Technical Aspects of Ink Drying and Curing in UV Flatbed Printers
Technical Aspects of Ink Drying and Curing in UV Flatbed Printers
Introduction
In the ever-evolving world of digital printing, UV flatbed printers have emerged as a game-changer, particularly in the realms of industrial and commercial printing. These printers offer unparalleled versatility, precision, and speed, making them ideal for a wide range of applications from packaging to signage. A crucial aspect of UV flatbed printing is the ink drying and curing process, which directly impacts the quality and durability of the final product. This article delves into the technical aspects of ink drying and curing in UV flatbed printers, exploring the underlying mechanisms, key components, and recent advancements in this field.
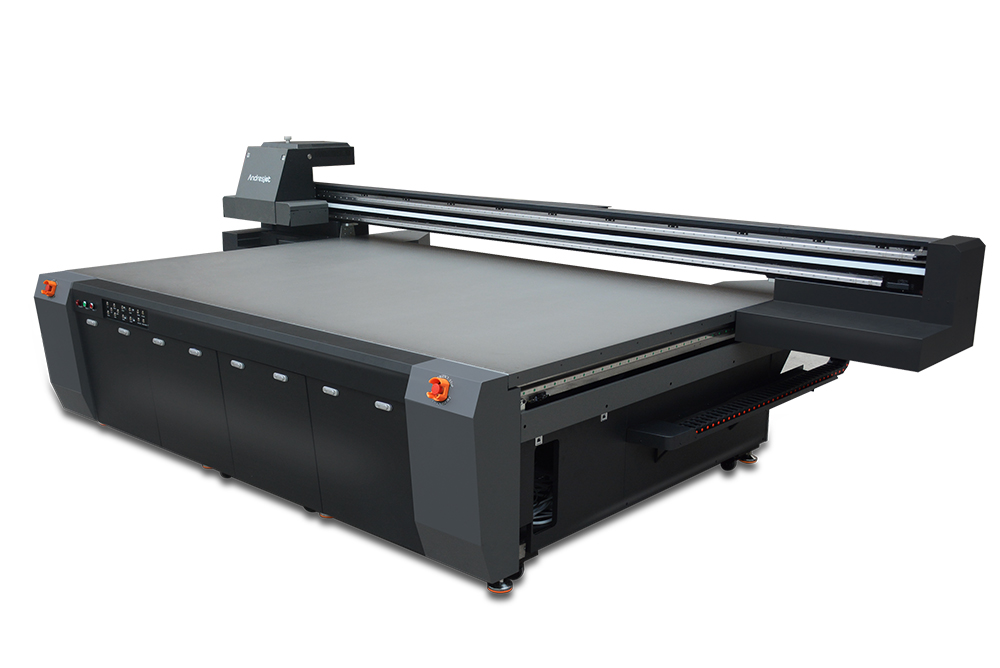
Understanding UV Ink Drying and Curing
UV ink drying and curing involve the rapid polymerization of ink components upon exposure to ultraviolet (UV) light. This process differs significantly from traditional solvent-based or aqueous ink systems, which rely on evaporation or absorption to dry. UV curing offers several advantages, including instant drying, reduced energy consumption, and environmental friendliness.
UV Ink Composition
UV inks are formulated specifically for rapid curing under UV light. They typically consist of three main components:
Oligomers: These are low molecular weight polymers that serve as the backbone of the ink film. Upon exposure to UV light, they undergo polymerization, forming a durable and cross-linked network.
Photoinitiators: These compounds absorb UV light and generate free radicals, which initiate the polymerization of oligomers.
Additives: Including pigments, dyes, and other functional additives, these components contribute to the color, viscosity, and other physical properties of the ink.
UV Curing Mechanism
The UV curing process can be broadly divided into two stages:
Absorption and Initiation: When UV light strikes the ink film, photoinitiators absorb the radiation and convert it into chemical energy. This energy triggers the generation of free radicals, which initiate the polymerization reaction.
Polymerization: The free radicals react with the oligomers, causing them to polymerize and cross-link, forming a dense and durable film. This process occurs rapidly, often within fractions of a second.
Key Components of UV Flatbed Printers for Ink Drying and Curing
UV flatbed printers incorporate several specialized components to facilitate the efficient drying and curing of UV inks. These include:
UV LED Curing Systems
UV LED curing systems have become increasingly popular in UV flatbed printers due to their energy efficiency, long lifespan, and instant on/off capabilities. Compared to traditional mercury arc lamps, UV LEDs emit narrow-band radiation, allowing for more precise control over the curing process.
UV LED curing systems typically consist of an array of LED chips mounted on a heat sink. The LED chips emit UV light of specific wavelengths (commonly 365nm, 385nm, or 395nm), which is directed onto the ink film through optical lenses or reflectors. The intensity and duration of UV exposure can be adjusted to optimize the curing profile for different ink formulations and substrate materials.
Cooling Systems
UV LEDs generate heat during operation, which must be effectively dissipated to prevent thermal damage to the curing system and maintain consistent curing performance. Water-cooled UV LED curing systems employ a closed-loop water circulation system to remove heat from the LED array. This not only prolongs the lifespan of the LEDs but also ensures stable and reliable curing performance over extended periods.
Control Systems
Advanced control systems monitor and regulate various parameters during the UV curing process, including UV intensity, exposure time, and temperature. These systems often incorporate feedback loops to automatically adjust curing parameters in response to changes in the ink film or substrate material. Some systems even incorporate intelligent algorithms that optimize the curing profile based on real-time data, further enhancing the quality and consistency of the final product.
Technical Considerations for Efficient Ink Drying and Curing
Achieving efficient ink drying and curing in UV flatbed printers requires careful consideration of several technical factors, including:
Ink Formulation
The choice of UV ink formulation significantly impacts the curing process. Factors such as the type and concentration of photoinitiators, the molecular weight and functionality of oligomers, and the presence of additives can all affect the curing speed, final film properties, and overall print quality. Printer manufacturers and ink suppliers collaborate closely to develop ink formulations optimized for specific applications and UV curing systems.
Substrate Material
The type and properties of the substrate material also play a crucial role in the curing process. Different materials absorb UV light differently, and some may require higher UV intensities or longer exposure times to achieve complete curing. In addition, the surface energy, roughness, and thermal conductivity of the substrate can affect the adhesion and uniformity of the ink film, further influencing the curing outcome.
Curing Profile
The curing profile—defined by UV intensity, exposure time, and other parameters—must be carefully tailored to the specific ink formulation and substrate material. An optimal curing profile ensures complete curing of the ink film while minimizing potential issues such as overcuring (which can lead to embrittlement or cracking) or undercuring (which can result in poor adhesion or ink transfer).
Environmental Conditions
Environmental conditions such as temperature and humidity can also affect the curing process. High temperatures can accelerate the curing reaction, while humidity can affect the surface energy of the substrate and the viscosity of the ink. Printer operators must monitor and control these conditions to ensure consistent curing performance.
Recent Advancements and Future Trends
The field of UV curing in UV flatbed printers continues to evolve, driven by technological advancements and changing market demands. Some of the recent trends and advancements include:
High-Power UV LEDs
High-power UV LEDs offer increased intensity and throughput, enabling faster curing speeds and higher productivity. These LEDs are particularly well-suited for industrial-scale UV flatbed printers, where speed and efficiency are paramount.
Multi-Wavelength Curing
Multi-wavelength UV curing systems employ a combination of UV LEDs emitting at different wavelengths. This approach allows for more precise control over the curing process, enabling printer operators to optimize curing profiles for specific ink formulations and substrate materials.
Intelligent Curing Systems
Intelligent curing systems incorporate advanced sensors, algorithms, and machine learning techniques to monitor and optimize the curing process in real-time. These systems can automatically adjust UV intensity, exposure time, and other parameters to account for variations in ink formulation, substrate material, and environmental conditions, ensuring consistent and high-quality curing performance.
Environmental Sustainability
As concerns over environmental sustainability grow, UV flatbed printer manufacturers are increasingly focusing on developing eco-friendly ink formulations and curing systems. This includes the use of low-VOC (volatile organic compound) inks, energy-efficient UV LEDs, and recyclable or biodegradable materials in printer components.
Conclusion
The technical aspects of ink drying and curing in UV flatbed printers are complex yet critical to achieving high-quality and durable prints. By understanding the underlying mechanisms, key components, and recent advancements in this field, printer operators can optimize the curing process to meet specific application requirements and market demands. As the industry continues to evolve, we can expect to see further advancements in UV curing technology, driving the development of more efficient, sustainable, and intelligent UV flatbed printers.