How to Optimize UV Flatbed Printer Settings for Best Results
UV flatbed printers have revolutionized the printing industry by offering versatile, high-quality prints on a wide range of substrates. From rigid materials like glass and metal to flexible ones like vinyl and fabric, these printers can handle it all. However, to achieve the best results, it’s crucial to optimize the printer settings. This comprehensive guide will walk you through the essential steps and considerations for fine-tuning your UV flatbed printer’s settings to ensure top-notch print quality, efficiency, and longevity of your prints.
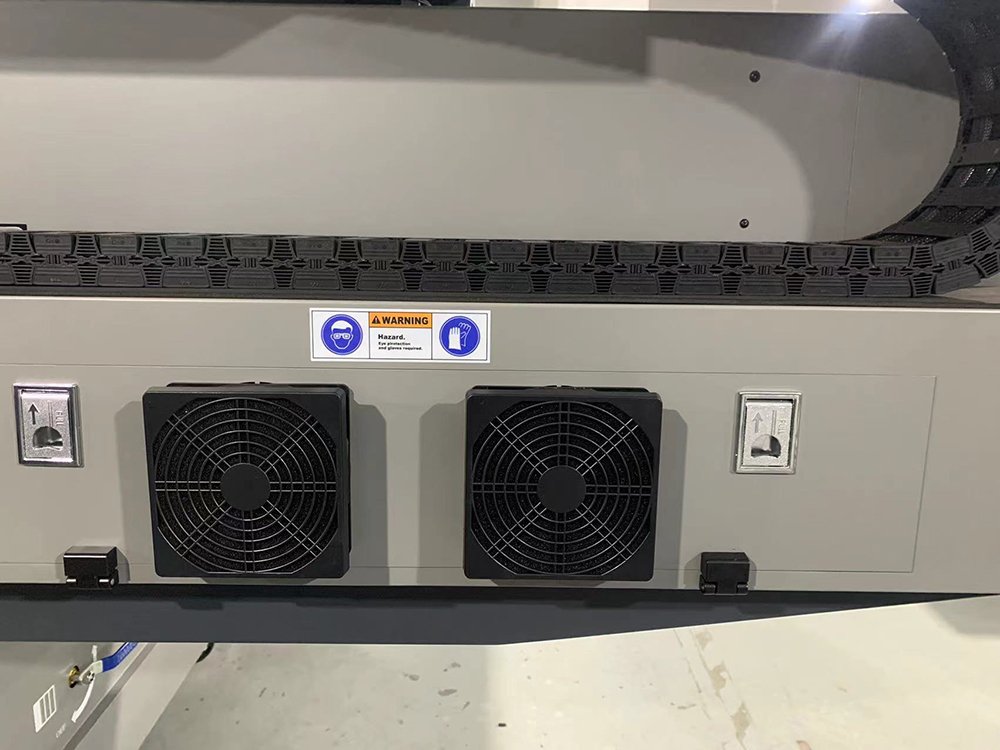
Understanding the Basics of UV Flatbed Printing
Before diving into the settings, it’s important to grasp the fundamentals of UV flatbed printing. These printers use ultraviolet light to cure the ink instantly after it’s applied to the substrate. This process offers several advantages, including faster printing speeds, enhanced durability, and the ability to print on a variety of materials.
The quality of the print is influenced by several factors, including ink type, printer resolution, substrate material, and printer settings. Optimizing these elements will help you achieve the desired outcome, whether you’re printing intricate graphics, text, or images.
Step-by-Step Guide to Optimizing Printer Settings
1. Choosing the Right Ink and Substrate
Ink Selection: UV inks are available in various types, each suited for specific applications. For instance, some inks are better for outdoor use due to their resistance to fading and weathering, while others might be more suitable for indoor displays because of their vibrant colors. Consult your ink supplier to choose the best ink for your project.
Substrate Compatibility: Not all substrates are created equal. Different materials absorb ink differently, which can affect the final appearance and durability of the print. Always test print on the actual substrate you plan to use to ensure compatibility and desired results.
2. Adjusting Printer Resolution
DPI (Dots Per Inch): The resolution of your print is measured in DPI. Higher DPI settings result in finer details and sharper images but may also increase print time and ink usage. For most applications, a resolution of 300-600 DPI is ideal. For very high-detail work, such as fine art reproductions, you might opt for even higher resolutions.
Test Prints: Perform test prints at different resolutions to find the optimal balance between quality and efficiency for your specific project.
3. Calibrating Color Settings
Color Profiles: Use ICC (International Color Consortium) profiles specific to your printer, ink, and substrate combination. These profiles help ensure accurate color reproduction.
Calibration: Regularly calibrate your printer to maintain color consistency. This process involves adjusting the printer’s color output to match a standard set of colors.
Color Matching: If you’re working with specific brand colors or need exact color matches, use a spectrophotometer to measure and adjust the colors accurately.
4. Setting the Right Print Speed
Balancing Speed and Quality: Faster print speeds can sometimes compromise print quality. Experiment with different speed settings to find the sweet spot that maintains quality without excessively slowing down production.
Curing Time: Keep in mind that faster print speeds might require adjustments to the UV curing lamp’s intensity or dwell time to ensure complete curing of the ink.
5. Adjusting UV Lamp Settings
Intensity: The intensity of the UV lamps affects how well the ink cures. Too low, and the ink might not fully cure; too high, and it could cause overheating or substrate damage. Follow the manufacturer’s guidelines for your specific printer model and substrate.
Dwell Time: This refers to the amount of time the substrate spends under the UV lamps. Adjusting the dwell time can help ensure proper curing without slowing down production too much.
6. Optimizing Print Head Height
Head Gap: The distance between the print heads and the substrate (head gap) can impact print quality. A smaller gap generally results in better ink deposition but can also increase the risk of head crashes. A larger gap might be necessary for uneven or thick substrates.
Auto Adjustment: Many modern UV flatbed printers come with automatic head height adjustment features. Utilize these to fine-tune the gap based on the substrate being used.
7. Managing Ink Flow and Drop Size
Ink Flow Rate: Adjusting the ink flow rate can help control the amount of ink deposited on the substrate. Too much ink can lead to bleeding or smudging, while too little can result in patchy or faded prints.
Drop Size: The size of the ink droplets can also be adjusted. Smaller droplets provide finer details, while larger ones cover more area quickly but might sacrifice some detail.
8. Controlling Humidity and Temperature
Environmental Conditions: Humidity and temperature can affect ink viscosity and substrate behavior. Maintain a controlled environment with recommended humidity and temperature levels to ensure consistent print quality.
Heating and Cooling Systems: Use the printer’s built-in heating and cooling systems to regulate the temperature of the print heads and substrate during printing.
9. Utilizing Printer Software Features
RIP Software: Raster Image Processor (RIP) software is crucial for managing large files and optimizing them for printing. Ensure your RIP software is up-to-date and configured correctly for your printer.
Print Queues: Efficiently manage your print queue to avoid bottlenecks and ensure smooth workflow. Use features like print preview and job prioritization to streamline production.
Maintenance Routines: Regularly run maintenance routines provided by the printer manufacturer. This includes cleaning print heads, checking ink levels, and inspecting the UV lamps.
10. Post-Processing Considerations
Curing After Print: Depending on the ink and substrate, additional curing steps might be required after printing to ensure complete ink polymerization.
Finishing Touches: Consider post-processing options like laminating, cutting, or mounting to enhance the durability and appearance of your prints.
Optimizing UV flatbed printer settings is a multifaceted process that involves understanding your printer’s capabilities, choosing the right materials, and fine-tuning a variety of settings. By following the steps outlined in this guide, you can achieve exceptional print quality, efficiency, and durability. Remember that the key to success is continuous testing and adjustment, as well as staying updated with the latest advancements in UV printing technology. With patience and practice, you’ll be able to master the art of UV flatbed printing and produce outstanding results every time.