Technical Aspects of Color Management in UV Flatbed Printing
Technical Aspects of Color Management in UV Flatbed Printing
In the realm of digital printing, UV flatbed printing stands out for its versatility, durability, and the ability to print on a wide range of substrates. This technology utilizes ultraviolet (UV) light to cure inks instantly, resulting in vibrant, long-lasting prints. A crucial aspect of achieving exceptional print quality in UV flatbed printing is effective color management. Color management ensures that the colors seen on the computer screen closely match those produced on the printed material. This process involves a series of technical steps and considerations, from understanding color spaces and profiles to calibrating equipment and controlling inkjet performance. In this article, we will delve into the technical aspects of color management in UV flatbed printing, exploring how to achieve accurate and consistent color reproduction.
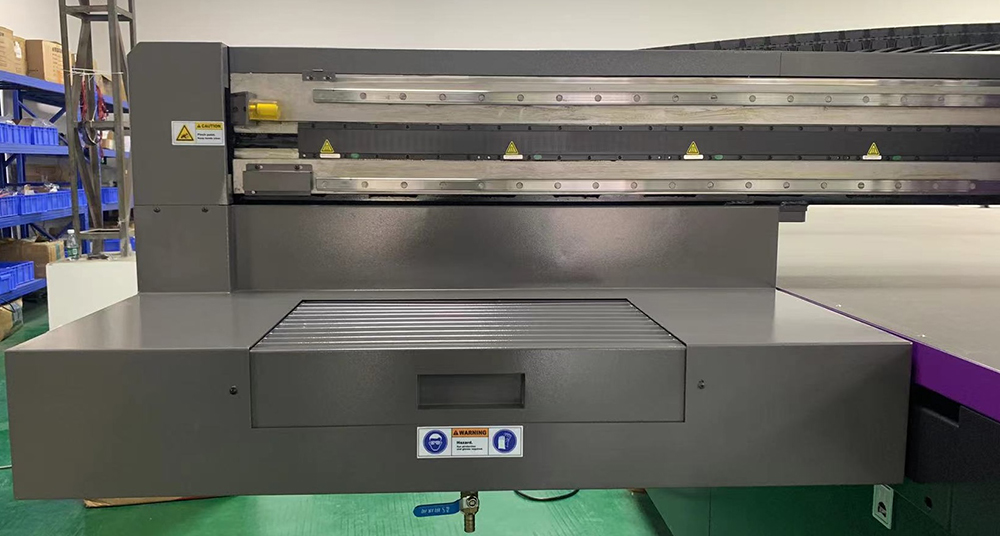
Understanding Color Spaces and Profiles
Color spaces, also known as color models, define the way colors are represented and communicated digitally. The most common color spaces in printing are RGB (Red, Green, Blue) for digital displays and CMYK (Cyan, Magenta, Yellow, Key/Black) for print. RGB is an additive color model, where colors are created by combining light, while CMYK is a subtractive model, where colors are created by absorbing light through ink on a substrate.
In UV flatbed printing, it is essential to convert RGB images to CMYK, as printers use CMYK inks. However, this conversion is not straightforward. Different printers, inks, and substrates can produce vastly different results from the same CMYK values. This is where color profiles come in. A color profile, or ICC profile (International Color Consortium), is a set of data that describes the color characteristics of a particular device or combination of devices. It acts as a translation tool, ensuring that colors are accurately interpreted and reproduced across different systems.
Profiles are created through a process called color calibration, where a series of known color patches are printed and measured. The differences between the expected and actual colors are analyzed, and the profile is adjusted to compensate for these discrepancies. For UV flatbed printing, both printer-specific and substrate-specific profiles may be required to achieve optimal color accuracy.
Calibration and Characterization
Calibration and characterization are two fundamental processes in color management. Calibration ensures that devices such as monitors, scanners, and printers are operating at their best performance, while characterization involves creating detailed profiles that describe how these devices behave under specific conditions.
For UV flatbed printers, calibration involves adjusting the printer’s settings to ensure consistent ink deposition, uniform UV curing, and accurate media handling. This may include adjusting print head alignment, ink pressure, and UV lamp intensity. Regular calibration is crucial, as changes in temperature, humidity, and ink viscosity can affect print quality over time.
Characterization, on the other hand, involves printing a series of color patches on the actual substrate that will be used for the final print. These patches are then measured using a spectrophotometer, which captures the exact color values. The data from these measurements is used to create a custom ICC profile for that specific printer, ink set, and substrate combination. This profile is then loaded into the printing software, allowing it to accurately translate digital color data into the appropriate ink combinations for the printer.
Inkjet Performance and Color Accuracy
The performance of the inkjet print heads is critical to achieving accurate and consistent color in UV flatbed printing. Factors such as drop size, drop placement accuracy, and inkjet frequency can all affect color reproduction. Advances in inkjet technology have led to the development of high-resolution print heads that can produce smaller, more precise drops, resulting in smoother gradients and sharper details.
Moreover, the chemistry of the UV inks themselves plays a significant role in color accuracy. UV inks are formulated to cure rapidly under UV light, but they must also be able to produce a wide color gamut and maintain color consistency over time. Manufacturers continuously improve ink formulations to enhance durability, adhesion, and color saturation while minimizing environmental impact.
To further improve color accuracy, some UV flatbed printers utilize multi-channel ink systems. These systems can include additional ink colors, such as light cyan and light magenta, to expand the color gamut and reduce the visibility of graininess in prints. Variable dot technologies, where the size of individual ink drops can be adjusted, also contribute to smoother color transitions and improved image quality.
Substrate Considerations
The choice of substrate can have a profound impact on color management in UV flatbed printing. Different materials absorb and reflect light differently, affecting the appearance of printed colors. For example, a glossy substrate will reflect more light, resulting in brighter, more saturated colors, while a matte substrate will absorb more light, producing a softer, more muted color palette.
It is essential to test and profile each substrate individually, as even slight variations in texture, absorbency, and color can affect the final print quality. Some substrates may require special pretreatments or primers to ensure proper ink adhesion and color accuracy. Additionally, the thickness and rigidity of the substrate can affect print head alignment and media handling, further impacting color consistency.
Software and Workflow Integration
Effective color management in UV flatbed printing also requires robust software solutions. Printing software, such as RIP (Raster Image Processor) software, plays a crucial role in translating digital files into printable data. A good RIP will support ICC profiles, allowing for accurate color matching, and offer advanced features such as color correction, image enhancement, and nesting optimization.
Workflow integration is another key aspect. In a typical UV flatbed printing environment, files may come from a variety of sources, each with its own color space and resolution. A streamlined workflow ensures that these files are properly converted, proofed, and printed, minimizing the risk of color errors. Automated systems can help manage job queues, track print progress, and maintain consistent print settings across multiple jobs.
Color Consistency Over Time
Maintaining color consistency over time is a challenge in any printing process, but it is especially critical in UV flatbed printing due to the high durability of the prints. Regular maintenance, including cleaning print heads, replacing worn parts, and recalibrating equipment, is essential. Additionally, monitoring environmental conditions such as temperature and humidity can help prevent color shifts due to external factors.
Implementing a color management system (CMS) can further enhance color consistency. A CMS centralizes color data, making it easier to manage profiles, track color performance, and make adjustments as needed. Some CMS solutions also offer remote diagnostic capabilities, allowing technicians to troubleshoot color issues without being physically present at the printer.
Color management in UV flatbed printing is a complex process that requires a deep understanding of color spaces, profiles, equipment calibration, inkjet performance, substrate characteristics, and software integration. By carefully controlling each of these factors, printers can achieve exceptional color accuracy and consistency, resulting in high-quality prints that meet or exceed customer expectations. As technology continues to evolve, so too will the tools and techniques used in color management, enabling even greater precision and control in UV flatbed printing.