How to Ensure Durability of UV-Printed Graphics
How to Ensure Durability of UV-Printed Graphics
In the realm of visual communication, UV-printed graphics have emerged as a game-changer, offering vibrant colors, sharp details, and exceptional resistance to fading and weathering. Unlike traditional printing methods, UV printing utilizes ultraviolet light to cure inks instantly, resulting in durable and long-lasting images. However, ensuring the durability of these graphics involves more than just the printing process itself; it requires a comprehensive understanding of materials, preparation, application, and maintenance. This article delves into the essential steps and considerations to guarantee the longevity of UV-printed graphics.
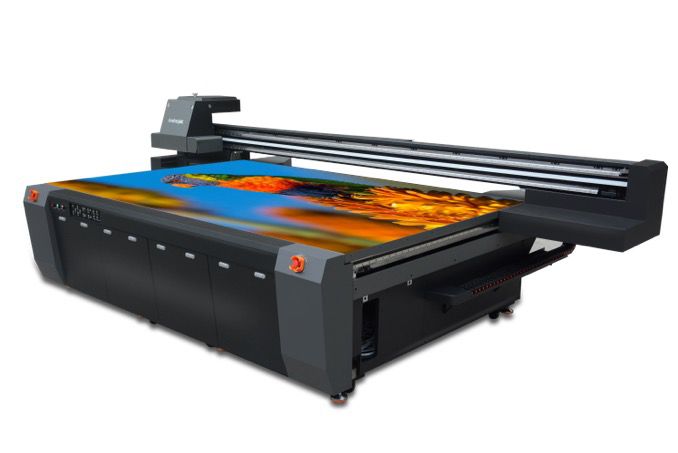
1. Choosing the Right Substrate
The substrate, or material upon which the graphic is printed, plays a critical role in determining the durability of UV-printed graphics. Different substrates have varying degrees of porosity, flexibility, and resistance to environmental factors.
Rigid Substrates: Materials like acrylic, polycarbonate, and aluminum are popular for their durability and resistance to warping. Acrylic, in particular, offers excellent clarity and weatherability, making it ideal for outdoor applications.
Flexible Substrates: Vinyl, polyester, and other flexible materials are often used for applications that require bending or wrapping around curves. When choosing flexible substrates, opt for those with high tensile strength and UV resistance.
Textured Substrates: For a unique visual effect, textured substrates can be used. However, it’s crucial to ensure that the texture does not interfere with the ink’s ability to adhere properly.
Before printing, always test the substrate for compatibility with UV inks and assess its performance under expected conditions.
2. Proper Print Preparation
The pre-print preparation stage is where the foundation for durability is laid. This includes file setup, color management, and ensuring the design is optimized for UV printing.
File Resolution: High-resolution files (typically 300 dpi or higher) ensure that graphics remain sharp and detailed, even when viewed from a distance.
Color Calibration: Proper color calibration ensures that the colors on the printed graphic match the intended design. Use ICC profiles specific to the printer and substrate being used.
Bleed and Margins: Include bleeds and margins in the design to avoid any unprinted edges that could detract from the graphic’s appearance or compromise its structural integrity.
White Ink Usage: For transparent or semi-transparent substrates, using a white ink base layer can enhance color vibrancy and opacity, ensuring the graphics stand out even in bright sunlight.
3. Ink Selection and Application
The type and quality of UV inks used significantly impact the durability of the graphics.
Ink Composition: Look for inks that are specifically formulated for outdoor use, with high resistance to UV rays, water, and abrasion. Some inks also contain additives that enhance flexibility or adhesion to specific substrates.
Layering Technique: Applying multiple thin layers of ink, rather than a single thick layer, can improve cure efficiency and reduce the risk of cracking or peeling.
Curing Process: The curing process is crucial. UV inks require exposure to a specific wavelength of light to cure properly. Ensure the UV lamps are regularly maintained and calibrated to deliver the correct amount of energy. Over-curing can lead to ink embrittlement, while under-curing can result in poor adhesion and reduced durability.
4. Surface Preparation
The surface of the substrate must be clean, dry, and free of any contaminants that could interfere with ink adhesion.
Cleaning: Use appropriate cleaners and solvents to remove dust, grease, and other impurities. For porous materials, ensure they are fully dry before printing to prevent ink from bleeding.
Priming: In some cases, applying a primer can improve ink adhesion and enhance the overall durability of the print. Choose a primer that is compatible with both the substrate and the UV inks being used.
5. Application Techniques
The way graphics are applied can also affect their durability.
Lamination: Applying a protective laminate can significantly extend the lifespan of UV-printed graphics, especially in high-traffic or harsh environments. Laminates can provide additional resistance to scratches, chemicals, and UV rays.
Mounting: Use high-quality adhesives and mounting materials that are compatible with both the substrate and the application surface. Ensure the graphic is securely mounted to prevent it from lifting or bubbling over time.
Edge Sealing: For graphics that are exposed to moisture, edge sealing can prevent water infiltration, which could cause delamination or ink bleeding.
6. Environmental Considerations
Understanding the environmental conditions in which the graphics will be displayed is crucial for ensuring their durability.
Outdoor Graphics: Graphics intended for outdoor use must withstand temperature extremes, UV exposure, moisture, and pollution. Choose materials and inks that are specifically rated for outdoor durability.
Indoor Graphics: While indoor graphics may not face the same environmental challenges as outdoor ones, they still need to resist fading from indoor lighting and maintain their appearance over time.
Climate Control: In areas with extreme temperature fluctuations or high humidity, additional measures such as climate control or the use of specialized materials may be necessary.
7. Maintenance and Care
Regular maintenance can significantly extend the life of UV-printed graphics.
Cleaning: Use non-abrasive cleaners and soft cloths to remove dust and debris. Avoid harsh chemicals that could damage the inks or substrates.
Inspection: Regularly inspect graphics for signs of wear, such as fading, cracking, or peeling. Address any issues promptly to prevent further damage.
Repair and Replacement: For graphics that are damaged or have reached the end of their lifespan, consider repair or replacement to maintain the intended visual impact and messaging.
8. Advancements in UV Printing Technology
Staying abreast of advancements in UV printing technology can also contribute to improved durability.
New Ink Formulas: Manufacturers are constantly developing new ink formulas that offer enhanced durability, flexibility, and environmental resistance.
Printer Upgrades: Upgrading to newer UV printers that offer improved cure efficiency, higher resolution, and better color management can result in higher-quality, more durable graphics.
Software Innovations: Advanced design and RIP software can optimize print files for better ink distribution and cure efficiency, leading to improved durability.
Conclusion
Ensuring the durability of UV-printed graphics is a multifaceted process that involves careful selection of materials, meticulous print preparation, precise ink application, and proactive maintenance. By understanding the unique requirements of each project and staying informed about the latest advancements in UV printing technology, professionals can create graphics that not only look stunning but also stand the test of time. Whether for outdoor signage, indoor displays, or any other application, the key to successful UV printing lies in the details and the commitment to quality throughout the entire process.