How to Optimize Your UV Flatbed Printer for Maximum Productivity
How to Optimize Your UV Flatbed Printer for Maximum Productivity
In today’s fast-paced printing industry, achieving maximum productivity from your UV flatbed printer is crucial for staying competitive. UV flatbed printers, known for their versatility and ability to print on a wide range of materials, offer businesses a powerful tool for creating high-quality prints quickly and efficiently. However, to fully harness their potential, it’s essential to optimize your printer’s settings, workflow, and maintenance routines. This article will guide you through the key steps to maximize the productivity of your UV flatbed printer.
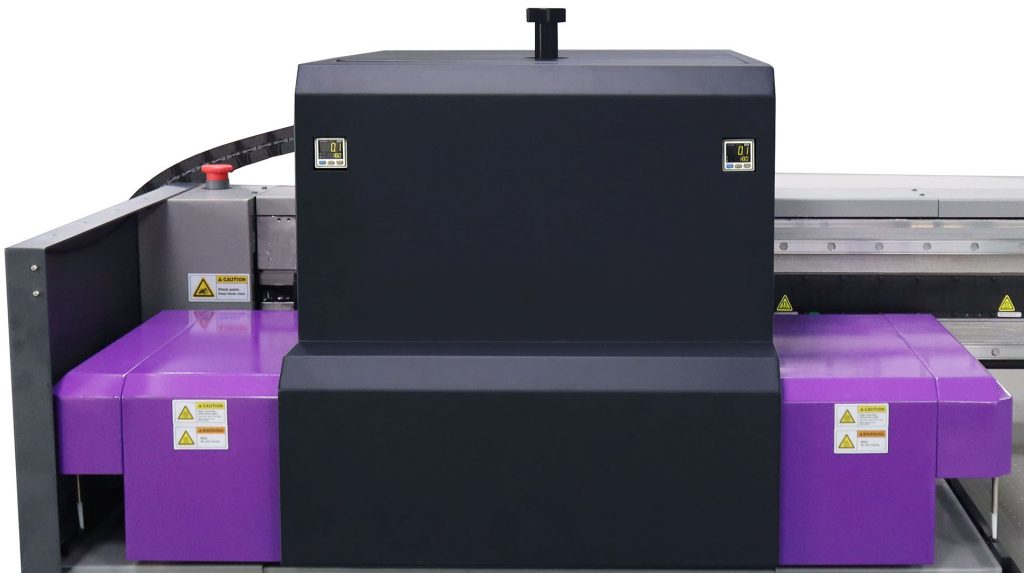
1. Understanding Your Printer’s Capabilities
Before diving into optimization, it’s vital to have a thorough understanding of your UV flatbed printer’s capabilities. This includes knowing its maximum print size, resolution, supported media types, and ink system. Familiarize yourself with the printer’s user manual and any online resources provided by the manufacturer. Understanding the technical specifications will help you make informed decisions about job setup, media selection, and print quality.
2. Choosing the Right Media and Ink
Selecting the appropriate media and ink is critical for achieving optimal print results and maximizing productivity. UV flatbed printers can handle a variety of materials, including rigid substrates like glass, metal, and plastic, as well as flexible materials such as vinyl and fabric. When choosing media, consider factors such as durability, adhesion properties, and the intended use of the printed product.
Similarly, ink selection plays a significant role in print quality and production efficiency. UV-curable inks are designed to adhere to a wide range of substrates and offer excellent color saturation and durability. However, different ink formulations may be better suited for specific applications. For instance, inks with higher pigment loads might be ideal for outdoor graphics that require long-term fade resistance, while inks with faster curing times could be more suitable for high-volume production runs.
3. Optimizing Print Settings
Adjusting your printer’s settings to match the specific requirements of each job is crucial for maximizing productivity. Here are some key settings to consider:
Resolution: While higher resolutions generally produce sharper images, they also slow down the printing process and consume more ink. For most applications, a balance between resolution and production speed is necessary. Assess the resolution needs based on the viewing distance and purpose of the print.
Ink Coverage: Adjusting the ink coverage settings can help control ink usage and drying times. For example, reducing ink coverage in non-critical areas can speed up printing and lower ink costs without compromising overall print quality.
Curing Parameters: UV flatbed printers use UV light to cure the ink instantly. Proper curing is essential for ensuring durability and adhesion. Experiment with curing times and intensities to find the optimal settings for your specific media and ink combination.
Color Management: Accurate color reproduction is crucial for maintaining print quality. Calibrate your printer regularly and use ICC profiles tailored to your media and ink to ensure consistent color output.
4. Efficient Job Setup and Workflow
Streamlining your job setup and workflow can significantly enhance productivity. Here are some strategies to consider:
Pre-Processing Images: Before sending files to print, ensure that images are properly pre-processed. This includes adjusting resolution, color correction, and ensuring that file formats are compatible with your printer’s RIP (Raster Image Processor). Pre-processing can help avoid printing errors and reduce the need for reprints.
Nesting Jobs: If possible, nest multiple jobs on a single sheet to minimize media waste and reduce setup time. This is particularly useful for smaller prints or when working with expensive materials.
Automated Feeding and Handling: Invest in automated feeding and handling systems if your volume justifies the cost. These systems can load, position, and unload media automatically, significantly reducing manual intervention and increasing throughput.
Queue Management: Use your printer’s software to manage the print queue efficiently. Prioritize jobs based on urgency and material availability. Make sure the printer is always loaded with the next job to minimize downtime.
5. Regular Maintenance and Cleaning
Maintaining your UV flatbed printer is essential for sustained productivity and print quality. Regular cleaning and maintenance tasks include:
Daily Cleaning: At the end of each day, clean the print head, platen, and any other exposed parts with a soft, lint-free cloth and the appropriate cleaning solution. Remove any ink residue or debris that may have accumulated during printing.
Weekly Maintenance: Once a week, perform a more thorough cleaning, including the ink system and UV lamps. Check for any signs of wear or damage and replace worn parts promptly.
Ink System Maintenance: Regularly check ink levels and replace empty cartridges or tanks. Keep the ink system clean and free from contaminants to avoid print defects.
Software Updates: Keep your printer’s software and drivers up to date. Manufacturers often release updates that improve performance, fix bugs, and add new features.
6. Training and Skill Development
Your team’s expertise plays a crucial role in maximizing printer productivity. Regular training sessions can help your staff stay up to date with the latest printing techniques, software updates, and maintenance procedures. Consider the following:
In-House Training: Conduct regular training sessions for your team, focusing on specific aspects of the printing process, such as color management, job setup, and troubleshooting.
Manufacturer Training: Take advantage of training programs offered by your printer’s manufacturer. These programs often provide comprehensive training on printer operation, maintenance, and advanced features.
Online Resources: Encourage your team to explore online resources, such as forums, tutorials, and webinars, to stay informed about industry trends and best practices.
7. Monitoring and Analyzing Productivity
To continuously improve productivity, it’s essential to monitor and analyze your printer’s performance. Keep track of key metrics such as print speed, ink usage, media costs, and downtime. Use this data to identify bottlenecks and areas for improvement.
Print Logs: Maintain detailed print logs to track the time taken for each job, ink usage, and any issues encountered. This information can help you identify trends and optimize your workflow accordingly.
Downtime Analysis: Analyze downtime to identify the causes of delays and develop strategies to minimize them. For example, if you frequently experience delays due to ink changes, consider adopting a more efficient ink management system.
Cost Analysis: Regularly review your printing costs, including ink, media, and maintenance expenses. This will help you make informed decisions about material selection and print settings to optimize cost-efficiency.
Conclusion
Optimizing your UV flatbed printer for maximum productivity involves a combination of understanding your printer’s capabilities, choosing the right media and ink, adjusting print settings, streamlining workflow, maintaining the printer, developing your team’s skills, and monitoring performance. By implementing these strategies, you can enhance print quality, reduce costs, and increase throughput, ultimately boosting your competitiveness in the printing industry. Remember, achieving maximum productivity is an ongoing process that requires continuous learning, adaptation, and improvement. With dedication and the right approach, you can unlock the full potential of your UV flatbed printer and drive your business forward.