Technical Challenges in Large Format UV Flatbed Printing
Technical Challenges in Large Format UV Flatbed Printing
Large format UV flatbed printing has revolutionized the printing industry by offering unparalleled versatility, precision, and efficiency in producing high-quality prints on a wide range of substrates. This technology employs ultraviolet (UV) inks that cure instantly upon exposure to UV light, enabling rapid turnaround times and vibrant, durable prints. Despite its many advantages, large format UV flatbed printing is not without its technical challenges. This article delves into the intricate hurdles that printers encounter, exploring issues related to ink adhesion, color management, printhead maintenance, media handling, and more.
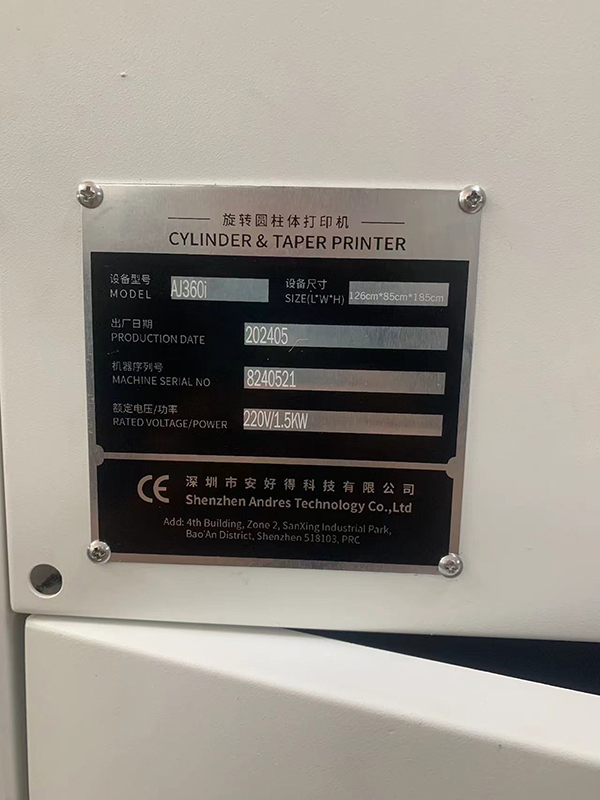
1. Ink Adhesion and Cure
One of the primary challenges in UV flatbed printing is ensuring optimal ink adhesion to various substrates. Unlike traditional inks that rely on evaporation or absorption, UV inks form a solid layer upon curing. Achieving proper adhesion requires a delicate balance between ink chemistry, substrate compatibility, and cure conditions.
Substrate Preparation: The surface characteristics of the substrate, such as porosity, texture, and coating, significantly influence ink adhesion. For instance, non-absorbent materials like glass or metal may require special coatings to promote adhesion. Printers must carefully select or pre-treat substrates to ensure the UV ink bonds correctly.
Ink Chemistry: UV inks are formulated with specific resins, pigments, and additives that react under UV light. The chemistry of these inks must be tailored to the substrate type to achieve both good adhesion and cure. Inks designed for flexible materials, for example, differ from those meant for rigid substrates.
Cure Conditions: The curing process itself presents challenges. Over-curing can lead to ink cracking or substrate damage, while under-curing results in ink that remains tacky and susceptible to smudging. Factors such as UV lamp intensity, cure speed, and distance from the print surface must be precisely controlled.
2. Color Management and Consistency
Maintaining accurate and consistent color reproduction is crucial in large format printing, especially for applications requiring high color fidelity, such as fine art reproduction or brand marketing materials.
Profiling and Calibration: Every printer, ink set, and substrate combination requires a unique color profile. Creating these profiles involves extensive color measurement and calibration to ensure that the printed output matches the intended colors. Regular calibration of the printing system is necessary to maintain color consistency over time.
Metamerism: UV inks can exhibit metamerism, where colors appear different under varying lighting conditions. This effect can be problematic for applications viewed under diverse lighting environments. Printers must select inks with stable color properties and consider the end-use lighting conditions during profiling.
Ink Aging: UV inks may undergo color shifts as they age, particularly when exposed to environmental factors such as sunlight or humidity. Ensuring long-term color stability requires careful selection of inks and possibly the application of protective coatings.
3. Printhead Maintenance and Nozzle Clogging
The printheads in UV flatbed printers are highly sophisticated, featuring tiny nozzles that dispense ink with precise control. However, these nozzles are prone to clogging, which can disrupt the printing process and affect print quality.
Nozzle Clogging: Ink residue, dust, or debris can accumulate in the nozzles, leading to clogs. Regular cleaning routines, such as automatic nozzle cleaning cycles and manual cleaning with specialized solutions, are essential to prevent clogging.
Printhead Alignment: Misalignment of printheads can result in banding, streaking, or other print artifacts. Ensuring precise alignment through regular maintenance and calibration is critical for achieving high-quality prints.
Ink Viscosity: The viscosity of UV inks must be carefully managed. Inks that are too thick can clog nozzles, while inks that are too thin may not provide the desired print density. Temperature and humidity control within the printing environment can help maintain optimal ink viscosity.
4. Media Handling and Registration
Handling a wide variety of media sizes and types is another significant challenge in large format UV flatbed printing. Achieving precise registration and consistent media feeding is crucial for accurate print placement and overall print quality.
Media Diversity: From thin flexible materials to thick rigid substrates, UV flatbed printers must accommodate a range of media. Different media require different feeding mechanisms and support systems to ensure they remain flat and stable during printing.
Registration Accuracy: Precise registration is essential, particularly for multi-layer prints or prints that require exact alignment with pre-printed elements. Advanced registration systems, such as those using cameras and sensors to detect media edges and fiducials, help ensure accurate print placement.
Media Warping: Some substrates, especially those that are heat-sensitive, may warp during the printing process due to the heat generated by the UV lamps. Printers must employ techniques such as using vacuum tables or cooling systems to minimize warping.
5. Environmental and Health Considerations
UV flatbed printing involves the use of chemicals, including UV inks and cleaning solutions, which can pose environmental and health risks if not managed properly.
Ink Disposal: UV inks and their byproducts must be disposed of in accordance with local regulations. Printers must establish protocols for ink recycling or safe disposal to minimize environmental impact.
VOCs and Air Quality: Although UV inks generally have lower volatile organic compound (VOC) emissions compared to solvent-based inks, they can still release harmful vapors. Proper ventilation and air filtration systems are necessary to maintain a safe working environment.
Operator Safety: Operators must be trained in safe handling procedures for UV inks and cleaning chemicals. Personal protective equipment (PPE), such as gloves, goggles, and respiratory masks, should be worn when handling these materials.
6. Technical Advancements and Future Trends
The field of large format UV flatbed printing is continually evolving, with technological advancements addressing many of the existing challenges.
Automation and AI: Increasing automation and the integration of artificial intelligence (AI) are improving print quality, reducing waste, and streamlining production processes. AI algorithms can optimize print settings, predict maintenance needs, and even automate color management tasks.
New Ink Technologies: Innovations in ink chemistry are leading to the development of inks with enhanced adhesion properties, improved color stability, and lower environmental impact. Inks that cure at lower temperatures or that are bio-based are examples of these advancements.
Hybrid Systems: Some printer manufacturers are developing hybrid systems that combine UV flatbed printing with other technologies, such as laser cutting or 3D printing, to further expand the capabilities of large format printing.
Large format UV flatbed printing offers a versatile and efficient solution for producing high-quality prints on a wide range of substrates. However, it is not without its technical challenges. Ensuring optimal ink adhesion, maintaining color consistency, preventing printhead issues, managing diverse media, and addressing environmental and health concerns are all critical aspects that printers must navigate. By staying abreast of technological advancements and adopting best practices, printers can overcome these challenges and harness the full potential of UV flatbed printing technology. As the industry continues to evolve, ongoing innovation and refinement will undoubtedly address many of the current hurdles, paving the way for even more sophisticated and capable large format UV flatbed printing systems in the future.