Technical Details of Printhead Alignment in UV Flatbed Printers
Technical Details of Printhead Alignment in UV Flatbed Printers
Introduction
In the realm of digital printing, UV flatbed printers have emerged as a powerful tool for producing high-quality, durable prints on a wide range of materials. These printers are renowned for their ability to print directly onto flat or semi-flat substrates, including glass, metal, wood, plastics, and ceramics, among others. At the heart of these printers lies the printhead, a critical component responsible for depositing ink with precision and accuracy. This article delves into the technical details of printhead alignment in UV flatbed printers, exploring the mechanisms, challenges, and best practices involved in ensuring optimal print quality.
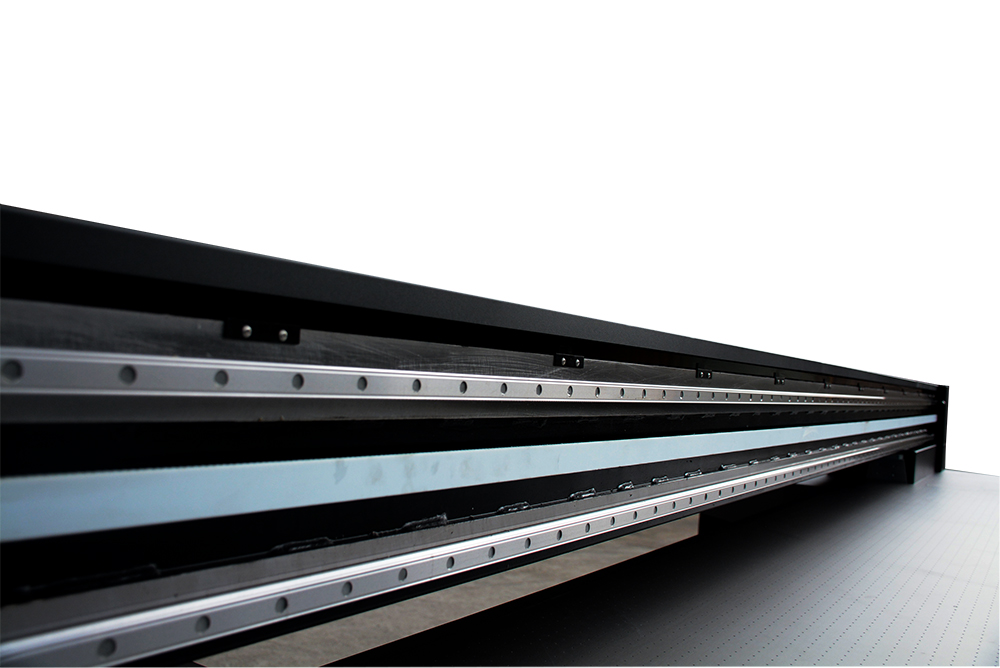
Understanding UV Flatbed Printers
UV flatbed printers, also known as scanning printers, operate by moving printheads back and forth across the print bed, building up color and detail in layers. The ink used in these printers is UV-curable, meaning it hardens upon exposure to ultraviolet light. This curing process occurs instantly, allowing for rapid printing speeds and high throughput.
The key advantage of UV flatbed printers lies in their versatility and precision. With large print beds, they can accommodate multiple parts or substrates simultaneously, enabling batch printing and mass customization. Furthermore, their digital nature eliminates the need for plates or screens, reducing setup time and costs.
Printhead Technology and Configuration
The printhead is the critical component that determines the quality and resolution of prints produced by UV flatbed printers. These printheads typically employ piezoelectric or thermal inkjet technology, each with its own set of advantages and limitations.
Piezoelectric Printheads
Piezoelectric printheads use piezoelectric crystals to generate pressure pulses that eject ink droplets from the nozzles. This technology is known for its high precision and consistency, allowing for fine control over droplet size and placement. Commonly used printheads in UV flatbed printers include those from manufacturers like Ricoh, Toshiba, and Konica Minolta.
Thermal Inkjet Printheads
Thermal inkjet printheads, on the other hand, use heat to vaporize ink within the nozzles, creating a bubble that forces ink out. While thermal printheads may not offer the same level of precision as piezoelectric ones, they are generally less expensive and suitable for lower-resolution applications.
Printhead Configuration
UV flatbed printers often employ multiple printheads arranged in a line or staggered configuration. This setup enables full-color printing using the CMYK (cyan, magenta, yellow, black) color model, with optional additional colors like light cyan, light magenta, white, and varnish for expanded color gamut and special effects.
Printhead Alignment Process
Printhead alignment is a critical step in ensuring optimal print quality from UV flatbed printers. The process involves precisely positioning the printheads relative to each other and the print bed to ensure that ink droplets are deposited in the correct locations, resulting in seamless, accurate prints.
Initial Setup
During the initial setup phase, the printheads are installed onto the printer’s carriage system and mechanically aligned using precision tools and fixtures. This mechanical alignment ensures that the printheads are parallel to the print bed and at the correct distance from it.
Software Calibration
Once the mechanical alignment is complete, software calibration is performed to fine-tune the printheads’ positions. This typically involves printing test patterns, such as color bars or grids, and analyzing them using specialized software. The software then adjusts the printheads’ positions in micro-increments to compensate for any deviations from the ideal alignment.
Bidirectional Printing Alignment
UV flatbed printers often support bidirectional printing, where the printheads move both left-to-right and right-to-left across the print bed. Bidirectional printing can significantly increase print speed but can also introduce alignment issues if not properly calibrated. Special attention is paid to ensuring that prints look consistent regardless of the printhead’s direction of travel.
Dynamic Alignment
In addition to initial and software-based calibration, some UV flatbed printers employ dynamic alignment systems that continuously monitor and adjust printhead positions during the printing process. These systems use sensors and algorithms to detect and correct for any minor deviations that may occur due to mechanical wear, temperature changes, or other factors.
Challenges and Solutions
Alignment Accuracy
Achieving precise printhead alignment can be challenging, particularly at high resolutions. Even small deviations in printhead positions can result in visible artifacts like banding, color shifts, or registration errors. Manufacturers address this challenge by using high-precision components and robust calibration routines.
Material Variability
The wide range of materials that UV flatbed printers can print on introduces additional complexity to the alignment process. Different materials may have varying surface textures, porosities, and absorption rates, which can affect ink deposition and cure times. To compensate for these differences, printers often include adjustable settings for ink volume, cure intensity, and other parameters.
Maintenance and Durability
Maintaining printhead alignment over time can be challenging, particularly as printheads wear down and components age. Regular maintenance, including cleaning, replacement of worn parts, and periodic recalibration, is essential to ensuring consistent print quality.
Environmental Factors
Environmental factors like temperature, humidity, and vibration can also affect printhead alignment. UV flatbed printers are typically designed to operate within specific environmental ranges to minimize these effects.
Best Practices
To ensure optimal printhead alignment and print quality in UV flatbed printers, several best practices are recommended:
Follow Manufacturer Recommendations: Carefully follow the manufacturer’s instructions for printhead installation, alignment, and maintenance.
Regular Calibration: Perform regular software calibration using test patterns and specialized software to maintain printhead alignment.
Use High-Quality Materials: Use materials that are compatible with the printer and ink system to minimize variability in ink deposition and cure times.
Maintain a Controlled Environment: Operate the printer within the recommended environmental ranges to minimize the effects of temperature, humidity, and vibration.
Regular Maintenance: Perform regular maintenance tasks like cleaning printheads, replacing worn parts, and checking mechanical components to ensure optimal performance.
Train Operators: Provide training to operators on proper printer use, maintenance, and troubleshooting procedures.
Conclusion
Printhead alignment is a critical aspect of ensuring optimal print quality in UV flatbed printers. The process involves precise mechanical and software-based calibration, as well as ongoing maintenance and environmental control. By following best practices and using high-quality components, manufacturers and end-users can achieve consistently high-quality prints on a wide range of materials. As UV flatbed printer technology continues to evolve, so too will the techniques and tools used to align printheads, driving further improvements in print quality and productivity.