Technical Considerations for Large Format UV Flatbed Printing
Large format UV flatbed printing has revolutionized the printing industry, offering unparalleled versatility and precision in producing high-quality images on a wide range of substrates. This technology has found applications in various sectors, including advertising, signage, packaging, and even fine arts. The ability to print directly onto rigid materials such as wood, glass, metal, and plastics without the need for pre-treatment or primers is a game-changer. However, achieving optimal results in large format UV flatbed printing involves careful consideration of several technical aspects. This article delves into the key technical considerations that one must keep in mind to harness the full potential of UV flatbed printers.
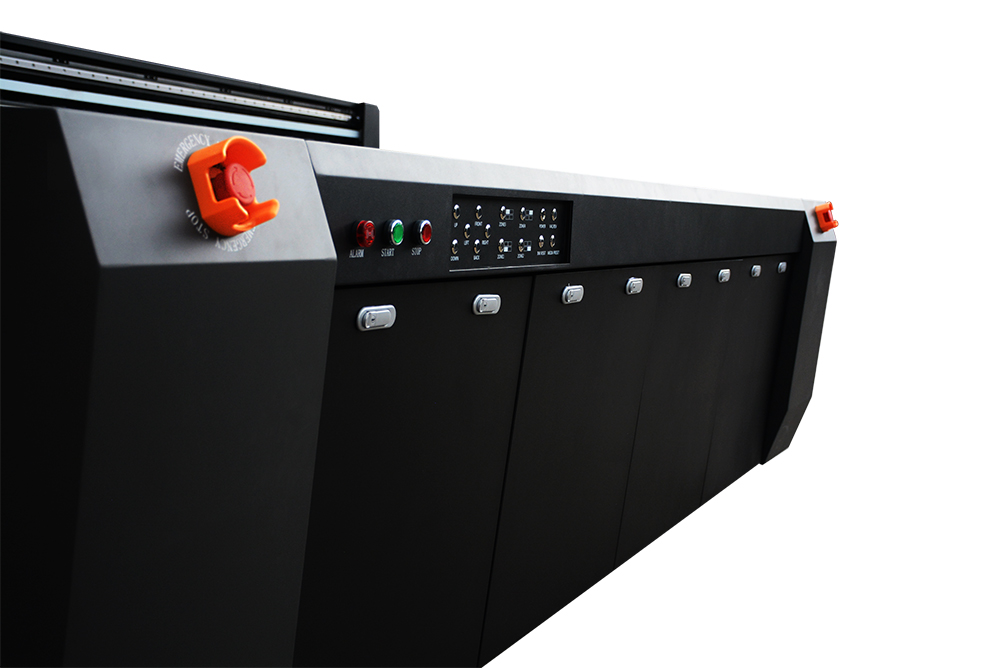
1. Understanding UV-Cured Inks
UV flatbed printers utilize UV-cured inks, which are liquid inks that solidify when exposed to ultraviolet light. This process, known as photocuring, offers several advantages over traditional solvent-based inks. UV-cured inks dry almost instantly, reducing the risk of smudging and allowing for faster production times. They also produce sharper images with better color saturation and durability.
One critical aspect of UV-cured inks is their composition. These inks typically contain photoinitiators, oligomers, monomers, and pigments. The photoinitiators are responsible for initiating the polymerization process when exposed to UV light. Oligomers and monomers form the backbone of the cured ink film, while pigments provide the color.
The choice of ink can significantly affect the print quality and the substrate’s compatibility. For instance, some inks may be better suited for flexible materials, while others perform optimally on rigid substrates. It is essential to select inks that are specifically formulated for the type of printing you intend to do and the substrates you plan to use.
2. Printer Resolution and Print Heads
The resolution of a UV flatbed printer refers to the number of ink droplets it can deposit per inch (dpi). Higher resolutions generally result in sharper and more detailed images. However, it is crucial to strike a balance between resolution and production speed. Higher resolutions often require more time to print, which can impact throughput.
Print heads are another critical component. They are responsible for depositing the ink onto the substrate. There are several types of print heads available, each with its own strengths and weaknesses. Piezoelectric print heads, for example, offer high precision and reliability but may be slower than thermal print heads. Thermal print heads, on the other hand, can operate at higher speeds but may sacrifice some precision.
When choosing a printer, consider the type of print heads it uses and their configuration. Some printers employ multiple print heads to increase speed and improve image quality. Additionally, the ability to adjust the drop size can enhance the printer’s versatility, allowing it to handle a wider range of applications.
3. Substrate Compatibility and Preparation
One of the most significant advantages of UV flatbed printing is its ability to print on a wide variety of substrates. However, not all substrates are created equal. Different materials may have different surface energies, porosities, and absorption rates, which can affect ink adhesion and cure quality.
It is essential to test the substrate for compatibility with the UV-cured inks and the printing process. Some substrates may require pre-treatment to improve ink adhesion or to ensure proper curing. For example, certain plastics may need to be corona-treated to increase their surface energy, while metals may require a primer to promote ink adhesion.
Proper substrate preparation can also involve ensuring that the surface is clean, dry, and free of contaminants. Dust, oil, and moisture can interfere with ink adhesion and cure quality, leading to poor print results.
4. UV Curing Systems
The UV curing system is a vital component of a UV flatbed printer. It is responsible for exposing the ink to the correct amount of ultraviolet light to initiate the polymerization process. There are several types of UV curing systems, including mercury vapor lamps, LED arrays, and hybrid systems.
Mercury vapor lamps have been the traditional choice for UV curing due to their high output and broad spectrum of UV light. However, they have some drawbacks, such as longer warm-up times, higher energy consumption, and the need for regular lamp replacement.
LED arrays, on the other hand, offer several advantages over mercury vapor lamps. They consume less energy, have a longer lifespan, and produce less heat. LED-based UV curing systems are also more compact and can be instantly turned on and off, which improves efficiency.
Hybrid systems combine the benefits of both mercury vapor lamps and LED arrays. They typically use LED arrays for the initial cure and mercury vapor lamps for the final cure, providing a balance between speed and cure quality.
When selecting a UV curing system, consider factors such as the type of inks being used, the substrates being printed on, and the production requirements. The goal is to achieve a proper cure without overexposing the ink or the substrate to UV light, which can cause degradation.
5. Color Management and Calibration
Color management is crucial in large format UV flatbed printing to ensure consistent and accurate color reproduction. It involves the use of color profiles, which describe the color characteristics of the printer, inks, and substrates.
Regular calibration of the printer is necessary to maintain color accuracy. Calibration involves adjusting the printer’s settings to ensure that the colors it produces match the colors in the digital file. This process may involve printing test charts and measuring the color values with a spectrophotometer.
It is also essential to use high-quality digital files with accurate color information. Low-resolution images or images with incorrect color profiles can result in poor print quality. When working with client-provided files, it is advisable to verify the color settings and make any necessary adjustments before printing.
6. Software and Ripping
The software used to control the UV flatbed printer, known as Raster Image Processor (RIP) software, plays a critical role in the printing process. RIP software converts digital files into a format that the printer can understand and processes the image data to optimize print quality and production efficiency.
When choosing RIP software, consider its compatibility with the printer and the types of files you will be printing. Look for software that offers advanced features such as color management, variable data printing, and automation capabilities.
In addition to RIP software, other software tools may be necessary for tasks such as design, image editing, and file preparation. It is important to have a workflow that integrates seamlessly with the printer and the RIP software to ensure smooth and efficient production.
Large format UV flatbed printing offers numerous advantages in terms of versatility, precision, and quality. However, achieving optimal results requires careful consideration of several technical aspects, including UV-cured inks, printer resolution and print heads, substrate compatibility and preparation, UV curing systems, color management and calibration, and software and ripping.
By understanding and addressing these technical considerations, you can harness the full potential of UV flatbed printing and produce high-quality prints that meet or exceed your clients’ expectations. Whether you are printing signs, packaging, or fine art, attention to detail in these areas will ensure that your prints are vibrant, durable, and visually appealing.