How to Solve Common Printing Issues with a UV Flatbed Printer
UV flatbed printers have revolutionized the printing industry, offering versatile and high-quality printing on a wide range of materials. From rigid substrates like glass, metal, and ceramics to flexible materials such as vinyl and fabric, UV flatbed printers have become indispensable tools for businesses seeking to produce stunning visuals and durable prints. However, like any sophisticated machinery, UV flatbed printers can encounter various issues that may disrupt the printing process. This article aims to provide comprehensive solutions to some of the most common problems you might face with a UV flatbed printer, ensuring smooth and efficient operation.
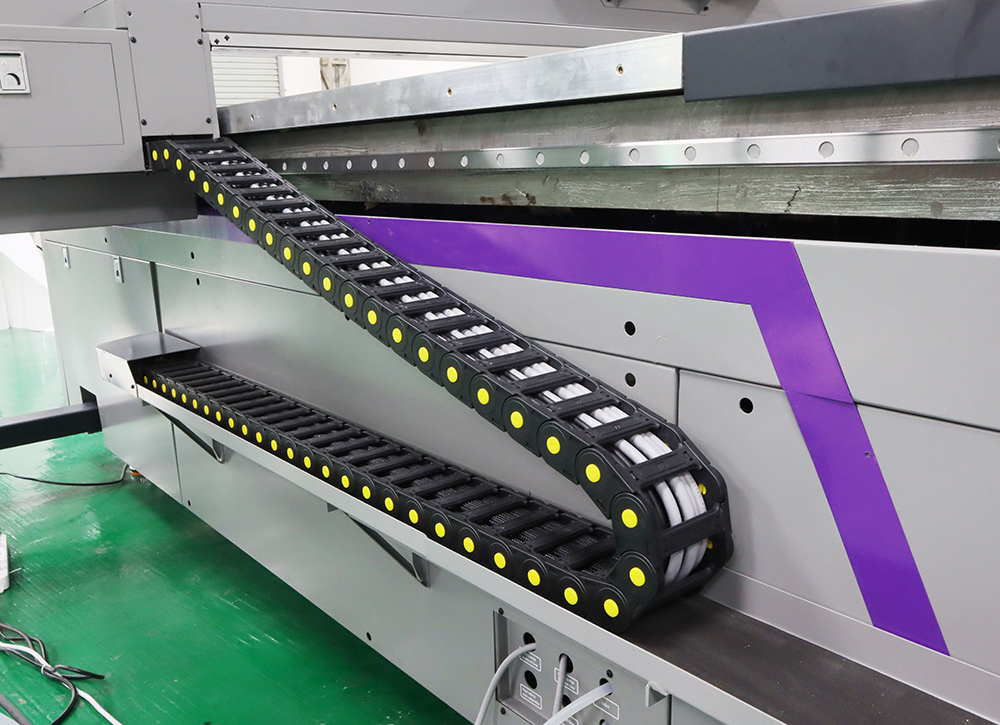
1. Nozzle Clogging
Nozzle clogging is one of the most frequent issues encountered in UV flatbed printing. It occurs when ink dries or accumulates in the nozzles, preventing proper ink flow and resulting in uneven or missing print areas.
Solutions:
Regular Cleaning: Incorporate a routine cleaning schedule using the printer’s built-in cleaning functions. Most UV flatbed printers come with automatic cleaning cycles that can be run periodically to prevent clogs.
Manual Cleaning: For stubborn clogs, manual intervention may be required. Use a cleaning solution recommended by the printer manufacturer and a soft, lint-free cloth to gently clean the nozzle plate. Ensure the printer is turned off and unplugged before performing manual cleaning.
Nozzle Check Pattern: Run a nozzle check pattern to identify which nozzles are clogged. This feature is available in most printer settings and helps pinpoint the affected areas for targeted cleaning.
Humidity Control: Maintain an optimal printing environment with controlled humidity levels. Low humidity can cause ink to dry quickly, leading to clogs. Invest in a humidifier if necessary.
2. Ink Smearing or Bleeding
Ink smearing or bleeding can ruin an otherwise perfect print, especially when working with detailed designs or multiple colors.
Solutions:
Proper Curing: Ensure that the UV light source is functioning correctly and that prints are being cured adequately. Insufficient curing can cause ink to remain tacky, leading to smearing.
Adjust Print Settings: Increase the distance between the print head and the substrate if possible. This can help reduce the likelihood of ink being spread or smudged during the printing process.
Use Quality Ink: Invest in high-quality UV-curable inks that are specifically designed for your printer model. Inferior inks may not cure properly and are more prone to smearing.
Substrate Preparation: Make sure the substrate is clean, dry, and free of any contaminants that could affect ink adhesion. Applying a primer if recommended by the printer or ink manufacturer can also improve ink adhesion.
3. Banding or Striping
Banding or striping refers to visible lines or gaps in the print, often caused by misalignments or inconsistencies in the ink deposition process.
Solutions:
Calibrate the Printer: Regularly calibrate the printer to ensure precise alignment of the print heads. Most UV flatbed printers have a calibration feature in their settings menu.
Check Print Head Alignment: Manually inspect and adjust the print head alignment if necessary. Misaligned print heads can cause banding issues.
Update Firmware: Ensure that the printer’s firmware is up to date. Manufacturers often release firmware updates to address known issues and improve printer performance.
Reduce Print Speed: Slowing down the print speed can help improve ink deposition accuracy, reducing the likelihood of banding.
4. Color Inconsistency
Color inconsistency can be a frustrating issue, especially when producing prints that require precise color matching.
Solutions:
Profile Calibration: Use color profiling tools to calibrate the printer and ensure accurate color reproduction. This involves creating and printing color charts, which are then measured with a spectrophotometer to create a custom ICC profile.
Ink Levels: Check ink levels regularly and replace cartridges as needed. Low ink levels can affect color saturation and consistency.
Consistent Printing Environment: Maintain a consistent printing environment in terms of temperature and humidity. Fluctuations in these factors can affect ink behavior and color output.
Print Head Maintenance: Perform regular maintenance on the print heads to prevent clogs and ensure even ink flow, which is crucial for consistent color output.
5. Adhesion Problems
Poor ink adhesion can result in prints that easily scratch or peel off the substrate.
Solutions:
Substrate Compatibility: Ensure that the substrate you are printing on is compatible with UV-curable inks. Some materials may require special surface treatments or primers to improve ink adhesion.
Curing Parameters: Adjust the curing parameters, such as the intensity and duration of the UV light, to ensure proper ink curing. Overcuring can cause the ink to become brittle, while undercuring can result in poor adhesion.
Layer Thickness: Control the layer thickness of the ink during printing. Thicker layers may require longer curing times to achieve proper adhesion.
Post-Processing: Apply a clear coat or laminate if necessary to protect the print and improve its durability and adhesion to the substrate.
6. Software Issues
Software-related issues can cause a range of problems, from print jobs not starting to incorrect print outputs.
Solutions:
Update Software: Ensure that the printer driver and any associated software are up to date. Outdated software can cause compatibility issues and other problems.
Check File Formats: Verify that the file formats you are printing from are supported by the printer. Convert files to a compatible format if necessary.
Connection Stability: Ensure a stable connection between the computer and the printer. Use a reliable USB cable or network connection to avoid interruptions during printing.
Troubleshoot Software: Use the printer’s troubleshooting tools or consult the user manual for software-specific issues. If problems persist, contact the printer manufacturer’s technical support for assistance.
While UV flatbed printers offer numerous advantages in terms of versatility and print quality, they are not immune to issues that can disrupt the printing process. By following the solutions outlined in this article, you can address common problems such as nozzle clogging, ink smearing, banding, color inconsistency, adhesion problems, and software issues. Regular maintenance, proper printing environment control, and the use of high-quality materials are key to ensuring smooth and efficient operation of your UV flatbed printer. With these tips, you can minimize downtime and produce high-quality prints consistently.