How to Prevent Banding in UV Flatbed Printing?
How to Prevent Banding in UV Flatbed Printing?
UV flatbed printing has revolutionized the way we produce high-quality prints on various materials. Its ability to print directly onto substrates like glass, plastic, wood, and metal has made it a popular choice for businesses seeking versatile and durable printing solutions. However, like any printing technology, UV flatbed printing is not without its challenges. One of the most common issues faced by printers is banding, which can significantly affect the overall quality of the print.
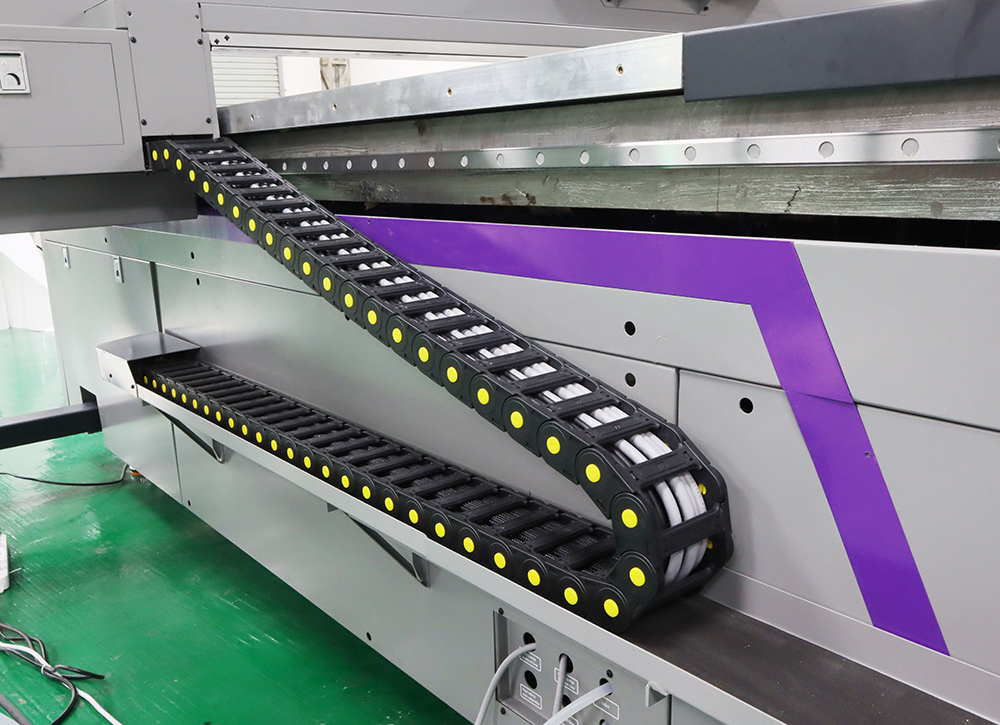
Banding, also known as striping or banding artifacts, refers to visible horizontal or vertical lines that appear on the printed surface. These lines can be caused by a variety of factors, including inkjet nozzle misalignment, ink drying issues, mechanical problems, and software settings. Banding can detract from the visual appeal of the print and, in some cases, even compromise its structural integrity. Fortunately, there are several strategies that can be employed to prevent or minimize banding in UV flatbed printing.
1. Understand the Causes of Banding
Before delving into the solutions, it is essential to understand the root causes of banding. This will enable you to identify the specific factors contributing to banding in your prints and address them accordingly. Common causes include:
Inkjet Nozzle Misalignment: If the nozzles in the print head are not aligned correctly, they can deposit ink unevenly, leading to visible banding.
Ink Drying Issues: UV inks need to be cured immediately after deposition to prevent smearing or bleeding. If the UV lamps are not functioning properly or the ink is not drying uniformly, it can result in banding.
Mechanical Problems: Issues with the printer’s mechanics, such as uneven platen movement or worn-out bearings, can also cause banding.
Software Settings: Incorrect or suboptimal printer settings, such as resolution, print speed, or ink density, can contribute to banding.
2. Calibrate and Maintain Your Printer
Regular calibration and maintenance are crucial for preventing banding and ensuring consistent print quality. Here are some key steps:
Print Head Alignment: Use the printer’s built-in alignment tools to ensure that the nozzles are correctly aligned. If necessary, perform manual adjustments or contact the printer manufacturer for assistance.
UV Lamp Inspection: Check the UV lamps regularly to ensure they are functioning properly. Replace any lamps that are not curing the ink evenly or have reached the end of their lifespan.
Mechanical Inspection: Inspect the printer’s mechanics for any signs of wear or damage. Replace worn-out parts and ensure that the platen is moving smoothly and evenly.
Clean the Print Head: Regularly clean the print head to remove any ink residue or debris that could interfere with ink deposition.
3. Optimize Your Print Settings
Adjusting your print settings can often help reduce or eliminate banding. Experiment with the following settings:
Resolution: Increase the print resolution to improve ink deposition accuracy. Higher resolutions will result in smaller ink droplets, which can help reduce banding.
Print Speed: Slowing down the print speed can allow for better ink deposition and curing, reducing the likelihood of banding.
Ink Density: Adjust the ink density settings to ensure that the ink is being deposited evenly across the print surface. Over-saturation or under-saturation can both contribute to banding.
Pass Count: Increasing the number of passes the print head makes over the substrate can help distribute the ink more evenly, reducing banding.
4. Use High-Quality Materials
The quality of your substrates and inks can also play a role in banding. Invest in high-quality materials to minimize the risk of banding:
Substrates: Use substrates that are compatible with UV inks and have a smooth, even surface. Rough or porous surfaces can make it more difficult to achieve uniform ink deposition.
Inks: Choose UV inks that are specifically designed for flatbed printing and have a proven track record of minimal banding. Some ink manufacturers offer inks with enhanced flow properties or special additives to reduce banding.
5. Control the Environment
Environmental factors can also impact the likelihood of banding. Consider the following:
Temperature and Humidity: Maintain a consistent temperature and humidity level in your printing environment. Changes in temperature or humidity can affect ink viscosity and curing, potentially leading to banding.
Dust and Debris: Keep your printing area clean and dust-free. Dust particles can interfere with ink deposition and cause banding.
6. Post-Print Inspection and Adjustment
Finally, always perform a thorough post-print inspection to identify any banding issues. If banding is detected, use the following steps to adjust your process:
Analyze the Print: Closely inspect the print to determine the cause of the banding. Look for patterns or consistency in the banding to help identify the root cause.
Make Incremental Adjustments: Based on your analysis, make incremental adjustments to your print settings, materials, or printer maintenance. It is often helpful to keep a record of your changes and their impact on banding.
Consult with Experts: If banding persists, consider consulting with printer manufacturers, ink suppliers, or printing experts. They can provide additional guidance and support in diagnosing and addressing banding issues.
In conclusion, banding can be a frustrating issue in UV flatbed printing, but it is not an insurmountable problem. By understanding the causes of banding, calibrating and maintaining your printer, optimizing your print settings, using high-quality materials, controlling the environment, and performing thorough post-print inspections, you can significantly reduce or eliminate banding in your UV flatbed prints. With these strategies in place, you can ensure that your prints are of the highest quality, meeting the demands of your customers and exceeding their expectations.