How to Troubleshoot a UV Flatbed Printer?
How to Troubleshoot a UV Flatbed Printer?
UV flatbed printers have revolutionized the printing industry, offering high-quality prints on various materials with exceptional detail and durability. However, like any complex machinery, they can encounter issues that require troubleshooting. This comprehensive guide will walk you through the common problems you might face with a UV flatbed printer and provide step-by-step solutions to help you resolve them efficiently.
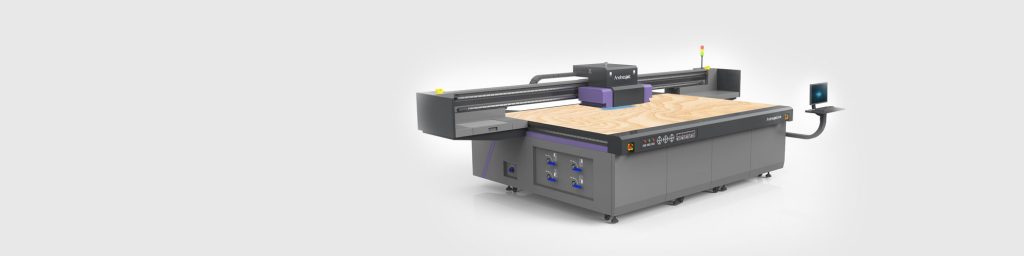
1. Understanding the Basics of UV Flatbed Printers
Before diving into troubleshooting, it’s crucial to understand the basic components and operation of a UV flatbed printer. UV flatbed printers use ultraviolet (UV) light to cure ink instantly after it’s deposited onto the material. This process allows for precise printing on a wide range of substrates, including glass, metal, plastic, and more.
The printer typically consists of the following key components:
Print Bed: The flat surface where the material is placed for printing.
Inkjet Heads: The components that deposit ink onto the material.
UV Lamps: These cure the ink immediately after deposition.
Control Panel: Used to operate the printer and adjust settings.
Software: Controls the printer’s functions and printing process.
2. Common Issues and Troubleshooting Steps
Issue 1: Print Quality Problems
One of the most common issues with UV flatbed printers is print quality problems, which can manifest in various ways, such as banding, blurring, or uneven ink deposition.
Troubleshooting Steps:
Check Ink Levels: Ensure all ink cartridges are adequately filled. Low ink levels can cause print quality issues.
Clean Print Heads: Over time, ink can accumulate on the print heads, affecting print quality. Use the printer’s cleaning function or manually clean the heads with a lint-free cloth and isopropyl alcohol.
Adjust Print Settings: Check the print resolution and ink density settings. Increasing the resolution can improve print quality, but it may also increase printing time.
Calibrate the Printer: Many printers offer a calibration feature that can help improve print quality. Follow the manufacturer’s instructions to perform the calibration.
Issue 2: Ink Curing Problems
If the ink isn’t curing properly, it can lead to smears, tackiness, or even complete failure of the print to adhere to the material.
Troubleshooting Steps:
Check UV Lamps: Ensure the UV lamps are functioning correctly. If they appear dim or are not curing the ink adequately, they may need to be replaced.
Adjust Lamp Intensity: Some printers allow you to adjust the intensity of the UV lamps. Increase the intensity if the ink isn’t curing properly.
Clean the Lamps: Dust and debris can accumulate on the lamps, reducing their effectiveness. Clean the lamps with a soft cloth to remove any obstructions.
Check Material Compatibility: Ensure the material you’re printing on is compatible with UV ink. Some materials may require specific ink types or curing settings.
Issue 3: Software and Connectivity Issues
Software glitches or connectivity problems can prevent the printer from receiving print jobs correctly.
Troubleshooting Steps:
Restart the Printer: Sometimes, a simple restart can resolve software issues.
Check Connections: Ensure all cables are securely connected, and the printer is properly connected to your computer or network.
Update Software and Drivers: Manufacturers often release updates to address software bugs. Check the manufacturer’s website for updates and install them if available.
Reinstall Software: If the issue persists, try uninstalling and reinstalling the printer software.
Issue 4: Mechanical Problems
Mechanical issues, such as motor failures or sensor malfunctions, can cause the printer to malfunction or stop working altogether.
Troubleshooting Steps:
Check for Obstructions: Ensure nothing is blocking the print bed or inkjet heads.
Inspect Mechanical Components: Look for any visible damage or wear on the printer’s mechanical components. Replace any damaged parts.
Contact Manufacturer Support: If you suspect a mechanical failure, it’s best to contact the manufacturer’s support team for assistance. They can provide guidance on troubleshooting and may offer to repair or replace faulty components.
Issue 5: Material Handling Issues
If the printer is not handling materials properly, it can lead to misaligned prints or damage to the material.
Troubleshooting Steps:
Check Material Guides: Ensure the material guides are properly adjusted to fit the thickness and size of the material you’re printing on.
Clean the Print Bed: Dust and debris on the print bed can cause materials to shift during printing. Clean the bed regularly to prevent this issue.
Adjust Print Speed: Printing too quickly can sometimes cause material handling issues. Try reducing the print speed to see if it resolves the problem.
3. Preventive Maintenance Tips
To minimize the occurrence of issues and extend the lifespan of your UV flatbed printer, follow these preventive maintenance tips:
Regularly clean the print heads and UV lamps.
Keep the printer’s software and drivers up to date.
Perform routine inspections of mechanical components.
Use only high-quality, manufacturer-recommended inks and materials.
Follow the manufacturer’s guidelines for proper printer usage and maintenance.
Conclusion
Troubleshooting a UV flatbed printer can be challenging, but with the right knowledge and tools, most issues can be resolved quickly. By understanding the printer’s components and following the troubleshooting steps outlined in this guide, you can ensure your printer operates efficiently and produces high-quality prints. Remember, preventive maintenance is key to minimizing downtime and maximizing the lifespan of your printer. If you encounter complex issues or are unsure how to proceed, don’t hesitate to contact the manufacturer’s support team for assistance.