How to Troubleshoot Common Problems with UV Flatbed Printers
How to Troubleshoot Common Problems with UV Flatbed Printers
UV flatbed printers have revolutionized the printing industry by offering versatility, precision, and durability in a wide range of applications, from advertising materials to industrial labeling. However, like any complex machinery, these printers can encounter various issues that disrupt workflow and compromise print quality. This article aims to guide users through the troubleshooting process for common problems encountered with UV flatbed printers, ensuring optimal performance and minimizing downtime.
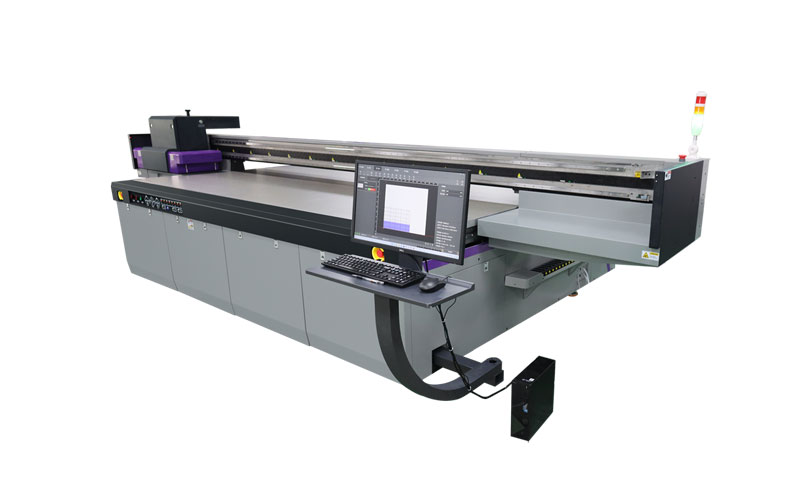
1. Understanding UV Flatbed Printer Basics
Before diving into troubleshooting, it’s essential to grasp the fundamentals of UV flatbed printers. These printers utilize ultraviolet (UV) light to cure ink instantly as it is deposited onto the substrate, enabling printing on diverse materials such as glass, metal, plastic, wood, and more. Key components include the print head, UV lamps, ink system, media handling system, and control software.
2. Common Problems and Troubleshooting Steps
2.1 Poor Print Quality
Issue: Prints appear blurry, streaky, or have missing areas.
Possible Causes:
Nozzle Clogs: Accumulated ink or dust can block nozzles, preventing proper ink flow.
Incorrect Print Head Alignment: Misalignment can result in uneven ink distribution.
Low Ink Levels: Insufficient ink supply can lead to faded prints.
Inappropriate Print Settings: Incorrect resolution, ink density, or pass settings.
Troubleshooting Steps:
Clean the Print Head: Use a cleaning solution and lint-free cloth to gently clean the nozzles. Avoid touching the nozzles directly.
Check Ink Levels: Ensure all ink cartridges are full and properly seated.
Run a Nozzle Check Pattern: This test print helps identify clogged or malfunctioning nozzles.
Realign the Print Head: Follow the printer’s manual instructions for alignment.
Adjust Print Settings: Increase resolution, adjust ink density, or add more passes as needed.
2.2 UV Lamp Issues
Issue: Prints are not fully cured or have uneven curing.
Possible Causes:
Aging UV Lamps: Over time, UV lamps lose intensity, reducing their curing effectiveness.
Lamp Misalignment: Improper positioning can lead to inconsistent curing.
Faulty Lamp Drivers: Electrical issues can prevent lamps from operating correctly.
Troubleshooting Steps:
Inspect UV Lamps: Check for cracks, blackening, or reduced brightness, indicating the need for replacement.
Realign UV Lamps: Ensure lamps are correctly positioned according to the manufacturer’s guidelines.
Test Lamp Functionality: Use a UV meter to check lamp output and ensure it meets specifications.
Replace Faulty Components: If lamp drivers are suspected, consult a technician for replacement.
2.3 Ink Adhesion Problems
Issue: Ink fails to adhere properly to the substrate, resulting in smudging or peeling.
Possible Causes:
Incompatible Ink or Substrate: Certain inks may not bond well with specific materials.
Substrate Preparation: Contaminants or improper cleaning can affect adhesion.
Curing Parameters: Incorrect curing time or temperature.
Troubleshooting Steps:
Verify Ink Compatibility: Consult the printer’s manual or supplier for suitable ink-substrate combinations.
Clean and Prepare the Substrate: Ensure the surface is clean, dry, and free of oils or contaminants.
Adjust Curing Settings: Increase or decrease curing time and intensity as needed.
Test Prints: Conduct small-scale tests to validate adhesion before full-scale production.
2.4 Media Handling Problems
Issue: Substrates jam, shift, or fail to load correctly.
Possible Causes:
Incorrect Media Settings: Misconfigured settings can cause handling errors.
Dirty or Damaged Rollers: Dust, debris, or worn-out rollers can impede movement.
Mechanical Issues: Faulty sensors or motors can disrupt media feeding.
Troubleshooting Steps:
Check Media Settings: Ensure the correct media type, size, and thickness are selected in the printer settings.
Clean Rollers: Use a clean, damp cloth to remove dirt and debris from rollers.
Inspect Mechanical Components: Look for signs of wear or damage on rollers, sensors, and motors. Replace if necessary.
Calibrate the Media Handling System: Follow the printer’s calibration procedures to ensure proper alignment and movement.
2.5 Software and Connectivity Issues
Issue: Printer fails to respond to commands, experiences software crashes, or has connectivity problems.
Possible Causes:
Outdated Software: Older firmware or drivers may not be compatible with current operating systems.
Corrupted Files: Damaged print files can cause software errors.
Network Issues: Unstable or weak connections can disrupt communication.
Troubleshooting Steps:
Update Software: Ensure the printer’s firmware and drivers are up-to-date.
Check Print Files: Verify file integrity and compatibility with the printer’s software.
Restart the Printer and Computer: Sometimes, a simple restart can resolve software glitches.
Troubleshoot Network Connections: Ensure a stable and secure connection between the printer and computer. Use wired connections if possible to minimize interference.
Restore Factory Settings: If problems persist, reset the printer to its default settings and reconfigure as needed.
3. Preventive Maintenance Tips
To minimize the occurrence of these issues, regular preventive maintenance is crucial:
Regular Cleaning: Clean the print head, UV lamps, and media handling components regularly.
Ink Management: Monitor ink levels and replace cartridges promptly to avoid running dry.
Calibration Checks: Perform routine calibration of the print head and media handling system.
Software Updates: Keep the printer’s software and drivers updated to the latest versions.
Environmental Control: Maintain a clean, dust-free, and temperature-controlled environment to protect the printer’s components.
4. When to Seek Professional Help
While many issues can be resolved through basic troubleshooting, some problems may require professional assistance. If you encounter complex electrical faults, persistent software errors, or hardware damages, contact the printer’s manufacturer or an authorized service provider. Their expertise can ensure a swift and accurate resolution, minimizing downtime and preserving the printer’s lifespan.
Conclusion
UV flatbed printers offer unparalleled versatility and precision, but like any sophisticated equipment, they can encounter various challenges. By understanding the printer’s basics, recognizing common problems, and following systematic troubleshooting steps, users can effectively diagnose and resolve issues, ensuring optimal print quality and operational efficiency. Regular maintenance and timely professional assistance further contribute to the printer’s longevity and performance. With these strategies in place, UV flatbed printer users can maximize productivity and deliver exceptional print results.