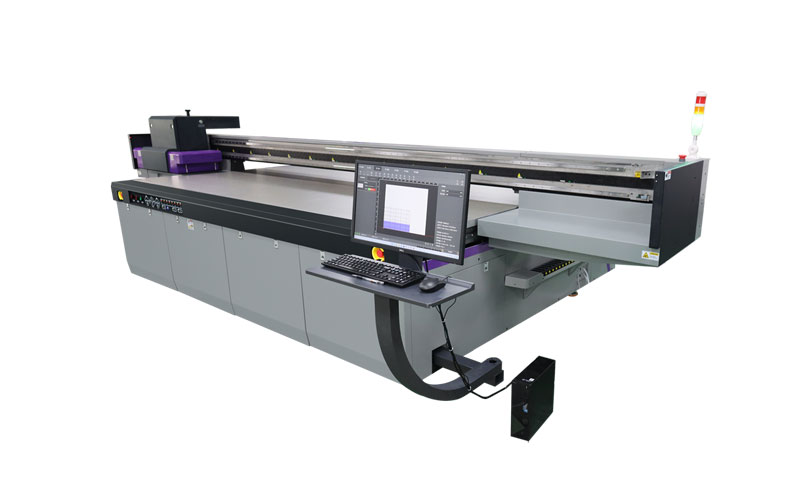
Understanding the Basics of Color Management
Before diving into the specifics of UV flatbed printing, it’s important to grasp the fundamentals of color management. Color management is the process of controlling the way colors are represented and reproduced across different devices, such as cameras, monitors, and printers. The goal is to ensure that the colors you see on your screen match as closely as possible to the colors produced by the printer.
At the heart of color management lies the color space or color model. Common color models include RGB (used for digital displays) and CMYK (used for printing). UV flatbed printers typically use CMYK ink sets, where C stands for cyan, M for magenta, Y for yellow, and K for key (black). Understanding how these colors interact and are processed by the printer is fundamental to achieving accurate and consistent results.
Printer Calibration: The Foundation of Color Accuracy
Printer calibration is the first step towards ensuring color accuracy with a UV flatbed printer. Calibration involves adjusting the printer’s settings to achieve the desired color output. This process typically includes:
Profiling the Printer: Using specialized software and a colorimeter or spectrophotometer, you can create a color profile (or ICC profile) for your printer. This profile maps the printer’s color capabilities to a standard color space, such as Adobe RGB or sRGB, allowing for more accurate color matching.
Linearization: This step ensures that the printer’s ink output is consistent across its entire range. Linearization adjusts the amount of ink deposited to achieve a predictable and smooth gradation of colors.
Color Adjustment: After profiling, you may need to make fine adjustments to the printer’s color settings to better align with your desired color output. This can involve tweaking ink densities, dot gain, and other parameters.
Regular calibration is essential, as printer performance can vary over time due to factors such as ink age, nozzle wear, and environmental conditions. It’s recommended to calibrate your UV flatbed printer at least once a month, or more frequently if you notice significant color shifts.
Choosing the Right Substrate
The choice of substrate can significantly impact color accuracy and consistency. Different materials absorb ink differently, which can affect color saturation, brightness, and contrast. When selecting a substrate for your UV flatbed printer, consider the following:
Ink Absorption: Some materials, such as uncoated papers, absorb more ink, resulting in richer, deeper colors. Others, like certain plastics or metals, may have a lower ink absorption rate, leading to lighter or more muted colors.
Surface Texture: The texture of the substrate can affect how ink is deposited. Smooth surfaces generally produce sharper, more consistent colors, while textured surfaces may create a more diffused, less uniform appearance.
Material Compatibility: Ensure that the substrate you choose is compatible with UV inks and the printing process. Some materials may require specific pretreatment or coatings to ensure proper ink adhesion and color fidelity.
Color Management Software and Tools
In addition to printer calibration, utilizing color management software can further enhance color accuracy. These tools help bridge the gap between the digital file and the printed output by managing color transformations and ensuring consistency across different devices.
RIP Software: Raster Image Processors (RIPs) are essential for translating digital files into a format that the printer can understand. Advanced RIP software often includes color management features that allow for precise color adjustments and the application of ICC profiles.
Color Management Systems: Software like Adobe Photoshop, Illustrator, and InDesign integrate seamlessly with color management systems, allowing you to work in a controlled color environment. By setting your working space to match your printer’s profile, you can better predict how colors will print.
Proofing Solutions: For critical color applications, consider using proofing solutions that simulate the final printed output. These can be hardware-based, like digital proofing printers, or software-based, utilizing color simulation tools.
Best Practices for Print Production
Achieving and maintaining color accuracy and consistency with a UV flatbed printer also requires adhering to best practices in print production:
Consistent Environmental Conditions: Keep your print shop’s environment as stable as possible in terms of temperature and humidity. Fluctuations in these conditions can affect ink viscosity and substrate behavior, leading to color variations.
Ink Maintenance: Regularly clean and maintain your printer’s ink system to prevent clogs and ensure that ink flows consistently. Use high-quality inks recommended by the printer manufacturer to avoid color shifting and other issues.
Print Settings: Fine-tune your print settings for each job, taking into account factors like resolution, ink coverage, and print speed. These settings can significantly affect color reproduction and should be adjusted based on the specific requirements of the project.
Quality Control: Implement a robust quality control process that includes regular color checks and test prints. Use control strips or color bars to monitor color accuracy and consistency throughout the print run.
Operator Training: Ensure that your print operators are well-trained in color management principles and the specific features of your UV flatbed printer. Knowledgeable operators can make informed decisions and adjustments to maintain color accuracy.
Conclusion
Ensuring color accuracy and consistency with a UV flatbed printer is a complex but achievable goal. By understanding the principles of color management, regularly calibrating your printer, choosing the right substrates, utilizing color management software, and adhering to best practices in print production, you can produce high-quality prints with accurate and consistent colors. Remember, achieving excellence in color reproduction is an ongoing process that requires attention to detail and a commitment to continuous improvement. With the right tools and strategies in place, you can confidently deliver outstanding print results that meet or exceed your clients’ expectations.