Technical Aspects of Integrating UV Flatbed Printers into Workflows
In today’s fast-paced printing industry, businesses are constantly seeking ways to enhance efficiency, versatility, and the quality of their output. One technology that has significantly contributed to this evolution is the UV flatbed printer. These printers, known for their ability to print directly onto a wide range of substrates, offer numerous advantages over traditional printing methods. However, integrating UV flatbed printers into existing workflows is not a straightforward process. It requires careful planning, consideration of technical specifications, and adjustments to ensure optimal performance and seamless operation. This article delves into the technical aspects of integrating UV flatbed printers into workflows, highlighting key considerations, challenges, and best practices.
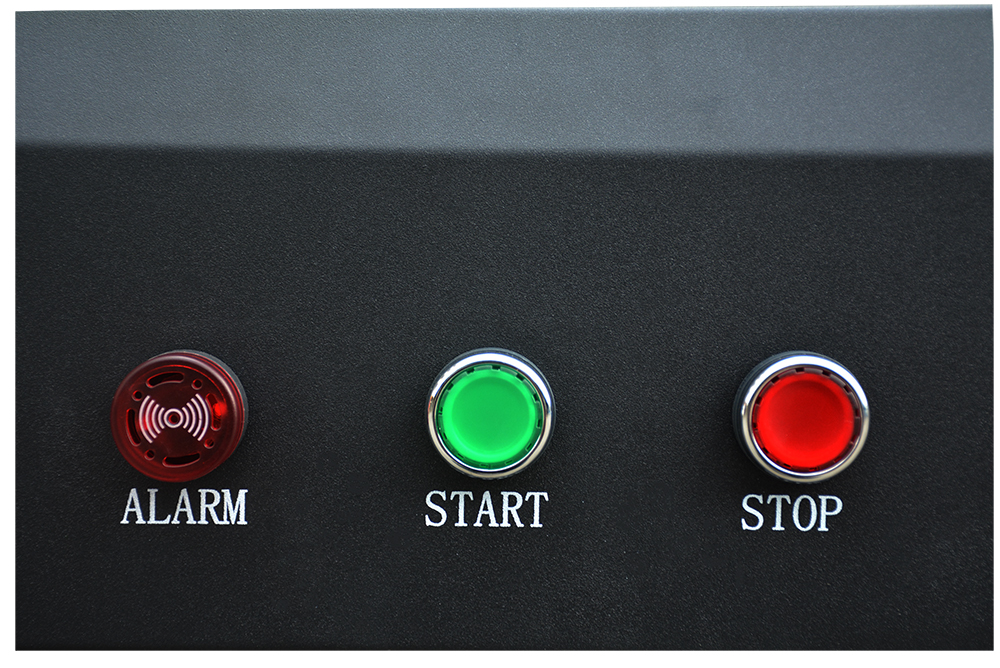
Understanding UV Flatbed Printers
UV flatbed printers utilize ultraviolet light to cure inks instantly upon contact with the substrate. This technology allows for printing on various materials such as plastics, metals, glass, wood, and even textiles. The process involves applying ink to the surface and then exposing it to UV light, which causes the ink to harden and adhere to the material. This results in vibrant, durable prints that are resistant to fading and wear.
One of the primary advantages of UV flatbed printers is their ability to print on three-dimensional objects and irregular surfaces, making them ideal for personalized and custom printing jobs. Additionally, they offer high resolution and precise color matching, making them suitable for applications requiring intricate details and vibrant colors.
Technical Considerations for Integration
Integrating UV flatbed printers into existing workflows involves several technical considerations to ensure compatibility, efficiency, and quality.
1. Substrate Compatibility
The versatility of UV flatbed printers allows for printing on a wide range of substrates. However, it is crucial to consider the specific requirements of each substrate. Factors such as material thickness, texture, and porosity can affect ink adhesion and curing. Conducting tests with different substrates is essential to determine the optimal printing parameters and ink types.
Moreover, some substrates may require pre-treatment or the use of specific primers to ensure proper ink adhesion. Understanding these requirements and incorporating them into the workflow can prevent issues such as ink bleeding, peeling, or poor color saturation.
2. Printer Configuration and Calibration
Proper configuration and calibration of the UV flatbed printer are critical for achieving high-quality prints. This includes setting the correct print resolution, adjusting the ink drop size, and calibrating the color profile to match the desired output.
Regular maintenance, such as cleaning the print heads and ensuring the UV lamps are functioning correctly, is also vital. A well-maintained printer will not only produce better quality prints but also minimize downtime and the need for costly repairs.
3. Software Integration
Integrating UV flatbed printers into existing workflows often requires the use of specialized software. This software is responsible for controlling the printer, managing print queues, and processing print files. Compatibility with existing design and production software, such as Adobe Illustrator or CorelDRAW, is crucial for a smooth workflow.
In some cases, custom software solutions may be necessary to facilitate seamless integration. This could involve developing interfaces that allow for easy transfer of print jobs between different systems or automating certain tasks to streamline the process.
4. Workflow Optimization
Optimizing the workflow to incorporate UV flatbed printers involves rethinking traditional processes and identifying areas where efficiency can be improved. For example, digitizing manual steps such as file preparation, substrate handling, and quality control can significantly reduce production time.
Implementing a just-in-time (JIT) production model can also be beneficial. By printing only what is needed when it is needed, businesses can reduce waste, minimize inventory costs, and improve responsiveness to customer demands.
Challenges and Solutions
While the benefits of integrating UV flatbed printers into workflows are numerous, there are also challenges that need to be addressed.
1. Initial Investment and Operating Costs
UV flatbed printers can be a significant investment, both in terms of the initial purchase and ongoing operating costs. Factors such as ink consumption, maintenance, and repairs can add up over time.
To mitigate these costs, businesses should conduct a thorough cost-benefit analysis before purchasing. Consider factors such as the printer’s lifespan, the volume of print jobs, and potential revenue generation. Additionally, exploring financing options or leasing agreements can make the initial investment more manageable.
2. Learning Curve
Operators need to be trained on the specific functionalities and maintenance requirements of UV flatbed printers. This can involve a steep learning curve, particularly for those not familiar with digital printing technologies.
Providing comprehensive training programs and ongoing support can help operators transition smoothly. Additionally, leveraging the expertise of printer manufacturers or third-party consultants can provide valuable insights and troubleshooting assistance.
3. Quality Control
Maintaining consistent print quality is a challenge in any printing process. With UV flatbed printers, factors such as ink consistency, substrate variability, and printer calibration can affect the final output.
Implementing a robust quality control process is essential. This could involve regular print tests, color calibration checks, and substrate inspections. Utilizing automated quality control tools, such as inline inspection systems, can further enhance consistency and reduce the risk of errors.
Best Practices for Integration
To ensure a successful integration of UV flatbed printers into workflows, consider the following best practices:
Conduct a Needs Assessment:
Before purchasing a UV flatbed printer, assess your business’s specific needs. Consider the types of jobs you will be printing, the substrates you will be using, and the volume of print jobs.
Choose the Right Printer:
Select a printer that aligns with your business’s requirements in terms of print size, resolution, speed, and substrate compatibility.
Invest in Training:
Provide comprehensive training for operators to ensure they are proficient in using the printer and understanding its maintenance requirements.
Optimize Workflow:
Streamline your workflow by digitizing manual processes, implementing JIT production models, and utilizing automation tools.
Maintain Regular Communication:
Establish open lines of communication with printer manufacturers or service providers for ongoing support and troubleshooting.
Monitor and Evaluate:
Regularly monitor the printer’s performance and evaluate its impact on your workflow. Make adjustments as necessary to improve efficiency and quality.
Integrating UV flatbed printers into workflows is a strategic decision that can significantly enhance a business’s printing capabilities. However, it requires careful planning, consideration of technical specifications, and adjustments to ensure optimal performance. By understanding the technical aspects of UV flatbed printers, addressing potential challenges, and following best practices, businesses can seamlessly integrate these printers into their workflows, ultimately improving efficiency, versatility, and print quality.
As the printing industry continues to evolve, UV flatbed printers will play an increasingly important role. By staying informed and adapting to new technologies, businesses can remain competitive and meet the ever-changing demands of their customers.