Technical Aspects of Media Handling in UV Flatbed Printers
Technical Aspects of Media Handling in UV Flatbed Printers
In the rapidly evolving world of digital printing, UV flatbed printers have emerged as a versatile and efficient solution for a wide range of industries, including advertising, packaging, and decoration. These printers offer unparalleled precision, speed, and versatility in handling various media types, making them an indispensable tool for modern printing applications. This article delves into the technical aspects of media handling in UV flatbed printers, exploring the key features, mechanisms, and considerations that contribute to their superior performance.
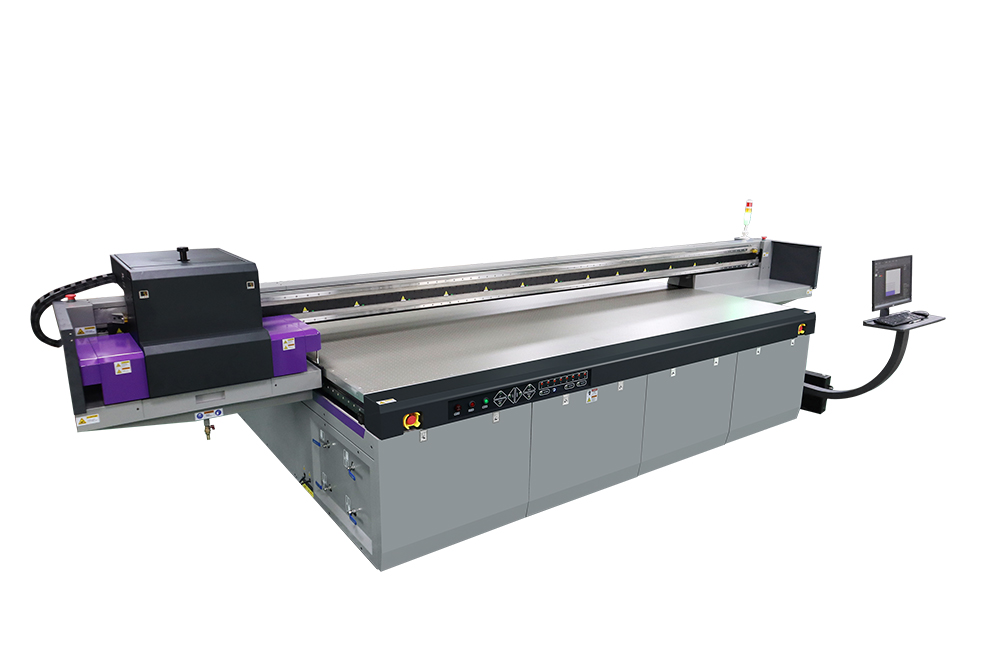
Introduction
UV flatbed printers employ ultraviolet (UV) curing technology, which allows for instant drying of inks, enabling high-speed printing on diverse substrates. Their flatbed design accommodates rigid and flexible materials alike, making them ideal for applications where precision and versatility are paramount. The media handling capabilities of UV flatbed printers are crucial to achieving optimal print quality and efficiency.
Media Handling Mechanisms
Feed and Alignment Systems
The first step in effective media handling involves the precise feeding and alignment of the material onto the printer’s platen. UV flatbed printers typically employ automated feeding systems that can handle rolls or sheets of various sizes and thicknesses. These systems incorporate sensors and actuators to ensure accurate positioning, minimizing waste and enhancing print quality.
Alignment mechanisms are equally important, as even minor misalignments can lead to visible defects in the final print. Advanced UV flatbed printers utilize sophisticated alignment software and hardware to automatically adjust the media position, ensuring that every print job starts with precise alignment.
Vacuum Table
A key feature of UV flatbed printers is their vacuum table, which securely holds the media in place during the printing process. The vacuum table ensures that the material remains flat and immobile, preventing distortions or shifting that could compromise print quality. The vacuum system is typically designed to accommodate a wide range of media thicknesses, allowing for seamless transitions between different materials.
Media Clamping Systems
In addition to the vacuum table, some UV flatbed printers incorporate media clamping systems to further secure the material during printing. These systems, often used in conjunction with the vacuum table, apply physical pressure to the edges of the media, preventing any movement during the high-speed printing process. Clamping systems are particularly useful for thin or flexible materials that might otherwise be prone to curling or lifting.
Material Compatibility
One of the greatest strengths of UV flatbed printers lies in their ability to handle a diverse range of media types. From rigid substrates like wood, metal, and glass to flexible materials such as PVC, textiles, and leather, UV printers can print on virtually any surface.
Rigid Substrates
Rigid substrates, including wood, metal, and acrylic, present unique challenges in terms of media handling. UV flatbed printers overcome these challenges by providing robust vacuum tables and clamping systems that can securely hold these materials in place. The UV curing technology also allows for instant drying, minimizing the risk of warping or distortion that might occur with traditional inks.
Flexible Substrates
Flexible substrates, on the other hand, require a delicate balance between secure holding and minimal distortion. UV flatbed printers achieve this through a combination of vacuum suction, media guides, and, in some cases, specialized rollers or belts. The instant drying capabilities of UV inks further enhance the printability of flexible materials, enabling high-quality prints on textiles, films, and other flexible substrates.
Precision and Resolution
Precision and resolution are critical factors in media handling for UV flatbed printers. High-resolution printing demands precise control over the media position, ink deposition, and curing process.
Precision Positioning
Precision positioning mechanisms ensure that the print heads move with extreme accuracy across the media surface. These mechanisms, often incorporating servo motors and high-resolution encoders, allow for micron-level control over the print head’s movements. This level of precision is essential for achieving sharp images, crisp text, and accurate registration between colors.
High-Resolution Printing
UV flatbed printers typically employ advanced print heads that can deliver resolutions exceeding 600 dpi (dots per inch) and even higher in some cases. These print heads use piezoelectric or thermal technology to precisely deposit UV-curable inks onto the media surface. The high resolution, combined with the precision positioning mechanisms, enables UV flatbed printers to produce prints with unparalleled clarity and detail.
Speed and Efficiency
In addition to precision and resolution, speed and efficiency are also crucial aspects of media handling in UV flatbed printers. These printers are designed to operate at high speeds, allowing for rapid throughput of a wide range of materials.
High-Speed Printing
High-speed printing capabilities are achieved through a combination of factors, including fast print head movement, efficient ink delivery systems, and rapid UV curing. UV inks cure instantly upon exposure to UV light, eliminating the need for lengthy drying times associated with traditional inks. This allows UV flatbed printers to maintain high speeds without compromising print quality.
Media Handling Efficiency
Media handling efficiency is also critical to the overall speed and productivity of UV flatbed printers. Automated feeding and unloading systems, combined with precise alignment and secure holding mechanisms, minimize downtime and ensure smooth, continuous operation. These systems also reduce the risk of human error, further enhancing the printers’ overall efficiency.
Maintenance and Durability
The durability and maintenance requirements of UV flatbed printers are also important considerations in media handling. These printers are designed to withstand heavy use and frequent material changes, making them suitable for demanding production environments.
Durable Construction
UV flatbed printers feature robust constructions, often incorporating stainless steel frames and heavy-duty components. These designs ensure that the printers can withstand the rigors of continuous operation and frequent material changes. The vacuum tables and clamping systems are also designed for long-term durability, ensuring reliable media holding over the printer’s lifetime.
Maintenance Requirements
Regular maintenance is essential to maintaining the optimal performance of UV flatbed printers. This includes cleaning the print heads, replacing consumables such as UV lamps and filters, and calibrating the alignment and positioning systems. Many modern UV flatbed printers incorporate automated maintenance routines that simplify the process and minimize downtime.
Conclusion
Media handling in UV flatbed printers is a complex yet crucial aspect of their operation. The precision, versatility, and efficiency of these printers are largely dependent on their ability to handle a wide range of materials with consistency and reliability. From automated feeding and alignment systems to robust vacuum tables and high-resolution printing capabilities, UV flatbed printers offer a unique combination of features that make them ideal for a wide range of printing applications.
As technology continues to evolve, we can expect to see further advancements in media handling and other aspects of UV flatbed printers. These advancements will no doubt drive the printers’ adoption in even more industries, further solidifying their position as a vital tool in the world of digital printing.