How to Troubleshoot UV Flatbed Printer Feed Issues
UV flatbed printers have revolutionized the printing industry with their ability to print on a wide range of materials and surfaces. From glass and metal to wood and plastic, these printers offer versatility and precision that was once unimaginable. However, like any sophisticated piece of equipment, UV flatbed printers can encounter issues that disrupt their operation. One common problem is feed issues, where the printer fails to feed media properly, leading to misprints, jams, or complete halts in the printing process. This article aims to guide you through the process of troubleshooting UV flatbed printer feed issues, ensuring you can quickly identify and resolve problems to maintain productivity.
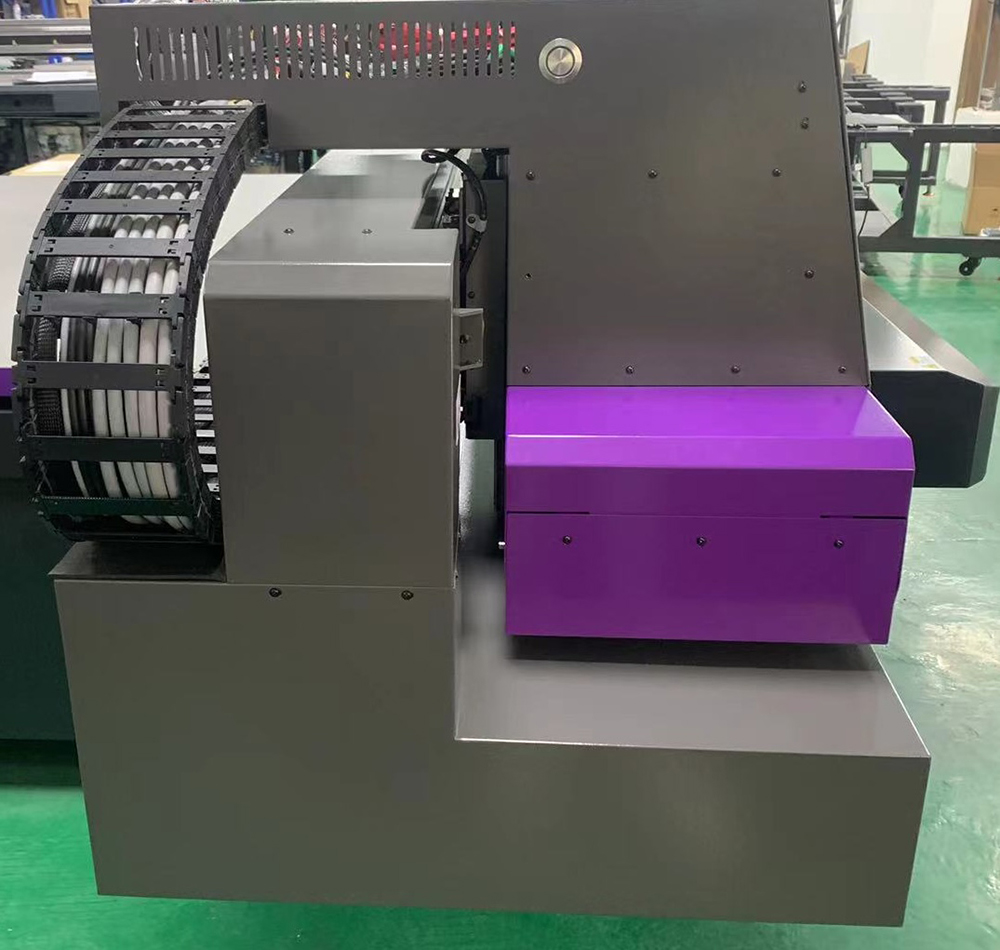
Before diving into troubleshooting, it’s essential to understand the basic components of the feed mechanism in a UV flatbed printer. Typically, the feed system consists of:
Media Roll Holders: These hold the rolls of media securely in place.
Feed Rollers: These rollers grip the media and pull it through the printer.
Sensor System: A series of sensors detect the presence, position, and movement of the media.
Motor and Drive System: This system powers the feed rollers, ensuring consistent and accurate media movement.
Common Feed Issues
Several factors can contribute to feed issues in UV flatbed printers. Some of the most common problems include:
Media Jams: When the media gets stuck in the printer, often due to misalignment or obstructions.
Skewing: The media moves off-center during feeding, causing prints to be crooked.
Inconsistent Feeding: The media feeds intermittently or at incorrect speeds.
No Feeding: The printer fails to pull the media through at all.
Initial Inspection
The first step in troubleshooting any feed issue is to perform a thorough inspection of the printer and its surroundings. Here’s what to check:
Media Quality and Condition: Ensure the media is not damaged, wrinkled, or too thick for the printer’s specifications.
Media Path Clearance: Check that the path through which the media feeds is clear of any debris, dust, or obstructions.
Rollers and Sensors: Inspect the feed rollers and sensors for dirt, debris, or wear. Clean them if necessary using a lint-free cloth and approved cleaning solutions.
Tension Settings: Verify that the media tension is correctly set according to the media type and thickness.
Step-by-Step Troubleshooting
If the initial inspection doesn’t reveal any obvious issues, follow these step-by-step troubleshooting procedures:
1. Check Media Loading
Proper Alignment: Ensure the media is loaded correctly on the roll holders, aligned with the feed path.
Core Adapters: Use the correct core adapters if the media roll has a different core size than the printer’s holder.
2. Calibrate the Feed System
Manual Calibration: Refer to the printer’s manual for instructions on how to manually calibrate the feed system. This process typically involves adjusting the sensors and rollers to ensure they are correctly aligned.
Automatic Calibration: If your printer supports automatic calibration, run the calibration routine to reset the feed system settings.
3. Examine the Sensor System
Sensor Functionality: Test the sensors to ensure they are detecting the media correctly. This may involve using a test strip or checking the sensor’s response through the printer’s diagnostic menu.
Sensor Position: Adjust the sensor positions if they are misaligned, ensuring they are correctly positioned to detect the media’s edge or presence.
4. Inspect the Motor and Drive System
Motor Operation: Listen for any unusual noises from the motor during operation. A faulty motor may produce grinding or whining sounds.
Drive Belts and Gears: Check drive belts and gears for wear, slippage, or damage. Replace any worn components as needed.
5. Software and Firmware
Firmware Updates: Ensure the printer’s firmware is up to date. Manufacturers often release firmware updates to address known issues and improve printer performance.
Print Settings: Verify that the print settings in the software are correctly configured for the media type and size being used.
6. Environmental Factors
Temperature and Humidity: Extreme temperature or humidity levels can affect the media’s behavior and the printer’s performance. Ensure the printing environment is within the recommended range.
Stable Surface: Make sure the printer is placed on a stable, level surface to prevent any vibrations or movements that could affect feeding.
Advanced Troubleshooting
If the basic troubleshooting steps do not resolve the issue, consider the following advanced steps:
Detailed Diagnostics: Use the printer’s built-in diagnostic tools to run detailed tests on the feed system. These tests can provide more specific error codes or identify faulty components.
Component Replacement: If a specific component, such as a feed roller or sensor, is identified as faulty, replace it with a new one.
Consult the Manufacturer: If you are unable to resolve the issue, contact the printer’s manufacturer for further assistance. They may provide additional troubleshooting steps or recommend sending the printer in for repair.
Preventive Measures
To minimize the chances of feed issues in the future, adopt the following preventive measures:
Regular Maintenance: Perform regular maintenance tasks, such as cleaning the rollers and sensors, to keep the printer in optimal condition.
Quality Media: Use high-quality media that meets the printer’s specifications to avoid feeding problems.
Operator Training: Ensure that operators are trained on proper media loading and printer operation to prevent user-related issues.
UV flatbed printer feed issues can be frustrating and disruptive, but with a systematic approach to troubleshooting, most problems can be quickly resolved. By understanding the feed mechanism, performing thorough inspections, following step-by-step troubleshooting procedures, and adopting preventive measures, you can maintain the smooth operation of your UV flatbed printer. Remember, proper maintenance and attention to detail are key to keeping your printer running efficiently and producing high-quality prints.