Technical Aspects of UV Flatbed Printing You Should Know
Technical Aspects of UV Flatbed Printing You Should Know
In the realm of digital printing, UV flatbed printing stands out as a versatile and efficient technology that has revolutionized the way prints are produced on a wide range of substrates. This innovative process utilizes ultraviolet (UV) light to cure ink instantly, resulting in high-quality, durable prints that can adhere to almost any surface. As businesses and individuals seek to enhance their visual communications through eye-catching signage, personalized products, and intricate designs, understanding the technical aspects of UV flatbed printing becomes crucial. This article delves into the key elements of UV flatbed printing that every enthusiast and professional should know.
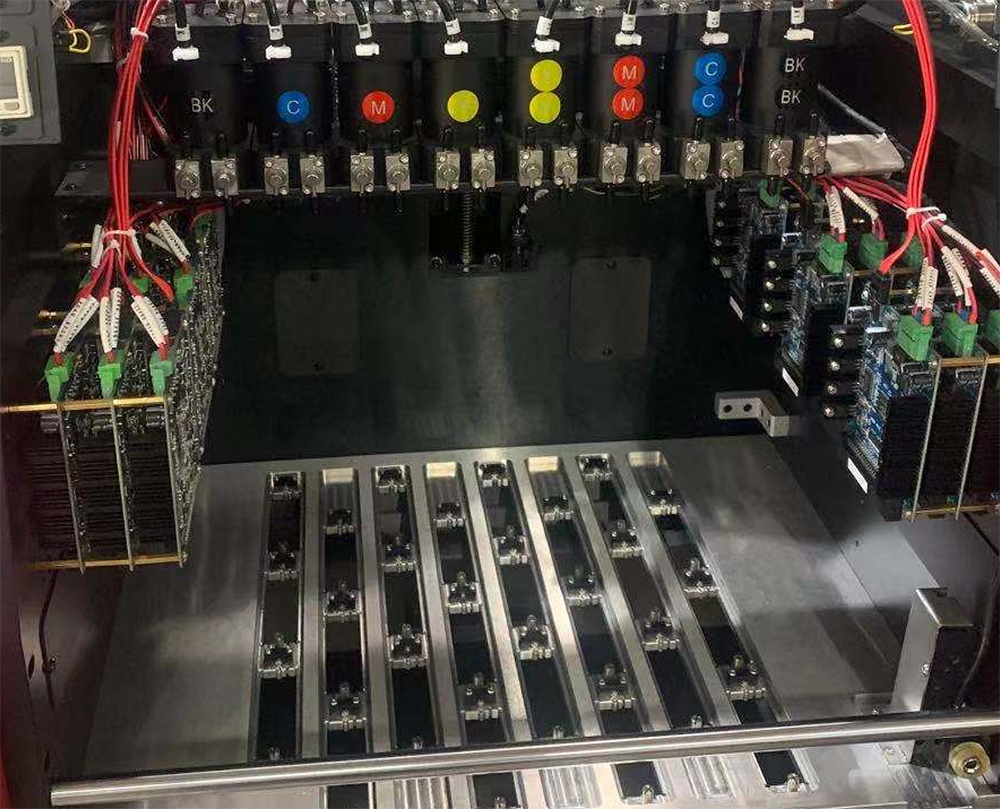
1. Fundamentals of UV Flatbed Printing
UV flatbed printing is a form of digital printing where ink is applied directly onto a flat surface using a print head equipped with thousands of nozzles. Unlike traditional printing methods that rely on heat or solvent-based inks, UV flatbed printers use UV-curable inks that solidify upon exposure to UV light. This immediate curing process eliminates the need for drying time, enabling faster production cycles and reducing the risk of ink smudging or bleeding.
2. Components of a UV Flatbed Printer
A typical UV flatbed printer consists of several essential components:
Print Head: This is the core of the printer, containing nozzles that precisely dispense ink onto the substrate. High-end printers often feature multiple print heads for faster printing speeds and enhanced color accuracy.
UV Lamps: These lamps emit UV radiation to cure the ink instantly after it is deposited. The intensity and duration of UV exposure are carefully controlled to ensure optimal ink adhesion and durability.
Substrate Table: The flatbed itself, where the material to be printed is placed. This table can be adjusted to accommodate various sizes and types of substrates, from rigid materials like metal and glass to flexible ones like vinyl and fabric.
Ink Supply System: This includes ink cartridges or reservoirs that hold the UV-curable inks, as well as the pumps and tubing that deliver the ink to the print heads.
Control Software: This software manages the entire printing process, including image processing, color management, and printer settings. It also allows for precise control over print quality, resolution, and ink usage.
3. Types of UV-Curable Inks
UV-curable inks come in different formulations, each tailored to specific applications and substrates. The most common types include:
Monomer Inks: These are the most flexible and versatile, suitable for a wide range of substrates. They offer good adhesion and are often used for general-purpose printing.
Oligomer Inks: With higher viscosity than monomer inks, oligomers provide better chemical resistance and durability. They are ideal for outdoor applications where the print may be exposed to harsh weather conditions.
Polymer Inks: These inks offer the highest level of durability and chemical resistance. They are typically used for industrial applications where the printed surface may encounter abrasive or chemical substances.
4. Print Resolution and Quality
One of the standout features of UV flatbed printing is its ability to produce high-resolution prints. Most modern UV flatbed printers can achieve resolutions of up to 1440 dpi (dots per inch), resulting in sharp, detailed images that retain their clarity even when viewed closely. The quality of the print is also influenced by factors such as ink drop size, print head technology, and the printer’s color management system.
5. Substrate Compatibility
UV flatbed printing excels in its ability to print on a vast array of substrates, ranging from traditional materials like paper and cardboard to more unconventional surfaces like wood, metal, glass, plastic, and even textiles. This versatility is due to the quick-curing nature of UV inks, which can bond effectively with most surfaces without the need for primers or pre-treatment. However, it is essential to choose the right ink formulation and adjust printer settings according to the specific substrate to ensure optimal adhesion and durability.
6. Color Management and Consistency
Achieving accurate and consistent color reproduction is crucial in UV flatbed printing. This is facilitated through advanced color management systems that utilize ICC (International Color Consortium) profiles. These profiles ensure that the colors displayed on the computer screen match those printed on the substrate, taking into account factors such as ink type, substrate characteristics, and viewing conditions. Regular calibration of the printer and monitoring of ink levels are also necessary to maintain color consistency over time.
7. Curing Process and Durability
The curing process is a critical aspect of UV flatbed printing. UV lamps emit light in the ultraviolet spectrum, which triggers a chemical reaction in the ink, causing it to harden and adhere to the substrate. The intensity and duration of UV exposure are carefully controlled to ensure complete curing without overheating the substrate or causing ink discoloration. Properly cured prints exhibit excellent durability, resistance to fading, scratching, and chemicals, making them suitable for both indoor and outdoor applications.
8. Production Efficiency and Cost-Effectiveness
UV flatbed printing offers significant advantages in terms of production efficiency and cost-effectiveness. The ability to print directly onto a wide range of substrates eliminates the need for additional processes such as mounting or laminating, streamlining production and reducing material waste. Furthermore, the instant curing process allows for faster turnaround times, increasing productivity and reducing labor costs. While the initial investment in a UV flatbed printer may be higher than that of traditional printing equipment, the long-term savings in time, materials, and labor often justify the expense.
9. Environmental Considerations
As environmental concerns grow, UV flatbed printing offers a more sustainable alternative to solvent-based printing methods. UV-curable inks are typically solvent-free, reducing emissions of volatile organic compounds (VOCs) and minimizing the environmental impact. Additionally, the efficient use of ink and substrates, along with the elimination of pre-treatment and post-processing steps, contributes to a greener printing process. Many UV flatbed printers also incorporate energy-saving features, such as LED-based UV lamps, which consume less power than traditional UV lamps.
10. Maintenance and Troubleshooting
Regular maintenance is essential to ensure the optimal performance and longevity of a UV flatbed printer. This includes cleaning the print heads, checking ink levels, and performing routine calibration. Troubleshooting common issues, such as nozzle clogged or ink adhesion problems, often involves adjusting printer settings, cleaning components, or replacing worn parts. Manufacturers typically provide detailed maintenance guides and technical support to assist users in keeping their printers in top condition.
Conclusion
UV flatbed printing represents a significant advancement in digital printing technology, offering unparalleled versatility, high print quality, and efficient production processes. Understanding the technical aspects of this technology, from the fundamentals of UV curing to the intricacies of color management and substrate compatibility, is crucial for maximizing its potential. Whether you are a professional printer, a designer, or a business owner looking to enhance your visual communications, mastering the art of UV flatbed printing can open up a world of creative possibilities and help you stay ahead in a competitive market. With its combination of speed, quality, and sustainability, UV flatbed printing is poised to remain a leading technology in the digital printing industry for years to come.