How to Ensure Color Accuracy with a UV Flatbed Printer
How to Ensure Color Accuracy with a UV Flatbed Printer
In today’s highly competitive printing industry, color accuracy is a critical factor that determines the success of a print job. UV flatbed printers, known for their versatility and ability to print on a wide range of materials, offer a robust solution for ensuring high-quality prints with precise color reproduction. This article will delve into various aspects of ensuring color accuracy with a UV flatbed printer, covering topics such as color management, equipment calibration, material selection, and the use of advanced tools like color measurement devices.
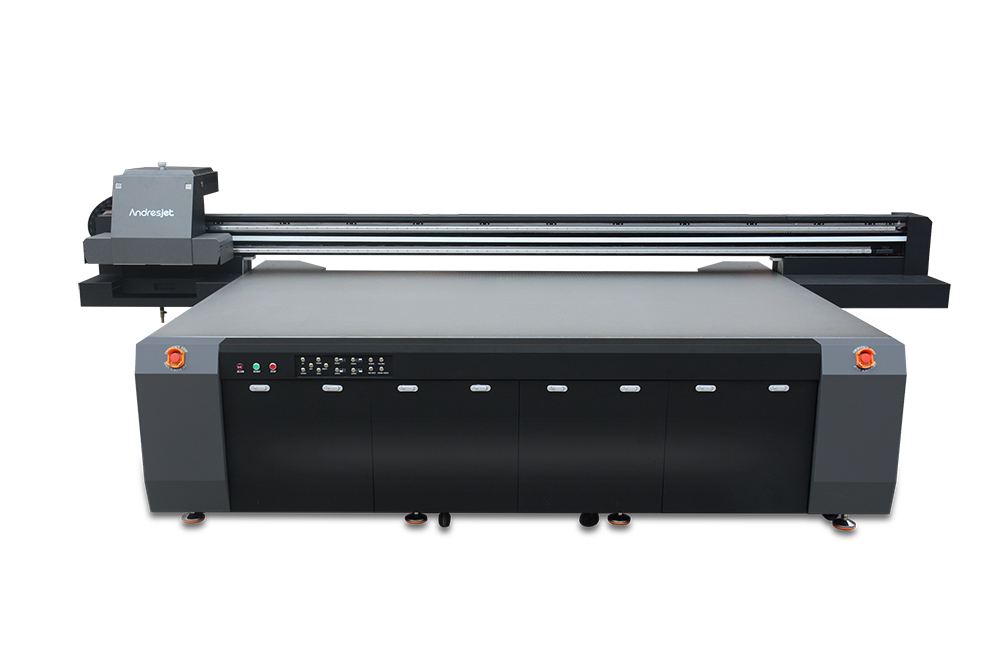
Understanding Color Accuracy
Color accuracy refers to the ability of a print to match the original design or color specifications. Achieving color accuracy is crucial for maintaining brand consistency and customer satisfaction. Several factors can influence color accuracy, including the printer’s capabilities, ink formulation, substrate properties, and the environment in which the printing process occurs.
Color Spaces and Color Conversion
To understand color accuracy, it’s essential to grasp the concept of color spaces. A color space is a mathematical model that describes the range of colors that a device can produce or perceive. The most common color spaces in the printing industry include RGB (for screens and monitors) and CMYK (for printing presses).
Color conversion involves transforming colors from one color space to another. For example, when designing graphics on a computer screen using RGB, the colors must be converted to CMYK for accurate reproduction on a printed piece. This process requires precise color management to avoid color shifts and ensure the printed piece matches the design intent.
Color Management for UV Flatbed Printers
Color management is a systematic approach to maintaining color consistency across different devices and materials. For UV flatbed printers, color management involves several key steps:
1. Calibrating the Printer
Printer calibration involves adjusting the printer’s settings to ensure consistent color output. This process typically includes:
Nozzle Check and Cleaning: Ensuring the printer’s nozzles are free from clogs and producing even ink droplets.
Head Alignment: Adjusting the printer heads to ensure that the ink is deposited accurately on the substrate.
Color Profiling: Creating a profile that maps the printer’s color output to a known color space. This profile is used by the RIP software to convert design files into printer-ready data.
2. Using High-Quality Inks
The type and quality of ink used in a UV flatbed printer significantly impact color accuracy. High-quality inks, such as those specifically formulated for UV curing, offer better color consistency and durability.
UV-Curable Inks: These inks are exposed to UV light to cure instantly, providing excellent adhesion and scratch resistance.
Ink Consistency: Ensuring that the ink formulation remains consistent over time is crucial for maintaining color accuracy.
3. Selecting the Right Substrate
The substrate (the material being printed on) can significantly affect color accuracy. Different substrates have varying absorption, reflection, and surface properties, which can alter the appearance of the printed colors.
Testing Substrates: It’s essential to test different substrates with the UV flatbed printer to determine which ones offer the best color accuracy.
Substrate Preparation: Ensuring that the substrate is clean, flat, and free from contaminants can also contribute to better color accuracy.
4. Controlling the Printing Environment
The environment in which the printing process occurs can also influence color accuracy. Factors such as temperature, humidity, and lighting can affect the behavior of the ink and the substrate.
Temperature and Humidity Control: Maintaining a consistent temperature and humidity level in the printing area can help ensure stable ink performance.
Lighting Conditions: Proper lighting conditions are essential for accurately assessing color accuracy during the printing process.
Advanced Tools for Ensuring Color Accuracy
In addition to fundamental color management practices, several advanced tools can help ensure color accuracy with a UV flatbed printer:
1. Spectrophotometers and Colorimeters
Spectrophotometers and colorimeters are devices used to measure color accurately. They can be used to:
Profile Substrates: Create color profiles for different substrates to ensure consistent color output.
Measure Printed Samples: Compare printed samples to the original design or color specifications to identify any discrepancies.
2. Color Management Software
Color management software, such as those offered by companies like X-Rite and Datacolor, can help streamline the color management process. These software solutions often include:
Profiler Creation: Tools for creating and editing color profiles.
Color Matching: Features for matching printed colors to reference standards.
Workflow Integration: Compatibility with RIP software and other print production tools.
3. Quality Control Checks
Implementing rigorous quality control checks throughout the printing process can help ensure color accuracy. This may include:
Proofing: Printing color proofs before running the full job to identify any color issues early on.
Inspection: Conducting visual inspections of printed samples to ensure they match the original design or color specifications.
Feedback Loop: Using the information gathered during quality control checks to make necessary adjustments to the printer’s settings or the design files.
Case Studies and Practical Examples
To further illustrate the importance of ensuring color accuracy with a UV flatbed printer, let’s consider a few case studies and practical examples:
Case Study 1: Printing on Acrylic
A company specializing in printing on acrylic materials uses a UV flatbed printer to produce signs and displays. To ensure color accuracy, they follow these steps:
Profile Creation: They create custom color profiles for different types of acrylic substrates.
Ink Selection: They use high-quality UV-curable inks that are specifically formulated for acrylic materials.
Environment Control: They maintain a consistent temperature and humidity level in their printing area.
Case Study 2: Printing on Metallic Substrates
A printer working with metallic substrates, such as aluminum or stainless steel, faces unique challenges in achieving color accuracy. To overcome these challenges, they:
Substrate Preparation: They thoroughly clean and pre-treat the metallic substrates to ensure optimal ink adhesion.
Ink Testing: They conduct extensive testing to find the best ink formulation for their specific needs.
Color Matching: They use spectrophotometers to match the printed colors to reference standards.
Practical Example: Printing Custom Phone Cases
A company that prints custom phone cases uses a UV flatbed printer to offer a wide range of design options. To ensure color accuracy, they:
Design Verification: They verify the color settings in the design software before sending the job to the printer.
Printer Calibration: They regularly calibrate the printer to maintain consistent color output.
Quality Control: They inspect each printed phone case to ensure it matches the customer’s color specifications.
Conclusion
Ensuring color accuracy with a UV flatbed printer requires a combination of fundamental color management practices, advanced tools, and rigorous quality control checks. By carefully calibrating the printer, selecting high-quality inks and substrates, controlling the printing environment, and using tools like spectrophotometers and color management software, printers can achieve consistent and accurate color reproduction. As the printing industry continues to evolve, the ability to deliver high-quality prints with precise color accuracy will remain a critical factor in differentiating successful businesses from the competition.