How to Troubleshoot UV Flatbed Printer Power Issues
UV flatbed printers have revolutionized the printing industry with their ability to produce high-quality, durable prints on a wide range of materials. However, like any sophisticated piece of equipment, they can encounter issues from time to time. One common problem that users may face is power-related troubles. Whether it’s the printer failing to turn on, experiencing intermittent power cuts, or showing error messages related to power supply, these issues can disrupt workflow and cause frustration. In this article, we will delve into the various methods to troubleshoot UV flatbed printer power issues, helping you get your printer back up and running efficiently.
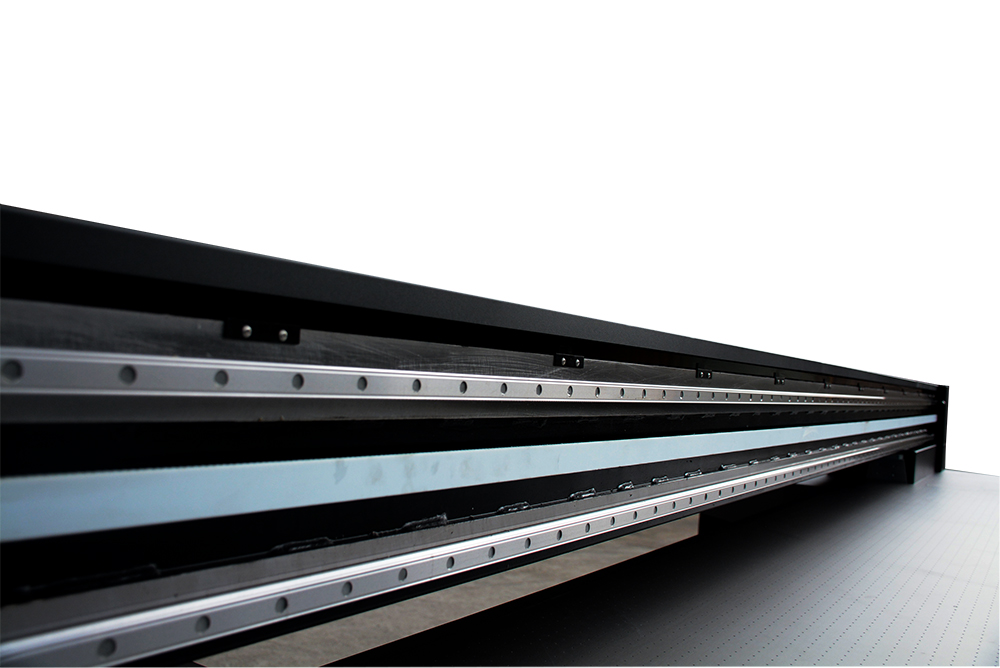
Understanding the Basics of UV Flatbed Printer Power Systems
Before diving into troubleshooting, it’s essential to have a basic understanding of how the power system in a UV flatbed printer works. These printers typically use a combination of main power supply units, power distribution boards, and various sensors to manage and distribute power effectively. The main power supply converts the AC (alternating current) from your electrical outlet into DC (direct current) that the printer’s components can use.
Common Power Issues and Their Causes
Printer Not Turning On:
Faulty Power Cord or Outlet: The most straightforward issue could be a damaged power cord or a non-functional electrical outlet.
Power Supply Unit (PSU) Failure: The PSU might be defective or overloaded.
Mainboard Issue: A problem with the printer’s mainboard can prevent it from receiving or processing power signals.
Intermittent Power Cuts:
Loose Connections: Loose wires or connectors inside the printer can cause intermittent power disruptions.
Overheating: Overheating of the PSU or other components can lead to automatic shutdowns to prevent damage.
Voltage Fluctuations: Unstable power supply from the outlet can cause the printer to shut down unexpectedly.
Power-Related Error Messages:
Sensor Malfunction: Faulty sensors can send incorrect signals about power status.
Firmware Bugs: Sometimes, software issues in the printer’s firmware can cause power-related error messages.
Step-by-Step Troubleshooting Guide
1. Check the Power Source
Inspect the Power Cord: Ensure that the power cord is not damaged and is securely plugged into both the printer and the electrical outlet.
Test the Outlet: Use a different device to test the outlet and confirm that it is working correctly. If the outlet is faulty, consult an electrician to repair or replace it.
Voltage Stability: If you suspect voltage fluctuations, consider using a voltage stabilizer or surge protector to provide a steady power supply to the printer.
2. Examine the Power Supply Unit (PSU)
Visual Inspection: Look for any signs of physical damage or burnout on the PSU. If you notice any, it’s likely that the PSU needs to be replaced.
Multimeter Test: Use a multimeter to test the output voltage of the PSU. Compare the readings with the specifications provided in the printer’s manual. If the voltage is not within the acceptable range, the PSU may be defective.
Ventilation and Cooling: Ensure that the PSU and surrounding components have adequate ventilation. Overheating can cause the PSU to shut down intermittently. Clean any dust or debris that may be obstructing airflow.
3. Investigate Internal Connections
Open the Printer Case: Carefully open the printer case, following the manufacturer’s guidelines to avoid damaging any components.
Check Connectors and Wires: Inspect all internal connectors and wires for any signs of looseness or damage. Re-seat any loose connectors and replace any damaged wires.
Power Distribution Board: Examine the power distribution board for any visible damage or burnt components. If you identify any issues, it may be necessary to replace the board.
4. Inspect the Mainboard
Visual Check: Look for any signs of physical damage or corrosion on the mainboard.
Component Testing: If you have access to diagnostic tools, test the mainboard components for functionality. Faulty capacitors or integrated circuits can cause power-related issues.
Firmware Update: Ensure that the printer’s firmware is up to date. Sometimes, firmware bugs can cause power-related error messages. Check the manufacturer’s website for any available updates and follow the instructions to install them.
5. Check Sensors and Other Components
Sensor Functionality: Verify that all sensors related to power management are functioning correctly. Faulty sensors can send incorrect signals, leading to power issues.
Other Components: Inspect other components, such as relays and fuses, for any signs of damage or wear. Replace any faulty components as necessary.
Preventive Measures
To minimize the chances of encountering power issues with your UV flatbed printer, consider the following preventive measures:
Regular Maintenance: Schedule regular maintenance checks to clean the printer and inspect its components.
Stable Power Supply: Use a reliable power source and consider installing a surge protector or uninterruptible power supply (UPS) to protect the printer from voltage fluctuations and power outages.
Proper Ventilation: Ensure that the printer has adequate ventilation to prevent overheating.
Handling Precautions: When handling the printer or its components, always follow proper precautions to avoid static discharge and physical damage.
Troubleshooting UV flatbed printer power issues can be a daunting task, but by following a systematic approach, you can identify and resolve the problem effectively. Start by checking the power source and PSU, then move on to internal connections, the mainboard, and other components. Regular maintenance and preventive measures can help reduce the likelihood of power-related problems.
Remember, if you are unsure about any step or if the issue persists despite your efforts, it’s best to consult a professional technician or contact the printer’s manufacturer for further assistance. With the right knowledge and tools, you can keep your UV flatbed printer running smoothly and ensure high-quality prints for your projects.