How to Solve Common Problems with UV Flatbed Printers
UV flatbed printers have revolutionized the printing industry by offering versatile, high-quality prints on a wide range of materials. These printers utilize ultraviolet (UV) light to cure inks instantly, resulting in durable and vibrant prints. However, like any other piece of advanced machinery, UV flatbed printers can encounter various issues that may disrupt the printing process. This article aims to provide comprehensive solutions to some of the most common problems faced by users of UV flatbed printers, ensuring smoother and more efficient operations.
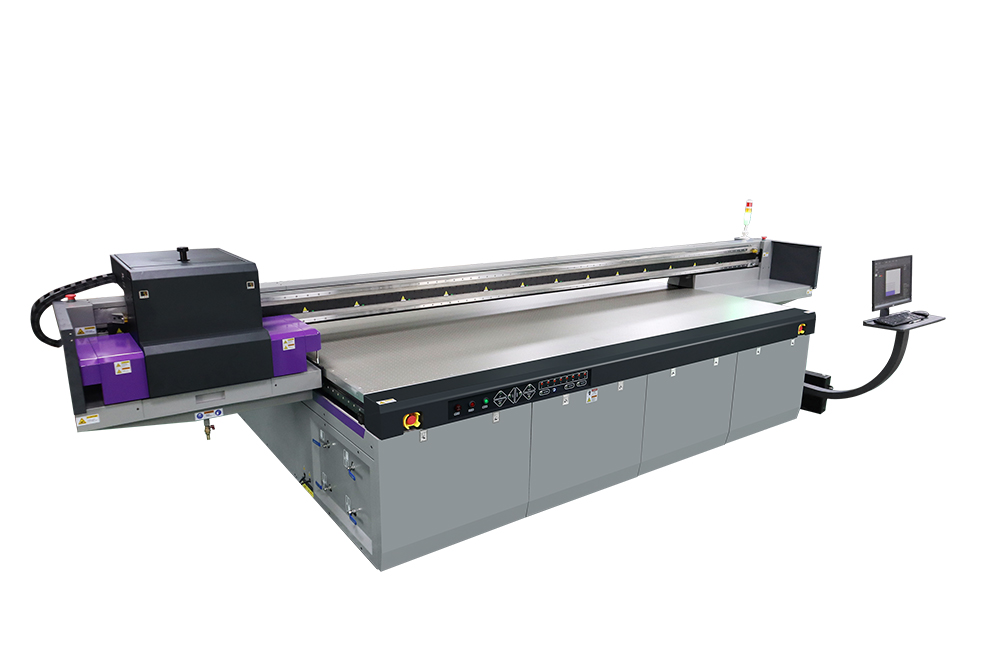
1. Print Quality Issues
One of the most frequent complaints with UV flatbed printers is subpar print quality. This can manifest as blurry images, banding, or uneven color distribution.
Solution:
Nozzle Check and Cleaning: Perform a nozzle check to identify any clogged or malfunctioning nozzles. Use the printer’s built-in cleaning utilities or manually clean the nozzles with a cleaning solution and a lint-free cloth. Regular maintenance, such as weekly or monthly cleanings, can prevent this issue.
Calibration: Ensure that the printer is properly calibrated. This includes calibrating the print heads, the media feed, and the UV lamps. Misalignment can lead to significant print quality issues. Refer to the printer’s manual for specific calibration instructions.
Ink Quality and Type: Use high-quality inks that are specifically designed for your UV flatbed printer. Incompatible or low-quality inks can cause poor print quality and even damage the printer over time. Additionally, ensure that the ink cartridges are not expired or empty.
Print Settings: Adjust the print settings to optimize print quality. This may include increasing the resolution, adjusting the ink density, or changing the print speed. Experiment with different settings to find the best combination for your specific job.
2. Adhesion Problems
UV inks need to adhere properly to the substrate to ensure a long-lasting and durable print. Adhesion issues can result in peeling, cracking, or complete failure of the ink to stick to the material.
Solution:
Substrate Preparation: Properly prepare the substrate before printing. This may involve cleaning it to remove any dust, oil, or contaminants that could interfere with ink adhesion. Some materials may also require a primer or coating to improve ink adherence.
Curing Settings: Adjust the UV lamp’s intensity and curing time. Over-curing can cause the ink to become too brittle and prone to cracking, while under-curing can result in poor adhesion. Consult the ink and substrate manufacturer’s recommendations for optimal curing settings.
Temperature and Humidity: Control the printing environment’s temperature and humidity. Extreme conditions can affect ink adhesion. Ideally, maintain a consistent temperature and low humidity levels to promote proper ink curing and adhesion.
3. Curing Issues
Improper curing is a common problem that can lead to a range of issues, including poor durability, color fading, and ink smearing.
Solution:
UV Lamp Maintenance: Regularly check and replace the UV lamps if they are worn out or not functioning at full capacity. UV lamps lose their effectiveness over time, and old lamps may not provide the necessary energy to cure the ink properly.
Lamp Positioning: Ensure that the UV lamps are correctly positioned and aligned with the print heads. Misalignment can result in uneven curing and poor print quality.
Curing Speed and Distance: Adjust the speed of the conveyor belt and the distance between the UV lamps and the printed material. Faster speeds may require more intense lamps or closer positioning to ensure proper curing.
4. Ink Smearing or Bleeding
Ink smearing or bleeding occurs when the ink spreads uncontrollably on the substrate, resulting in distorted or blurry prints.
Solution:
Ink Viscosity: Check the viscosity of the ink. Inks that are too thin may spread excessively. Adjust the ink viscosity according to the manufacturer’s recommendations.
Print Speed and Ink Drying: Reduce the print speed to allow more time for the ink to set before it is exposed to the UV light. This can help prevent smearing. Additionally, ensure that the ink is not over-applied, as excess ink can lead to bleeding.
Substrate Absorbency: Choose substrates that are compatible with UV inks and have the right absorbency levels. Highly absorbent materials may cause the ink to spread, while non-absorbent materials may require special treatments to ensure proper ink adhesion.
5. Software and Driver Issues
Problems with the printer’s software or drivers can cause a variety of issues, including print errors, connectivity problems, and system crashes.
Solution:
Updates: Regularly update the printer’s firmware, software, and drivers. Manufacturers often release updates to fix bugs, improve performance, and add new features.
Compatibility: Ensure that the printer’s software is compatible with your operating system and other software applications. Incompatibilities can lead to print errors and system instability.
Troubleshooting Tools: Use the printer’s built-in diagnostic tools to identify and resolve software issues. These tools can often pinpoint the problem and provide suggestions for a quick fix.
Technical Support: If the issue persists, contact the printer’s technical support team. They can provide expert assistance and may be able to remotely access the printer to diagnose and fix the problem.
6. Mechanical Problems
UV flatbed printers are complex machines with many moving parts, which can sometimes lead to mechanical issues.
Solution:
Regular Maintenance: Implement a regular maintenance schedule to keep the printer in good working condition. This includes cleaning the printer, checking for worn or damaged parts, and lubricating moving components.
Parts Replacement: Replace any worn or damaged parts promptly. This can prevent more serious issues from developing and ensure the printer operates smoothly.
Alignment and Adjustment: Regularly check and adjust the printer’s alignment, including the print heads, media feed, and conveyor belt. Misalignment can cause a variety of print issues.
7. Environmental Concerns
UV flatbed printers can produce harmful emissions, including volatile organic compounds (VOCs) and ozone, which can be hazardous to both the environment and the operator’s health.
Solution:
Ventilation: Ensure that the printing area is well-ventilated. Install exhaust fans or an air purification system to remove harmful emissions from the workspace.
Eco-Friendly Inks: Choose eco-friendly inks that have lower VOC content and produce fewer harmful emissions. These inks are often more sustainable and safer to use.
Operator Safety: Provide proper protective gear for operators, such as gloves, masks, and eye protection. Regularly train employees on safe operating procedures and the potential hazards associated with UV printing.
UV flatbed printers offer numerous benefits, including high-quality prints, versatility, and durability. However, like any other advanced machinery, they can encounter various issues that may disrupt the printing process. By following the solutions outlined in this article, you can address common problems with UV flatbed printers and ensure smoother, more efficient operations. Regular maintenance, proper ink and substrate selection, and attention to environmental concerns are key to maintaining the printer’s performance and longevity. With the right approach, you can maximize the potential of your UV flatbed printer and produce exceptional prints every time.