How to Optimize the Printing Process for Speed and Efficiency on a UV Flatbed Printer
How to Optimize the Printing Process for Speed and Efficiency on a UV Flatbed Printer
In the realm of digital printing, UV flatbed printers have revolutionized the way we approach wide-format printing. These versatile machines offer exceptional print quality, durability, and the ability to print on a variety of substrates. However, to fully harness their potential, it’s crucial to optimize the printing process for speed and efficiency. This comprehensive guide delves into the key strategies and practices that can help you achieve optimal performance from your UV flatbed printer, ensuring that you maximize productivity while maintaining high print quality.
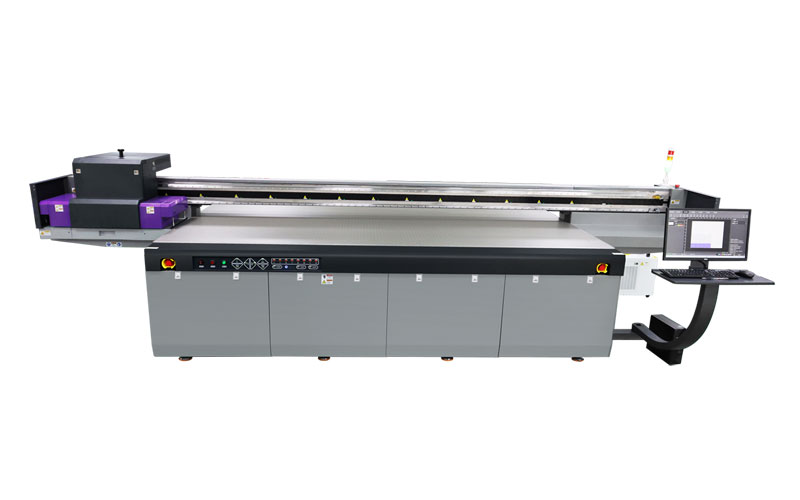
1. Understanding Your Printer’s Capabilities
Before diving into optimization techniques, it’s essential to have a thorough understanding of your UV flatbed printer’s specifications and capabilities. Familiarize yourself with its maximum print speed, resolution, supported media types, and ink characteristics. This knowledge will serve as the foundation for making informed decisions throughout the optimization process.
2. Preparing Your Files
2.1 File Resolution and Format
Resolution: Ensure your design files are set to the appropriate resolution. For most UV flatbed printers, a resolution of 300 dpi (dots per inch) is ideal for high-quality prints.
File Format: Use vector-based formats like AI or EPS for graphics that require scalability, and raster-based formats like TIFF or PSD for images with intricate details.
2.2 Color Management
Color Profile: Utilize ICC profiles specific to your printer and substrate to ensure accurate color reproduction.
Calibration: Regularly calibrate your printer and monitor to maintain color consistency.
2.3 Optimization Software
RIP Software: Invest in a good Raster Image Processor (RIP) that can efficiently handle large files, optimize print paths, and manage color accurately.
Preflighting: Use preflighting tools within your RIP or design software to check for errors, such as missing fonts, low-resolution images, or overprints, before sending the job to print.
3. Media Handling
3.1 Substrate Selection
Compatibility: Choose substrates that are compatible with your printer’s UV inks and adhere to the manufacturer’s guidelines.
Preparation: Ensure substrates are clean, dry, and free of dust or debris that could affect print quality.
3.2 Media Loading
Alignment: Properly align and secure the media on the print bed to prevent shifting during printing.
Thickness: Adjust the printer’s settings according to the thickness of the substrate to maintain optimal print head clearance and avoid damage.
4. Printer Settings and Configuration
4.1 Print Modes
Quality vs. Speed: Balance print quality and speed by selecting the appropriate print mode. For example, use a higher-quality mode for detailed graphics and a faster mode for large areas of solid color.
Pass Count: Adjust the number of print passes to optimize ink coverage and cure time. More passes can enhance color saturation but will slow down the process.
4.2 Ink Usage
Ink Levels: Regularly monitor and maintain ink levels to avoid interruptions during printing.
Ink Saving Features: Utilize ink-saving features, such as variable dot sizes or ink optimization algorithms, to reduce ink consumption without compromising quality.
4.3 Curing Settings
UV Lamp Power: Adjust the power of the UV lamps to ensure proper ink curing. Over-curing can lead to cracking or discoloration, while under-curing can result in poor adhesion.
Curing Speed: Optimize the speed of the curing process to match the ink’s curing requirements and the substrate’s characteristics.
5. Workflow Efficiency
5.1 Job Scheduling
Prioritization: Prioritize jobs based on urgency and complexity to efficiently manage workflow.
Batch Processing: Group similar jobs together to minimize setup time and maximize printer utilization.
5.2 Automation
Automated Feeding: If your printer supports automated media feeding, utilize this feature to reduce manual handling and increase efficiency.
Software Integration: Integrate your printer with workflow management software to streamline job submission, tracking, and reporting.
5.3 Maintenance
Regular Cleaning: Perform regular maintenance tasks, such as cleaning the print heads, wiping down the print bed, and replacing filters, to ensure consistent print quality and prevent downtime.
Preventive Maintenance: Establish a preventive maintenance schedule to address potential issues before they arise, including checking for worn parts or updating software and firmware.
6. Operator Training
6.1 Skill Development
Training Programs: Implement comprehensive training programs to ensure operators are proficient in using the printer and its software.
Troubleshooting: Equip operators with the knowledge to diagnose and resolve common issues quickly, minimizing downtime.
6.2 Continuous Learning
Stay Updated: Encourage operators to stay informed about new printing techniques, software updates, and industry trends.
Feedback Loop: Establish a feedback loop to collect insights from operators and continuously improve processes.
7. Environmental Considerations
7.1 Ink Disposal
Eco-Friendly Inks: Choose inks that are environmentally friendly and comply with local regulations for disposal.
Recycling: Implement a recycling program for used substrates, ink cartridges, and other consumables.
7.2 Energy Efficiency
Power Management: Use power-saving modes when the printer is not in use and optimize curing settings to reduce energy consumption.
Ventilation: Ensure proper ventilation in the printing area to manage fumes and maintain a safe working environment.
8. Quality Control
8.1 Inspection
Visual Inspection: Regularly inspect prints for defects, such as banding, misregistration, or ink bleeding.
Measurement Tools: Use tools like densitometers or spectrophotometers to measure color accuracy and consistency.
8.2 Feedback and Adjustment
Continuous Improvement: Analyze print results and adjust settings as needed to maintain high quality.
Customer Feedback: Gather feedback from customers to understand their expectations and make adjustments to meet their needs.
Conclusion
Optimizing the printing process on a UV flatbed printer requires a holistic approach that encompasses file preparation, media handling, printer configuration, workflow efficiency, operator training, environmental considerations, and quality control. By implementing these strategies, you can significantly enhance the speed and efficiency of your printing operations while maintaining exceptional print quality. Remember, the key to successful optimization is continuous learning and adaptation, allowing you to stay ahead of industry trends and meet the evolving needs of your customers. With a well-optimized UV flatbed printer, you can unlock new levels of productivity and creativity, driving your business toward success.