How to Optimize White Ink Usage on a UV Flatbed Printer
How to Optimize White Ink Usage on a UV Flatbed Printer
In the realm of digital printing, UV flatbed printers have revolutionized the way we approach print production, especially when it comes to printing on a wide variety of substrates, including those that are transparent, dark, or textured. One of the key advantages of these printers is their ability to utilize white ink, which serves multiple purposes such as enhancing color vibrancy on dark materials, acting as a base layer for vibrant color prints, and even creating stunning spot effects. However, white ink can be costly and its management requires a keen understanding of printer settings, ink chemistry, and substrate characteristics. This article delves into the intricacies of optimizing white ink usage on a UV flatbed printer to maximize efficiency, reduce costs, and ensure exceptional print quality.
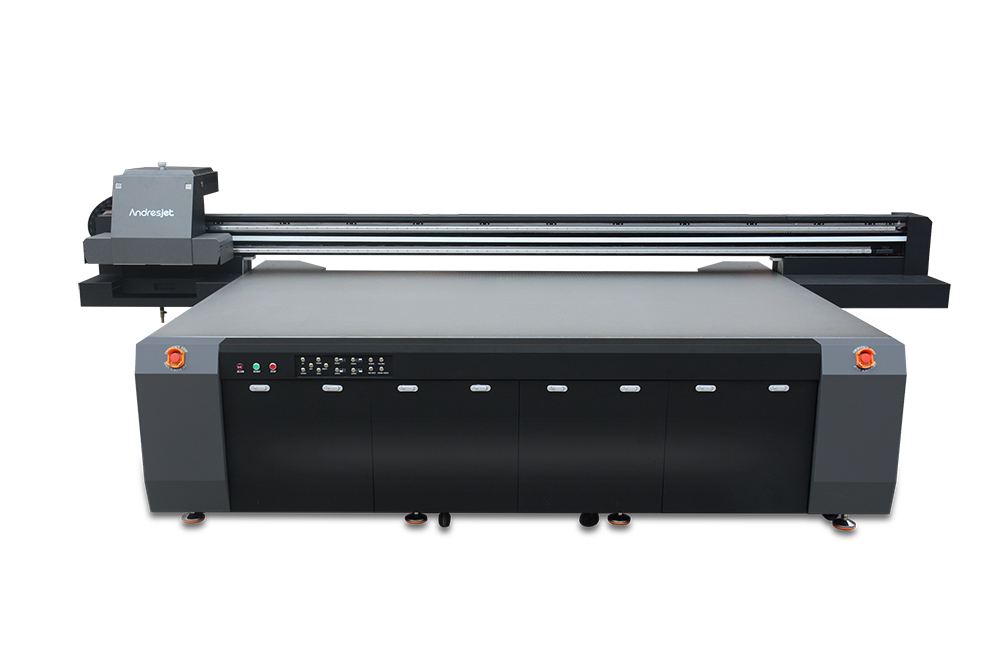
Understanding White Ink in UV Printing
White ink in UV flatbed printers is typically composed of titanium dioxide particles suspended in a UV-curable resin. When exposed to UV light, the resin cures, binding the titanium dioxide to the substrate, creating a durable and opaque white layer. Unlike traditional inks, which rely on absorption into the material, UV inks form a thin layer on the surface, allowing for precise control over color and opacity.
The uniqueness of white ink lies in its ability to serve as both a base and a highlight color. It can be used to prime dark or transparent substrates, ensuring that subsequent colors appear true and vibrant. Additionally, white ink can be employed for creative effects, such as simulating textures, adding depth, or creating highlights that catch the light.
Factors Affecting White Ink Usage
Optimizing white ink usage involves considering several variables, each of which can significantly impact print quality, ink consumption, and overall efficiency.
1. Substrate Characteristics
Different substrates require varying amounts of white ink to achieve the desired opacity. Darker or more absorbent materials will necessitate thicker layers of white ink, while lighter or non-absorbent substrates may require less. Understanding the porosity, color, and texture of the substrate is crucial for determining the appropriate ink application settings.
2. Printer Settings
The printer’s configuration, including ink drop size, print speed, and curing settings, plays a vital role in white ink utilization. Adjusting these parameters can help achieve the right balance between ink coverage and efficiency. For instance, smaller drop sizes can result in smoother gradients and finer details but may require more layers to achieve full opacity.
3. Ink Chemistry
The viscosity and pigment concentration of the white ink also influence its performance. Inks with higher pigment loads are more opaque but may require more energy to cure. Conversely, thinner inks may spread more easily but could result in less opaque prints. Choosing the right ink formulation for the job is essential.
4. Design Considerations
The design itself can dictate how much white ink is used. Designs with large areas of solid white will consume more ink than those with sparse or gradient white elements. Optimizing the design to minimize unnecessary white areas or utilizing design techniques that rely on color combinations to simulate white can reduce ink usage.
Strategies for Optimizing White Ink Usage
1. Conduct Substrate Tests
Before starting a large print job, it’s advisable to conduct tests on the chosen substrate. This involves printing sample swatches with varying layers of white ink to determine the minimum number of passes required to achieve the desired opacity. This step not only helps in conserving ink but also ensures consistent print quality across the entire job.
2. Adjust Printer Settings
Fine-tuning the printer settings can yield significant savings in white ink consumption. Reducing the print speed can allow for better ink distribution and absorption, potentially reducing the need for additional layers. Adjusting the drop size and ink flow rate can also optimize coverage without wasting. ink
3. Use a Base Layer Strategy
For jobs that require extensive white ink coverage, consider using a base layer of white ink applied uniformly across the entire substrate. This can be followed by targeted applications of white ink for highlights or details. This two-step process can reduce overall ink usage by ensuring that only the necessary areas receive multiple layers of ink.
4. Optimize Design Files
Designers can play a crucial role in optimizing white ink usage. By minimizing large solid white areas and using color combinations to create the illusion of white, designs can be made more ink-efficient. Additionally, ensuring that design files are properly calibrated for the printer’s color profile can prevent over-inking and waste.
5. Implement Ink-Saving Features
Many modern UV flatbed printers come equipped with features designed to minimize ink usage. These may include ink-saving modes, variable dot sizes, and advanced curing systems. Utilizing these features can lead to substantial reductions in ink consumption without compromising print quality.
6. Regular Maintenance and Calibration
Keeping the printer in optimal condition through regular maintenance and calibration is essential for efficient ink usage. Clogged nozzles, misaligned print heads, and incorrect curing settings can all lead to increased ink consumption and poor print quality. Regularly cleaning the printer, checking for nozzle clogs, and calibrating the print heads can help maintain consistent ink flow and accurate print placement.
The Role of Software in White Ink Optimization
Advancements in print management software have made it easier to optimize white ink usage. These software solutions often include features such as ink estimation calculators, which provide real-time estimates of ink consumption based on the design file and printer settings. They may also offer automated ink-saving options, such as adjusting the ink density in non-critical areas or optimizing the print path to reduce overlap and waste.
Furthermore, some software allows for the creation of custom ink profiles, enabling printers to tailor the ink application to specific substrates and job requirements. This level of customization can result in significant ink savings and improved print quality.
Environmental and Cost Considerations
Optimizing white ink usage is not just about reducing costs; it also has environmental benefits. UV inks are generally more environmentally friendly than traditional solvent-based inks, as they do not emit harmful volatile organic compounds (VOCs). However, minimizing ink waste through efficient usage further reduces the environmental footprint of the printing process.
From a cost perspective, optimizing white ink usage can lead to significant savings. White ink is often one of the most expensive components in UV printing due to its high pigment content and specialized formulation. By reducing unnecessary ink consumption, printers can lower their operational costs and pass those savings on to their customers.
Optimizing white ink usage on a UV flatbed printer requires a comprehensive understanding of the printing process, from substrate selection to printer configuration and design optimization. By taking a holistic approach that incorporates substrate testing, printer adjustments, design efficiency, and the use of advanced software, printers can achieve exceptional print quality while minimizing ink consumption. This not only reduces costs and environmental impact but also enhances the overall efficiency and profitability of the printing operation.
In the ever-evolving world of digital printing, staying ahead requires a commitment to continuous learning and adaptation. By embracing new technologies and best practices for white ink optimization, printers can unlock new levels of creativity, efficiency, and sustainability in their work.