How to Ensure Consistent Quality with a UV Flatbed Printer
How to Ensure Consistent Quality with a UV Flatbed Printer
In the realm of digital printing, UV flatbed printers have emerged as versatile and powerful tools capable of producing high-quality prints on a wide range of substrates. From rigid materials like metal, glass, and wood to flexible media such as vinyl and fabric, UV flatbed printers offer unparalleled flexibility and precision. However, ensuring consistent quality across all prints can be a challenge, requiring a blend of proper equipment maintenance, skilled operation, and meticulous attention to detail. In this article, we will explore the key strategies for maintaining consistent quality with a UV flatbed printer.
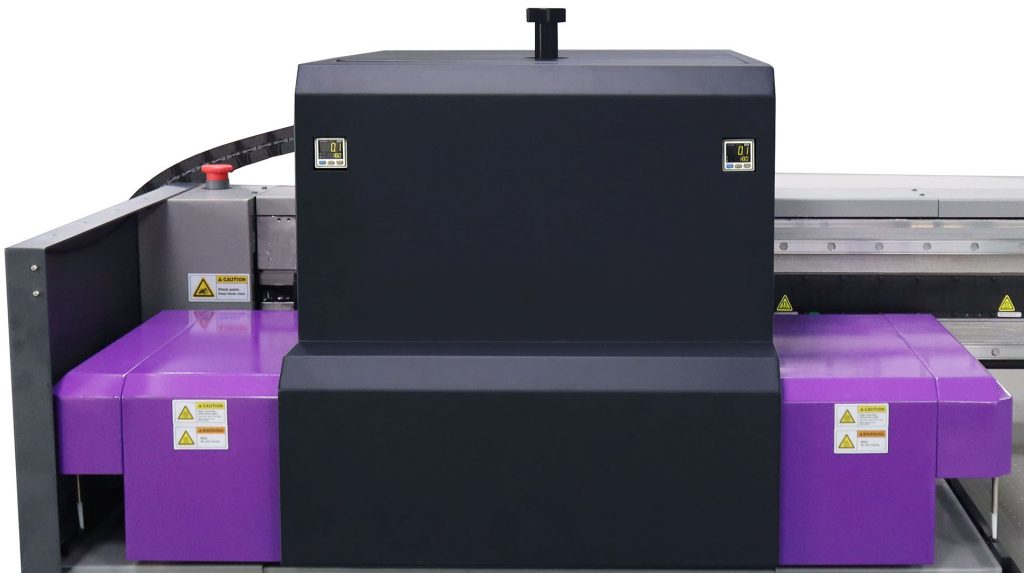
1. Understand Your Printer’s Capabilities and Limitations
Before diving into the intricacies of quality control, it’s crucial to have a thorough understanding of your UV flatbed printer’s capabilities and limitations. Each printer model comes with its unique set of specifications, including print resolution, color gamut, supported media types, and maximum print size. Familiarize yourself with the printer’s user manual and technical specifications to ensure that you’re working within its optimal parameters.
2. Regular Maintenance and Cleaning
Consistent quality begins with a well-maintained printer. Regular maintenance is essential to keep your UV flatbed printer in top working condition. This includes:
Daily Cleaning: At the start of each workday, inspect the print bed, print heads, and other critical components for dust, debris, or ink residue. Use a soft, lint-free cloth and approved cleaning solutions to gently clean these areas.
Weekly Maintenance: Perform more thorough cleaning tasks, such as cleaning the inside of the printer, checking for ink leaks, and ensuring that all moving parts are functioning smoothly.
Monthly Servicing: Schedule professional maintenance checks and servicing at regular intervals. This may include replacing worn-out parts, recalibrating the printer, and updating software and firmware.
3. Calibration and Profiling
Accurate color reproduction is crucial for maintaining consistent quality. This requires precise calibration and profiling of your printer and its associated software.
Printer Calibration: Regularly calibrate your printer to ensure that it’s producing accurate colors. This involves adjusting the printer’s settings to match a known color standard, typically using a calibration device and software.
Color Profiling: Create custom color profiles for different substrates and printing conditions. This ensures that the colors displayed on your monitor accurately match the printed output. Use a spectrophotometer to measure and analyze the printed colors, and adjust the profiles accordingly.
4. Choosing the Right Substrates and Inks
The quality of your prints is heavily influenced by the substrates and inks you use.
Substrates: Choose substrates that are compatible with your printer and suitable for your intended application. Consider factors such as material thickness, surface texture, and ink adhesion properties. Test different substrates to determine which ones provide the best results in terms of color saturation, durability, and overall appearance.
Inks: Use high-quality UV-curable inks that are specifically designed for your printer. These inks should offer excellent color vibrancy, adhesion, and resistance to fading and scratching. Experiment with different ink formulations to find the one that best suits your needs.
5. Optimizing Print Settings
The print settings you choose can significantly impact the quality of your prints. Take the time to experiment with different settings and find the optimal combination for your specific application.
Resolution: Higher resolutions generally result in sharper, more detailed prints. However, they also require more processing power and may slow down the printing process. Find a balance between resolution and print speed that meets your quality and productivity requirements.
Ink Coverage: Adjust the ink coverage settings to ensure that the right amount of ink is being applied to the substrate. Too much ink can lead to smudging and bleeding, while too little can result in faded colors and poor adhesion.
Curing Settings: UV flatbed printers use UV light to cure the ink as it’s printed. The intensity and duration of the UV exposure can affect the print’s durability and appearance. Experiment with different curing settings to find the optimal balance for your substrates and inks.
6. Skilled Operation and Training
The operator’s skill and knowledge play a crucial role in ensuring consistent quality. Proper training and ongoing education are essential for maximizing the potential of your UV flatbed printer.
Initial Training: Provide comprehensive training for new operators, covering topics such as printer operation, maintenance, and troubleshooting. This will help them understand the printer’s capabilities and limitations, and ensure that they’re using it correctly.
Ongoing Education: Encourage operators to attend workshops, seminars, and online courses to stay up-to-date with the latest printing technologies and best practices. This will help them continuously improve their skills and adapt to new challenges.
7. Quality Control and Inspection
Implement a robust quality control process to ensure that each print meets your standards for quality and consistency.
Pre-Print Checks: Before starting a print job, perform a thorough pre-print check to ensure that the substrate, ink, and print settings are correct. This will help prevent costly mistakes and ensure that the print process runs smoothly.
In-Process Monitoring: Monitor the print process closely, checking for any issues such as ink smudging, color inconsistencies, or print head clogs. Address these issues immediately to minimize waste and maintain print quality.
Post-Print Inspection: After the print job is complete, inspect the prints for any defects or inconsistencies. Use a magnifying glass or loupe to examine the prints closely, and make any necessary adjustments to the print settings or substrate choice.
8. Continuous Improvement and Feedback
Finally, foster a culture of continuous improvement and feedback within your printing environment. Encourage operators to share their experiences, challenges, and successes with each other, and use this information to refine your printing processes and improve quality.
Regular Reviews: Conduct regular reviews of your printing processes, identifying areas for improvement and implementing changes as needed. This may involve updating print settings, investing in new equipment, or providing additional training for operators.
Customer Feedback: Gather feedback from your customers to understand their expectations and preferences. Use this information to tailor your printing processes and ensure that you’re meeting their needs.
In conclusion, ensuring consistent quality with a UV flatbed printer requires a combination of proper equipment maintenance, skilled operation, and meticulous attention to detail. By understanding your printer’s capabilities, performing regular maintenance, calibrating and profiling your equipment, choosing the right substrates and inks, optimizing print settings, providing skilled operation and training, implementing a robust quality control process, and fostering a culture of continuous improvement and feedback, you can produce high-quality prints that meet your customers’ expectations and stand the test of time.