How to Optimize Ink Usage in UV Flatbed Printing?
How to Optimize Ink Usage in UV Flatbed Printing?
UV flatbed printing has revolutionized the way we approach digital printing, offering versatility, precision, and high-quality outputs. This technology allows for direct printing on various substrates, ranging from rigid materials like glass, metal, and plastic to flexible ones such as leather and fabric. However, with the advantages it brings, UV flatbed printing also poses unique challenges, especially when it comes to ink usage. Optimizing ink usage is crucial not only for cost-effectiveness but also for ensuring print quality and minimizing waste. In this article, we will explore practical strategies to optimize ink usage in UV flatbed printing.
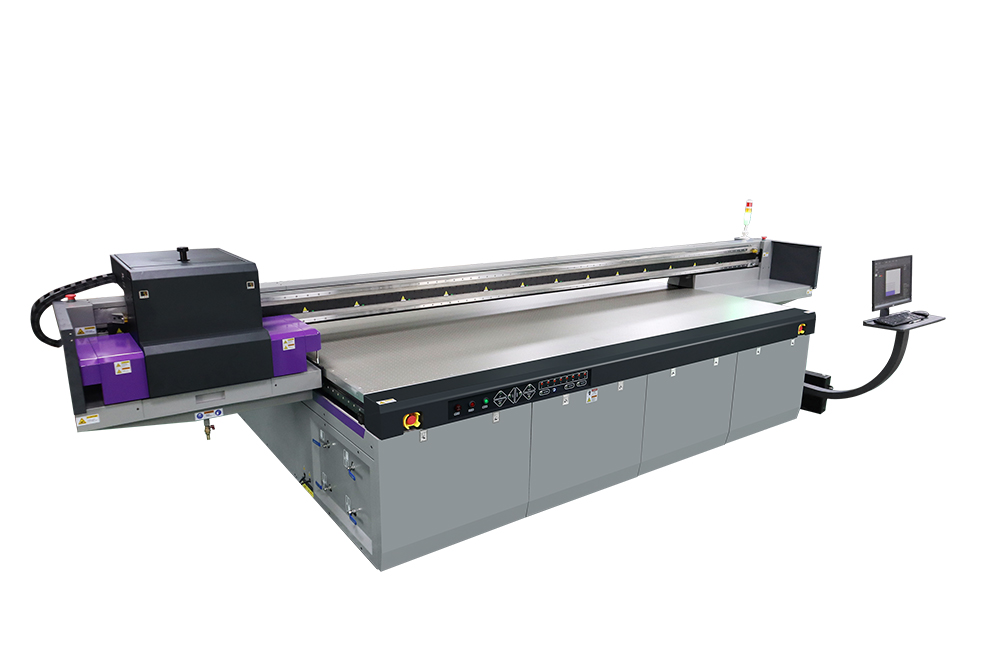
Understanding UV Flatbed Printing and Ink Consumption
UV flatbed printers utilize UV-curable inks that are instantly dried or cured by ultraviolet light after being deposited onto the substrate. This process enables fast printing speeds and immediate handling of the printed materials without the risk of smudging or smearing. However, UV inks are generally more expensive than traditional solvent or aqueous inks, making ink management a critical aspect of operating a UV flatbed printer efficiently.
Ink consumption in UV flatbed printing can vary significantly based on several factors, including the design being printed, the ink coverage required, the printer’s settings, and the substrate’s characteristics. Understanding these variables is the first step towards optimizing ink usage.
1. Design Optimization
The design plays a pivotal role in determining ink consumption. Simple designs with minimal ink coverage naturally consume less ink than complex, heavily saturated ones. Here are some design considerations to optimize ink usage:
Simplify Designs: Whenever possible, simplify the design to reduce ink coverage. Use design software to identify and eliminate unnecessary ink-heavy elements.
Utilize White Sparingly: White ink is often used in UV flatbed printing for its opacity, but it can be expensive and consume more ink than other colors. Use white ink only where necessary and consider alternatives for achieving opacity.
Color Management: Optimize color usage by selecting colors that require less ink to achieve the desired effect. Utilize spot colors instead of process colors when applicable.
2. Printer Settings and Calibration
Proper printer settings and regular calibration are essential for efficient ink usage. Here’s how to ensure your printer is set up for optimal ink consumption:
Ink Drop Size: Adjust the ink drop size according to the print job’s requirements. Smaller drops can provide finer detail but may require more ink to achieve opacity.
Print Resolution: Lowering the print resolution slightly can reduce ink consumption without significantly impacting print quality. Find the optimal resolution balance for each job.
Regular Calibration: Calibrate your printer regularly to ensure accurate ink deposition. Misaligned or improperly calibrated printers can waste ink by depositing it unevenly or in excess.
3. Substrate Selection and Preparation
The substrate’s characteristics can significantly affect ink consumption. Consider the following when selecting and preparing substrates:
Ink Absorption: Some substrates absorb more ink than others. Choose substrates with good ink adhesion properties to minimize ink waste.
Surface Preparation: Properly prepare the substrate’s surface to ensure even ink deposition. Clean, degrease, and, if necessary, apply a pretreatment to enhance ink adhesion.
Substrate Color: Dark or colored substrates may require more ink to achieve vibrant colors and opacity. Consider using lighter substrates or optimizing the design for better ink efficiency.
4. Ink Management Systems
Utilize ink management systems and features provided by the printer manufacturer to optimize ink usage:
Ink Level Monitoring: Regularly check ink levels to avoid over-inking or running the printer with low ink levels, which can affect print quality.
Ink Recovery Systems: Some UV flatbed printers offer ink recovery systems that collect and reuse excess ink. These systems can significantly reduce ink waste.
Software Features: Utilize printer software features such as ink-saving modes or variable dot technologies that adjust ink deposition based on the print job’s requirements.
5. Maintenance and Operator Training
Proper maintenance and operator training are crucial for optimizing ink usage and ensuring printer longevity:
Regular Maintenance: Follow the manufacturer’s recommended maintenance schedule to keep the printer in optimal condition. Clean print heads and replace worn parts promptly.
Operator Training: Train operators on best practices for ink usage, including design optimization, printer settings, and substrate preparation. Knowledgeable operators can make informed decisions that reduce ink waste.
Troubleshooting: Teach operators how to identify and address common issues that may lead to increased ink consumption, such as ink bleeding or poor ink adhesion.
Conclusion
Optimizing ink usage in UV flatbed printing is a multifaceted approach that involves design considerations, printer settings, substrate selection, ink management systems, and proper maintenance. By implementing these strategies, businesses can significantly reduce ink consumption, lower costs, and minimize waste while maintaining high print quality. Remember, continuous monitoring and adaptation are key to staying efficient in the ever-evolving UV flatbed printing industry. As technology advances, staying informed about new ink-saving technologies and techniques will further enhance your ability to optimize ink usage and maximize profitability.