How to Optimize Ink Coverage on a UV Flatbed Printer?
How to Optimize Ink Coverage on a UV Flatbed Printer?
In the world of large-format printing, UV flatbed printers have become increasingly popular due to their versatility and efficiency. These printers use ultraviolet (UV) light to instantly cure inks on a variety of materials, resulting in durable, high-quality prints. However, to achieve optimal print results, it’s crucial to understand and optimize ink coverage. This article explores the various factors that affect ink coverage on a UV flatbed printer and provides practical tips on how to optimize it.
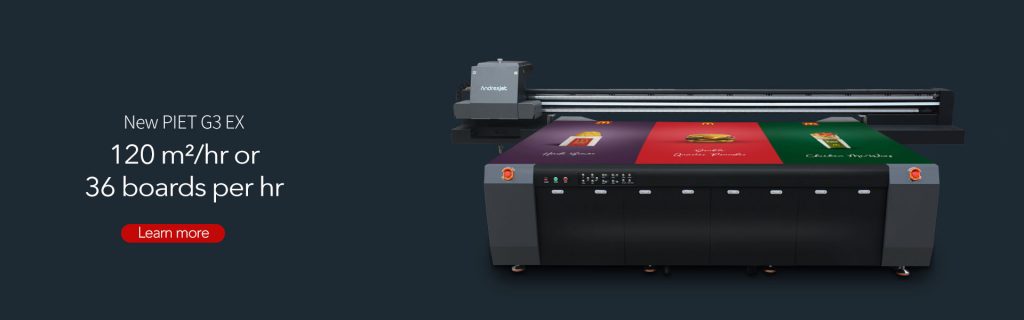
Understanding Ink Coverage
Ink coverage refers to the amount of ink laid down on the substrate during the printing process. It’s a critical factor in determining the final print quality, affecting both the visual appeal and durability of the print. Optimal ink coverage ensures vibrant colors, sharp details, and long-lasting prints.
Factors Affecting Ink Coverage
Ink Type and Quality: UV-curable inks are specially formulated to respond to UV light, undergoing a chemical reaction that causes them to solidify or “cure.” Different inks have varying viscosity, pigment size, and curing properties, all of which affect coverage. High-quality inks provide better color saturation and adhesion to the substrate.
Substrate Material: The type of material being printed on significantly impacts ink coverage. Different materials have varying absorption rates, surface textures, and porosity, which can affect how the ink spreads and adheres. For example, some materials may require a primer or special treatment to ensure optimal ink adhesion.
Print Settings: The print settings chosen, such as resolution, ink limit, and print speed, directly affect ink coverage. Higher resolutions typically require more ink to produce finer details, while faster print speeds may result in less ink being laid down.
Printer Maintenance: The condition of the printer heads, nozzles, and ink system can also influence ink coverage. Clogged nozzles or misaligned heads can lead to uneven ink distribution.
File Preparation: The quality of the graphic file being printed plays a role in ink coverage. A poorly optimized or low-resolution file may result in unnecessary ink usage or poor print quality.
Tips for Optimizing Ink Coverage
Choose High-Quality Inks: Invest in inks specifically designed for UV flatbed printers. These inks are formulated for quick curing and optimal adhesion to a wide range of substrates.
Test Different Substrates: Before committing to a large print job, conduct tests on small samples of the chosen substrate. This helps determine the best print settings and ink usage for that specific material.
Adjust Print Settings: Experiment with different print resolutions, speeds, and ink limits to find the optimal balance between print quality and ink usage. Higher resolutions may require more ink but can produce finer details.
Regular Printer Maintenance: Keep the printer heads and nozzles clean and aligned. Regular maintenance ensures even ink distribution and prevents clogged nozzles.
Prepare Files Properly: Use high-resolution graphic files optimized for large-format printing. This ensures the best possible print quality while minimizing ink waste.
Prime the Substrate: If necessary, use a primer to prepare the substrate surface for printing. This improves ink adhesion and coverage, especially on difficult-to-print materials.
Monitor Ink Levels: Keep track of ink levels and replace cartridges before they run dry to prevent print quality issues.
Profile Your Printer: Create or use an existing ICC profile specific to your printer and inks. This ensures color accuracy and consistent ink coverage.
Calibrate Regularly: Regularly calibrate your printer to maintain color accuracy and ink density.
Train Your Staff: Provide training to your staff on proper printer operation, ink management, and troubleshooting techniques. Knowledgeable operators can help optimize ink coverage and minimize waste.
Conclusion
Optimizing ink coverage on a UV flatbed printer requires a combination of understanding the factors that affect ink coverage and implementing practical tips to improve it. By investing in high-quality inks, testing different substrates, adjusting print settings, maintaining the printer, preparing files properly, priming the substrate if necessary, monitoring ink levels, profiling your printer, calibrating regularly, and training your staff, you can achieve vibrant, long-lasting prints with minimal ink waste. UV flatbed printing offers endless possibilities for creating stunning visual displays, and optimizing ink coverage is key to unlocking its full potential.