Technical Aspects of Printing on Fabric with a UV Flatbed Printer
Technical Aspects of Printing on Fabric with a UV Flatbed Printer
In the realm of digital printing, the application of UV flatbed printers on fabric has emerged as a groundbreaking technology, revolutionizing the textile industry with its versatility, precision, and efficiency. This article delves into the technical aspects of printing on fabric using a UV flatbed printer, exploring the printer’s mechanism, ink technology, substrate compatibility, print quality, and post-processing requirements.
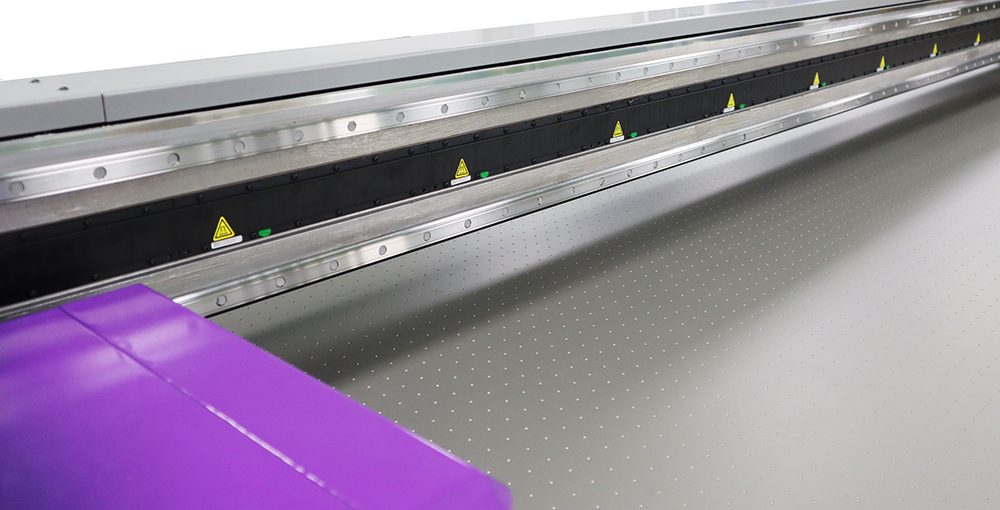
UV Flatbed Printer Mechanism
UV flatbed printers are designed to accommodate a wide range of materials, including rigid and flexible substrates. The printer’s flatbed platform allows for easy loading and unloading of the fabric, making it suitable for both small and large-scale production. The printing process involves the use of UV-curable inks that are jetted onto the fabric surface through a series of printheads. These printheads can move along the X and Y axes, ensuring precise and detailed printing.
One of the key advantages of UV flatbed printers is their ability to print on various thicknesses and textures of fabric without requiring significant adjustments. This versatility is achieved through the printer’s advanced printhead technology, which can maintain consistent ink drop size and placement regardless of the substrate’s surface characteristics.
UV-Curable Ink Technology
UV-curable inks are a crucial component of fabric printing with UV flatbed printers. These inks are formulated to cure (or dry) instantly when exposed to UV light. This rapid curing process enables the printer to produce high-quality prints with minimal ink bleeding or smearing, even on absorbent fabrics.
UV inks are typically composed of monomers, oligomers, photoinitiators, and additives. The photoinitiators react to UV light, triggering a chemical reaction that transforms the liquid ink into a solid polymer. This transformation occurs within seconds, allowing for immediate handling and finishing of the printed fabric.
Moreover, UV inks offer excellent color gamut and durability. They are resistant to fading, scratching, and chemical exposure, making them ideal for both indoor and outdoor applications. The inks’ ability to adhere strongly to the fabric surface also ensures long-lasting prints that can withstand repeated washing and wear.
Substrate Compatibility and Preparation
When printing on fabric with a UV flatbed printer, substrate compatibility is a critical consideration. Most natural and synthetic fabrics, such as cotton, polyester, nylon, and blends, are suitable for UV printing. However, the fabric’s surface properties, including texture, porosity, and stretchability, can affect the print quality.
Before printing, the fabric must be properly prepared. This typically involves cleaning the fabric to remove any dirt, oils, or contaminants that could interfere with ink adhesion. Depending on the fabric type, a pre-treatment step may be necessary to enhance ink receptivity and print durability. Pre-treatment can include applying a coating or primer specifically designed for UV inks.
Additionally, fabric tension and positioning on the printer’s bed are crucial for achieving optimal print results. Proper tensioning ensures that the fabric remains flat and taut during the printing process, preventing ink pooling or banding. Accurate positioning ensures that the print design aligns correctly with the fabric’s edges or seams.
Print Quality and Resolution
UV flatbed printers are capable of producing high-resolution prints on fabric, with some models achieving resolutions up to 600 dpi (dots per inch) or higher. This level of detail allows for intricate designs and sharp text rendering, making UV flatbed printing suitable for a wide range of applications, from fashion and apparel to home decor and signage.
Print quality is further enhanced by the printer’s ability to lay down multiple ink layers, a process known as ink build-up. By applying multiple passes of ink, the printer can achieve deeper, more saturated colors and smoother gradients. This capability is particularly advantageous for reproducing photographic images or complex graphics on fabric.
Post-Processing and Finishing
After printing, the fabric may require post-processing to ensure optimal print quality and durability. One common post-processing step is curing the inks with additional UV light exposure. This ensures that any residual ink is fully cured and that the print is completely dry.
For certain applications, the printed fabric may need to be heat-set. This process involves applying heat to the fabric, which helps to further fix the inks and improve washability. Heat-setting can also enhance the fabric’s hand feel and drapeability.
Finally, the printed fabric may require cutting, sewing, or other finishing processes to create the final product. It is essential to handle the fabric carefully during these steps to avoid damaging the print.
Environmental Considerations
UV flatbed printing on fabric is an environmentally friendly process compared to traditional textile printing methods. UV inks are solvent-free, meaning they do not emit volatile organic compounds (VOCs) during the printing or curing process. This reduces air pollution and creates a safer working environment for printer operators.
Furthermore, UV printing is a more efficient use of ink, as the printer deposits only the necessary amount of ink onto the fabric. This reduces ink waste and lowers the overall cost of production.
Conclusion
Printing on fabric with a UV flatbed printer offers numerous advantages, including versatility, high print quality, and environmental sustainability. The use of UV-curable inks and advanced printhead technology enables precise and detailed printing on a wide range of fabric types. Proper substrate preparation, attention to print quality and resolution, and careful post-processing are essential for achieving optimal results. As the technology continues to evolve, UV flatbed printing on fabric will likely play an increasingly important role in the textile industry, driving innovation and expanding the boundaries of creative expression.