Technical Aspects of Printing on Transparent Materials with UV Flatbed Printers
In the realm of digital printing, the ability to print on a diverse range of substrates has revolutionized numerous industries, from graphics and advertising to packaging and product decoration. One particularly intriguing and challenging area is printing on transparent materials using UV flatbed printers. This technology not only pushes the boundaries of creative expression but also demands a deep understanding of both the printing process and the unique properties of transparent substrates. This article delves into the technical aspects of achieving high-quality prints on transparent materials with UV flatbed printers, exploring key considerations such as ink selection, printhead technology, curing processes, and material handling.
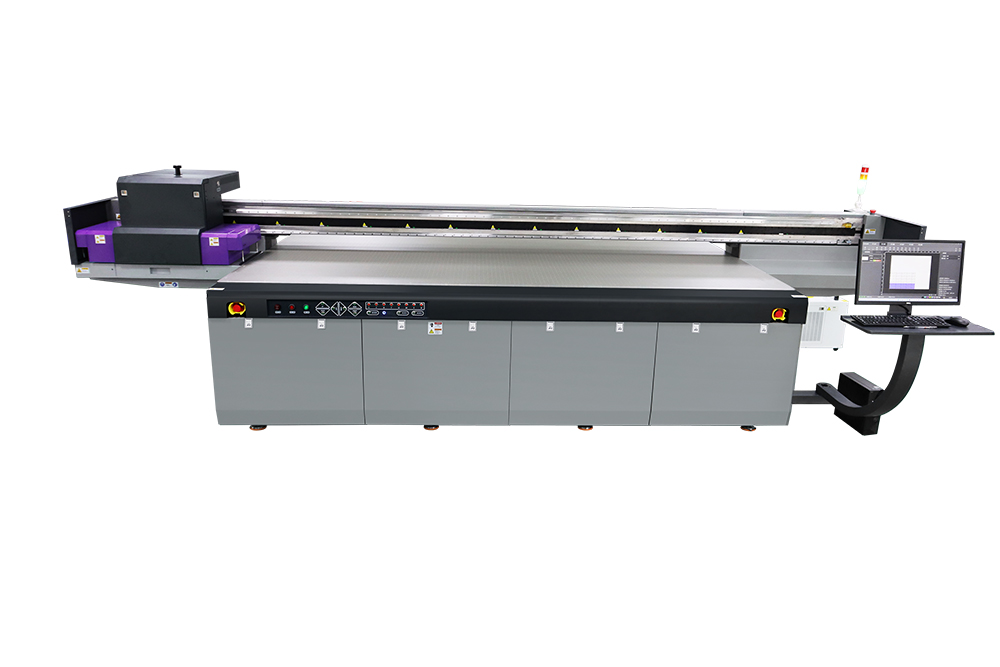
Understanding UV Flatbed Printers
UV flatbed printers are advanced digital printing machines that utilize ultraviolet (UV) light to cure inks instantly upon deposition. This technology allows for printing directly onto a wide variety of flat or slightly curved surfaces, including glass, plastic, metal, and, notably, transparent materials. The UV-curing process involves exposing the ink to high-intensity UV light immediately after it is jetted onto the substrate. This rapid curing ensures that the ink adheres firmly and dries almost instantaneously, enabling precise and detailed prints even on non-absorbent surfaces.
Ink Selection: A Critical Factor
The choice of ink is paramount when printing on transparent materials. UV-curable inks are specially formulated to adhere to a broad spectrum of surfaces and to cure rapidly under UV light. For transparent substrates, inks must possess excellent transparency, high color saturation, and good resistance to fading and scratching. Moreover, they should be compatible with the specific chemical composition and surface energy of the transparent material to ensure proper wetting and adhesion.
Pigment-based UV inks are often preferred for their superior lightfastness and durability. These inks contain finely ground particles of colorant that remain suspended in a liquid resin. When exposed to UV light, the resin polymerizes, locking the pigments in place and creating a durable, scratch-resistant image. In contrast, dye-based UV inks, while offering vibrant colors and good transparency, may be less durable and more susceptible to fading over time.
Printhead Technology: Precision and Versatility
The printhead is the heart of any UV flatbed printer, responsible for depositing ink onto the substrate with exceptional accuracy and consistency. Piezoelectric printheads are commonly used in UV flatbed printers due to their ability to eject precise droplets of ink at high speeds and with excellent control over droplet size and placement. This precision is crucial when printing on transparent materials, where even the slightest misalignment or variation in droplet size can result in visible imperfections.
Advanced printhead technologies, such as those with variable droplet sizes, enable printers to achieve a wider range of print effects, from fine detail work to solid color areas. This versatility is particularly beneficial when printing on transparent materials, where the ability to transition smoothly between fine text and large, solid graphics can greatly enhance the overall appearance of the printed piece.
Curing Processes: Ensuring Durability and Clarity
The curing process is a critical step in UV flatbed printing, especially when working with transparent materials. Proper curing ensures that the ink adheres securely to the substrate and that the final print is durable, scratch-resistant, and resistant to chemical and environmental degradation. UV flatbed printers are equipped with UV lamps or LED arrays that emit high-intensity ultraviolet light. The exposure time and intensity of the UV light must be carefully controlled to achieve optimal curing without causing heat-related issues, such as distortion or discoloration of the transparent material.
For transparent materials, it is essential to avoid over-curing, which can lead to yellowing or hazing of the substrate. Conversely, under-curing can result in poor adhesion and ink smearing. Therefore, printer manufacturers often provide specific curing profiles for different types of inks and substrates, allowing operators to fine-tune the curing process for optimal results.
Material Handling: Challenges and Solutions
Printing on transparent materials presents unique challenges in terms of material handling. Transparent substrates, such as glass or clear plastic, can be delicate and prone to scratching or static buildup. Proper handling and support are essential to prevent damage during the printing process.
UV flatbed printers are designed to accommodate a wide range of substrate thicknesses and sizes. They typically feature adjustable beds and vacuum systems to hold materials securely in place during printing. For particularly delicate or flexible transparent materials, additional support structures or adhesive backers may be required to ensure stability and prevent warping or sagging.
Static electricity can also be a problem when handling transparent materials, as it can cause dust and debris to adhere to the surface, affecting print quality. To mitigate this issue, printers may be equipped with static eliminators or operators may use anti-static sprays or wipes to neutralize static charges before printing.
Post-Processing: Enhancing the Finish
After printing, transparent materials may require additional post-processing steps to enhance their appearance and durability. For example, a clear protective coating can be applied to the printed surface to provide extra scratch resistance and UV protection. This coating can be either a UV-curable varnish or a laminated film, depending on the specific requirements of the application.
In some cases, printed transparent materials may also undergo cutting, shaping, or assembly processes to create finished products. For example, printed transparent acrylic sheets may be cut and bent to form displays or signage, while printed transparent film may be laminated onto other substrates to create layered visual effects.
Printing on transparent materials with UV flatbed printers is a complex and multifaceted process that requires a thorough understanding of ink chemistry, printhead technology, curing processes, and material handling. By carefully selecting the right inks, utilizing advanced printhead technologies, controlling the curing process, and ensuring proper material handling and post-processing, it is possible to achieve stunning, high-quality prints on a wide range of transparent substrates.
As UV flatbed printing technology continues to evolve, it is likely that even more innovative solutions will emerge, further expanding the possibilities for printing on transparent materials. Whether for artistic expression, product decoration, or functional applications, the ability to print on transparent substrates with UV flatbed printers opens up a world of creative possibilities and offers numerous opportunities for businesses and individuals alike.