How to Ensure Consistent Print Quality Across Different Materials?
How to Ensure Consistent Print Quality Across Different Materials?
In the realm of printing, achieving consistent quality across various materials is a paramount objective for businesses seeking to maintain brand integrity, customer satisfaction, and operational efficiency. The challenge lies in the inherent differences among substrates, which can significantly affect how ink or toner adheres, dries, and appears. From paper and cardboard to plastics, metals, and textiles, each material possesses unique properties that demand tailored approaches to ensure optimal print outcomes. This article delves into the strategies and techniques for ensuring consistent print quality across different materials.
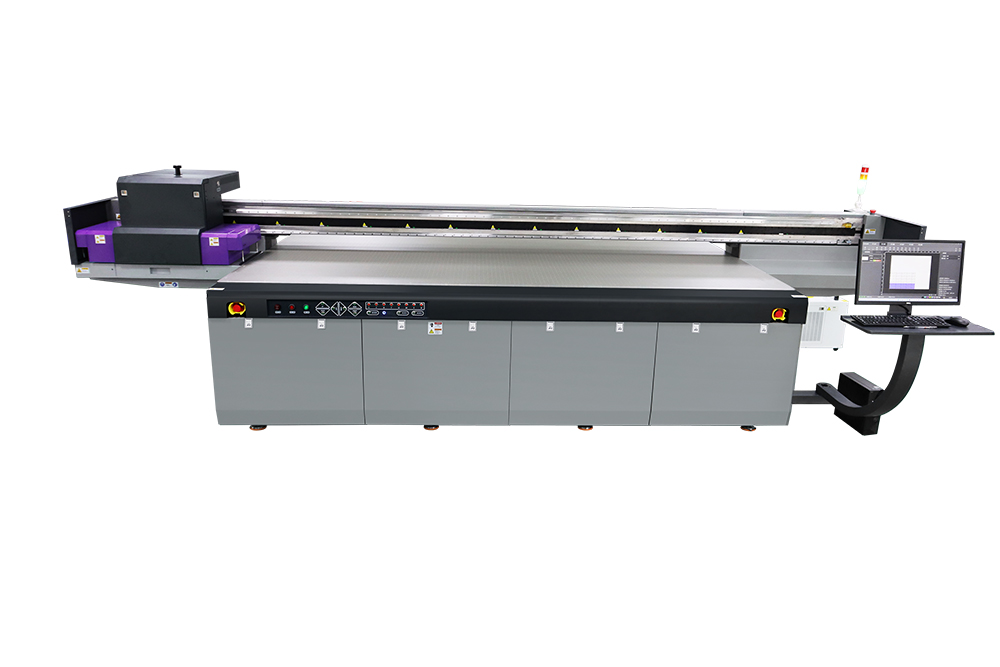
1. Understand Material Properties
The first step in ensuring consistent print quality is understanding the properties of the materials you intend to print on. Key material characteristics include surface energy, porosity, texture, thickness, and chemical composition. Surface energy, for instance, determines how well ink can wet and adhere to the material. Porosity affects ink absorption, while texture can influence ink distribution and final appearance. Thickness and chemical composition can impact drying times and ink durability.
By familiarizing yourself with these properties, you can select appropriate inks, printing techniques, and pretreatment methods that are compatible with specific materials. For example, low-surface-energy materials like polypropylene (PP) may require special inks or surface treatments to achieve good adhesion.
2. Choose the Right Ink and Printing Technology
Ink selection is crucial for maintaining consistent print quality. Different inks have varying degrees of compatibility with different materials. Water-based inks, for instance, are suitable for porous materials like paper but may not adhere well to non-porous surfaces such as plastics. UV-curable inks, on the other hand, offer excellent adhesion to a wide range of materials and are particularly suited for printing on plastics and metals due to their fast curing process.
The choice of printing technology also plays a pivotal role. Digital printing, including inkjet and laser printing, offers versatility in handling various materials and allows for easy adjustments in print settings. Screen printing, pad printing, and flexography, meanwhile, are more suited for specific applications and materials, offering high-volume capabilities with consistent quality.
3. Optimize Print Settings
Fine-tuning print settings is essential for achieving consistent quality across different materials. This includes adjusting ink density, dot gain, drying temperature, and print speed. Ink density controls the amount of ink deposited on the material, affecting color intensity and drying time. Dot gain refers to the spreading of ink dots after deposition, which can vary depending on the material’s porosity. Adjusting dot gain settings can help maintain consistent color and sharpness.
Drying temperature and print speed are particularly critical when printing on heat-sensitive or slow-drying materials. High temperatures can cause ink to crack or discolor on certain materials, while slow print speeds may lead to ink bleeding or smudging. Therefore, it’s crucial to find the optimal balance between these settings for each material.
4. Pre-Treatment and Surface Preparation
Pre-treatment processes can significantly enhance ink adhesion and overall print quality on challenging materials. Corona treatment, for example, is commonly used to increase the surface energy of non-porous materials like plastics, allowing inks to adhere better. Flame treatment is another method that briefly exposes the material surface to a controlled flame, improving wettability and ink adhesion.
Surface cleaning is also essential to remove dust, oils, and other contaminants that can hinder ink adhesion. This can involve simple wiping with an alcohol solution or more sophisticated methods like ultrasonic cleaning for delicate or intricate materials.
5. Calibrate and Maintain Equipment
Regular calibration and maintenance of printing equipment are vital for ensuring consistent print quality. Printer nozzles, screens, and pads can wear out or become clogged with ink over time, affecting print resolution and ink distribution. Regular cleaning and replacement of these components as needed can help maintain optimal print quality.
Calibrating the printing press to ensure accurate color reproduction is also crucial. This involves adjusting ink densities, color profiles, and print settings to match the desired output. Color management systems can assist in this process, providing a standardized way to measure and control color across different materials and print runs.
6. Conduct Material Testing
Before embarking on large-scale production, conducting thorough material testing is advisable. This involves printing test patterns or samples on the intended materials and evaluating them for ink adhesion, color accuracy, durability, and any other relevant quality metrics. Testing can help identify potential issues early on, allowing for adjustments in ink, printing settings, or pretreatment methods before full-scale production begins.
7. Monitor and Control Environmental Factors
Environmental factors such as temperature, humidity, and dust can impact print quality. High humidity can cause ink to dry slower, potentially leading to smudging or bleeding. Temperature variations can affect ink viscosity and print settings. Therefore, it’s important to monitor and control these factors within the printing environment to maintain consistent quality.
Conclusion
Ensuring consistent print quality across different materials is a multifaceted challenge that requires a comprehensive understanding of material properties, ink and printing technology, print settings, pretreatment methods, equipment maintenance, and environmental factors. By addressing each of these aspects, businesses can effectively overcome the inherent challenges posed by diverse substrates and achieve high-quality, consistent prints that meet their brand and customer requirements. Regular testing, calibration, and adaptation to new materials and technologies are also key to staying ahead in the ever-evolving printing industry.