How to Optimize Print Quality with a UV Flatbed Printer
How to Optimize Print Quality with a UV Flatbed Printer
In the realm of digital printing, UV flatbed printers have emerged as a versatile and high-performance solution for a wide array of applications, from signage and banners to fine art reproductions and industrial prototyping. Their ability to print directly onto a range of materials, including rigid substrates like wood, metal, glass, and plastics, coupled with their instant curing capabilities, makes them a sought-after choice for professionals seeking exceptional print quality and efficiency. However, achieving optimal print quality with a UV flatbed printer involves more than simply pressing the print button. This article delves into the key factors and strategies for maximizing print quality, ensuring that your output meets or exceeds expectations.
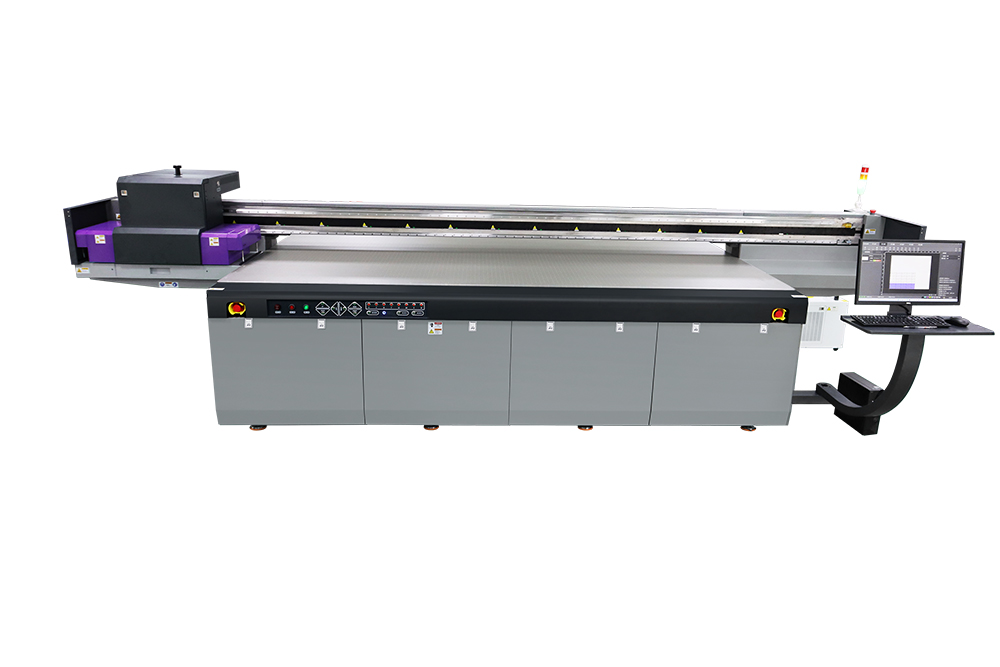
Understanding UV Flatbed Printer Basics
Before delving into optimization techniques, it’s crucial to grasp the fundamentals of UV flatbed printing. UV (Ultraviolet) flatbed printers employ UV-curable inks that, upon exposure to UV light, instantly harden or cure, allowing for immediate handling and finishing. This curing process eliminates the need for drying time, significantly enhancing productivity. The flatbed design allows for printing on three-dimensional objects and irregularly shaped surfaces, expanding the range of printable materials and applications.
Key Factors Affecting Print Quality
1. Ink Quality and Type
The quality of UV ink plays a pivotal role in determining the overall print quality. High-quality inks offer better color vibrancy, durability, and scratch resistance. Different ink types, such as hybrid, solvent-based, or eco-friendly UV inks, each have their unique characteristics and suitability for specific materials and applications. Choosing the right ink for your project is essential to achieving the desired results.
2. Printhead Technology
The printhead is the heart of any UV flatbed printer, responsible for depositing ink onto the substrate. Advanced printhead technologies, such as piezoelectric or thermal inkjet systems, offer precision and control over ink droplet size and placement, enabling finer details and higher resolution prints. Regular maintenance and calibration of the printhead are crucial to maintain optimal print quality.
3. Substrate Preparation
Proper substrate preparation is non-negotiable for achieving top-notch print quality. This includes ensuring the surface is clean, free from dust, grease, or any other contaminants that could affect ink adhesion. Depending on the material, it may also involve priming or coating the surface to enhance ink absorption and adhesion.
4. Print Resolution and DPI
Dots Per Inch (DPI) is a measure of print resolution, indicating the number of ink dots placed in a square inch of the printed image. Higher DPI values result in finer details and smoother transitions, enhancing overall print quality. However, it’s important to balance DPI with print speed and material suitability to avoid over-saturation or other issues.
5. Color Management
Accurate color reproduction is vital for achieving professional-looking prints. Implementing a robust color management system, including color profiling of both the printer and the materials being used, ensures consistent and predictable color output across different jobs and materials.
6. UV Curing Process
The UV curing process is critical to the final print quality. Insufficient curing can lead to soft or tacky ink, while over-curing can cause discoloration or material degradation. Optimizing the UV lamp intensity, curing time, and distance from the substrate ensures proper ink curing, maximizing durability and aesthetic appeal.
Optimization Strategies
1. Regular Maintenance and Calibration
Regular maintenance, including cleaning the printhead, replacing worn-out parts, and calibrating the machine, is essential for maintaining optimal print quality. A well-maintained printer is less prone to errors and inconsistencies, ensuring consistent and predictable results.
2. Material Testing
Different materials require different printing conditions and ink formulations. Conducting material tests with your UV flatbed printer allows you to identify the optimal settings for each material, including print resolution, ink type, and curing parameters. This ensures that every job is tailored to the specific needs of the material, maximizing print quality.
3. Color Profiling
Investing in color profiling software and hardware allows you to create custom profiles for your printer and materials. These profiles ensure that the colors you see on your screen are accurately reproduced on the printed material, eliminating the need for manual adjustments and enhancing color consistency across jobs.
4. Optimizing UV Curing
Fine-tuning the UV curing process can significantly impact print quality. Experiment with different UV lamp intensities, curing times, and distances from the substrate to find the optimal settings for each material. Monitoring the curing process with UV intensity meters and adjusting accordingly can help prevent under- or over-curing issues.
5. Environment Control
Maintaining a stable printing environment is crucial for consistent print quality. Factors such as temperature, humidity, and air quality can all affect ink behavior and curing efficiency. Investing in environmental control systems, such as heaters, dehumidifiers, and air filters, can help minimize these variables and ensure consistent results.
6. Software Optimization
Utilizing advanced print management software can streamline the printing process and enhance print quality. These software solutions often include features like automatic color correction, previewing capabilities, and job scheduling, allowing you to optimize each job before sending it to the printer.
7. Training and Expertise
Investing in training for your operators is a wise decision. A well-trained team understands the intricacies of UV flatbed printing and can quickly identify and resolve issues that may affect print quality. Additionally, staying up-to-date with the latest technology and industry trends can help your team make informed decisions about equipment upgrades and process improvements.
Conclusion
Achieving optimal print quality with a UV flatbed printer requires a comprehensive approach that encompasses ink quality, printhead technology, substrate preparation, color management, UV curing optimization, and environmental control. By implementing these strategies and investing in regular maintenance, material testing, and operator training, you can ensure that your UV flatbed printer consistently delivers high-quality prints that meet or exceed your customers’ expectations. As the technology continues to evolve, staying informed and adapting to new advancements will be key to maintaining a competitive edge in the ever-growing digital printing industry.