Technical Aspects of UV Ink Used in Flatbed Printers
Technical Aspects of UV Ink Used in Flatbed Printers
Flatbed printers have revolutionized the printing industry, offering versatility and precision in reproducing images and text on various surfaces. One of the key components contributing to their efficiency and effectiveness is UV ink. This article delves into the technical aspects of UV ink used in flatbed printers, exploring its composition, curing process, advantages, challenges, and future developments.
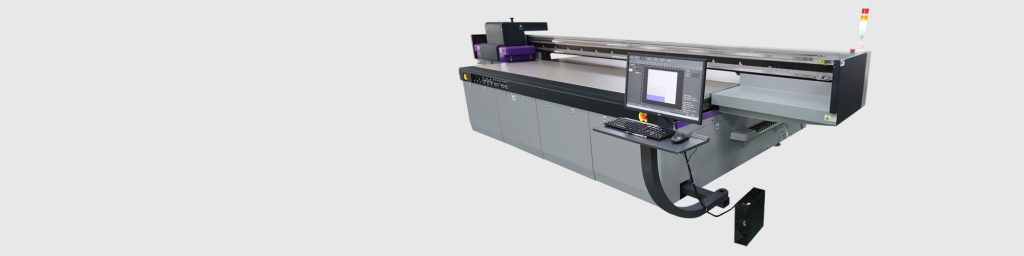
Composition of UV Ink
UV ink, also known as ultraviolet ink, is a type of ink that cures or dries when exposed to ultraviolet light. It is composed of several key components, including pigments or dyes, monomers, oligomers, photoinitiators, and additives. Each component plays a crucial role in determining the ink’s performance and characteristics.
Pigments or Dyes: These are the colorants responsible for the ink’s hue. Pigments are solid particles suspended in the ink, while dyes are soluble and can be dissolved in the ink base. Pigments are generally more durable and resistant to fading.
Monomers and Oligomers: These are the reactive components that form the ink’s polymer network during the curing process. Monomers are small molecules that can be linked together, while oligomers are larger molecules consisting of several monomers.
Photoinitiators: These are chemicals that absorb UV light and initiate the curing reaction. They are responsible for converting the UV energy into chemical energy, triggering the polymerization process.
Additives: These include stabilizers, surfactants, and other agents that enhance the ink’s performance. They can improve adhesion, reduce surface tension, and increase the ink’s shelf life.
Curing Process
The curing process of UV ink is a critical aspect of its application in flatbed printers. When the ink is exposed to UV light, the photoinitiators absorb the energy and undergo a chemical reaction, converting it into heat. This heat initiates the polymerization process, where monomers and oligomers link together to form a solid polymer network.
The curing process is rapid, typically taking only a few seconds. This allows for immediate handling and finishing of the printed materials without the risk of smudging or smearing. Additionally, the cured ink exhibits excellent adhesion to various substrates, including plastics, glass, metal, and even some textiles.
Advantages of UV Ink in Flatbed Printers
The use of UV ink in flatbed printers offers several advantages over traditional solvent-based or aqueous inks:
Instant Curing: UV ink cures immediately upon exposure to UV light, allowing for fast and efficient printing processes. This eliminates the need for drying time and enables immediate post-processing, such as cutting or laminating.
Durability: The cured ink forms a tough, durable film that is resistant to fading, scratching, and chemical degradation. This makes UV ink ideal for outdoor applications and products that require long-term durability.
Versatility: UV ink can be used on a wide range of substrates, including non-porous materials like plastics and metals. This versatility allows for printing on various products and surfaces, expanding the creative possibilities in the printing industry.
Environmental Friendliness: UV ink contains no volatile organic compounds (VOCs) and emits minimal odor during printing. This makes it a more environmentally friendly option compared to solvent-based inks, which can release harmful emissions into the air.
High Resolution and Detail: UV ink enables high-resolution printing, allowing for sharp images and fine details. This is particularly advantageous for applications that require precise graphics and text, such as packaging and signage.
Challenges and Limitations
While UV ink offers numerous benefits, it also presents some challenges and limitations in flatbed printing:
Cost: UV ink and the associated printing equipment, including UV lamps and curing systems, can be more expensive than traditional ink options. This initial investment may be a barrier for some businesses.
Health and Safety: Although UV ink is generally considered safer than solvent-based inks, it still requires proper handling and storage. Exposure to UV light during the curing process can also pose health risks if not managed appropriately.
Substrate Compatibility: While UV ink is versatile, it may not adhere well to all substrates. Some materials may require additional pretreatment or coating to ensure proper ink adhesion.
Ink Stability: UV ink can be sensitive to temperature and humidity, which can affect its viscosity and curing properties. Proper storage and handling are essential to maintain ink stability and print quality.
Future Developments
As technology continues to advance, the future of UV ink in flatbed printers looks promising. Researchers and manufacturers are exploring new formulations and additives to enhance ink performance and address current challenges.
Ink Formulation: Developments in ink chemistry are aimed at improving ink stability, reducing costs, and enhancing adhesion to a broader range of substrates. This includes the exploration of bio-based and renewable materials as ink components.
LED Curing Technology: Traditional UV curing systems use mercury-based bulbs, which can be costly and require frequent replacement. LED curing technology offers a more energy-efficient and environmentally friendly alternative, with longer lifespan and lower heat output.
Inkjet Innovations: Advancements in inkjet technology are enabling higher print speeds, finer resolution, and improved ink deposition control. This will further enhance the capabilities of UV ink in flatbed printers, allowing for even more versatile and efficient printing processes.
In conclusion, UV ink plays a vital role in the performance and versatility of flatbed printers. Its unique composition and curing process enable high-quality, durable prints on various substrates. While challenges and limitations exist, ongoing developments in ink formulation, curing technology, and inkjet innovations are poised to further enhance the capabilities and applications of UV ink in the printing industry. As technology continues to evolve, UV ink will remain a key component in driving innovation and creativity in flatbed printing.