How to Minimize Ink Usage in UV Flatbed Printing?
How to Minimize Ink Usage in UV Flatbed Printing?
UV flatbed printing has revolutionized the printing industry, offering unparalleled versatility and efficiency in producing high-quality prints on various materials. However, one of the challenges faced by printers is managing ink consumption effectively. Ink is not only a significant cost factor but also influences the printer’s environmental footprint. This article explores practical strategies to minimize ink usage in UV flatbed printing, ensuring cost-effectiveness and promoting sustainability.
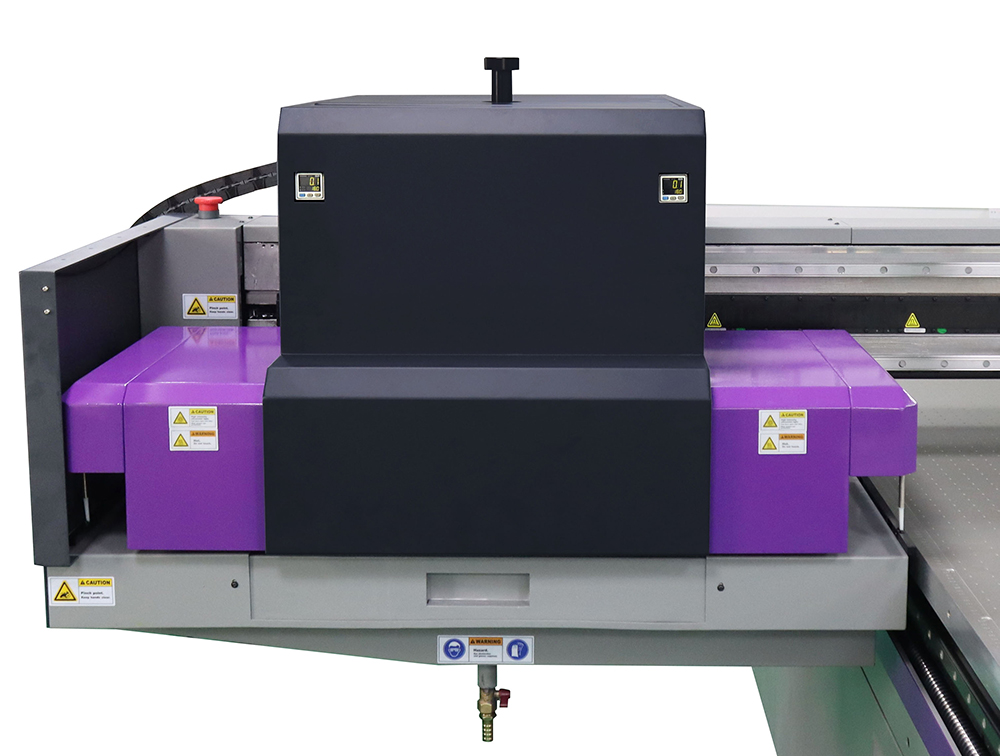
Understanding UV Flatbed Printing
UV flatbed printers use ultraviolet (UV) light to cure ink instantly after it is applied to the material. This process allows for printing on diverse substrates, including glass, plastic, metal, and even irregular surfaces. The ink is formulated to cure rapidly when exposed to UV light, resulting in durable and vibrant prints.
Why Minimize Ink Usage?
Minimizing ink usage in UV flatbed printing is crucial for several reasons:
Cost Savings: Ink is a significant expense in printing operations. Reducing ink consumption directly impacts the cost per print, enhancing profitability.
Environmental Impact: UV inks, while generally more environmentally friendly than solvent-based inks, still contribute to waste if overused. Minimizing ink usage reduces the carbon footprint of printing operations.
Printer Maintenance: Excessive ink usage can lead to more frequent cleaning and maintenance requirements, affecting printer uptime and productivity.
Strategies to Minimize Ink Usage
Optimize Print Settings
Ink Density: Adjust the ink density settings according to the specific job requirements. Lowering ink density can significantly reduce ink usage while maintaining acceptable print quality.
Print Resolution: Evaluate whether high-resolution printing is necessary for every job. Lowering the resolution can decrease ink consumption, especially for larger print areas.
Utilize Ink-Saving Features
Ink Drop Management: Many modern UV flatbed printers offer advanced ink drop management systems. These systems optimize ink droplet size and placement, reducing ink waste.
Ink Recovery Systems: Some printers are equipped with ink recovery systems that collect and reuse excess ink, minimizing waste and reducing the need for frequent ink replenishment.
Proper Printer Maintenance
Regular Cleaning: Keep the printer’s print head and ink system clean to ensure optimal ink flow and prevent ink wastage due to clogged nozzles.
Calibration: Regularly calibrate the printer to maintain accurate ink deposition, preventing over-inking.
Selective Ink Usage
Spot Color Printing: For jobs that require only a few colors, consider using spot colors instead of full-color printing. This approach can significantly reduce ink usage.
Ink Mixing: Carefully mix inks to achieve the desired colors, avoiding unnecessary ink waste.
Software Optimizations
File Preparation: Optimize print files to remove unnecessary elements and simplify complex designs, reducing the ink required for printing.
Print Preview and Proofing: Use print preview and proofing tools to ensure that the print job is set up correctly before commencing printing, minimizing ink waste due to errors.
Material Selection
Ink Adhesion: Choose materials that require less ink for adhesion. Some materials absorb ink more efficiently, reducing the need for excessive ink application.
Surface Preparation: Properly prepare the material surface to ensure optimal ink adhesion, reducing the likelihood of ink bleeding or the need for additional ink layers.
Training and Education
Operator Training: Train printer operators to understand ink usage and how to optimize print settings for each job.
Continuous Improvement: Encourage a culture of continuous improvement, where operators are motivated to find new ways to reduce ink usage without compromising print quality.
Ink Management Software
Ink Tracking: Implement ink management software to track ink usage and identify areas where ink waste occurs.
Job-Specific Ink Allocation: Use software to allocate the precise amount of ink required for each job, minimizing waste.
Consider Ink Type
Ink Quality: Choose high-quality UV inks that offer better coverage and adhesion, reducing the need for excessive ink application.
Ink Supplier Consultation: Consult with ink suppliers to understand the most efficient ink usage practices for specific applications.
Collaborative Approach
Customer Communication: Communicate with customers to understand their print quality expectations, allowing for adjustments that can reduce ink usage without compromising the final output.
Industry Best Practices: Collaborate with industry peers to share best practices for ink usage optimization.
Conclusion
Minimizing ink usage in UV flatbed printing is a multifaceted approach that involves optimizing print settings, utilizing ink-saving features, proper printer maintenance, selective ink usage, software optimizations, material selection, training and education, ink management software, considering ink type, and a collaborative approach. By implementing these strategies, printers can significantly reduce ink consumption, lowering costs, enhancing sustainability, and improving overall operational efficiency. As the printing industry continues to evolve, prioritizing ink usage optimization will remain a vital aspect of maintaining competitiveness and promoting environmental responsibility.